Pushing the Limits: Carbon Fiber in Battery Packaging
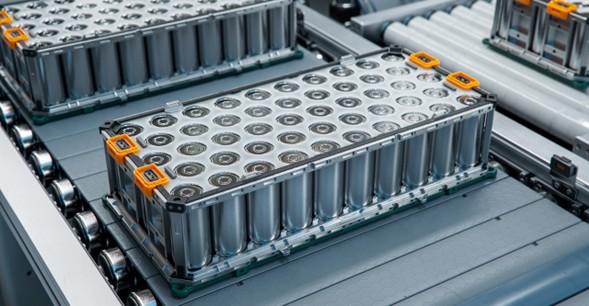
Polymer-based solutions pave the way for composite materials to meet the strict demands of modern energy storage.
Carbon fiber reinforced polymer (CFRP) materials have carved out space in advanced structural applications. As industries look to integrate batteries into structural components, CFRP emerges as a promising candidate for support and housing energy systems. A recent study, Permeability and barrier layer properties of a woven carbon fibre polymer composite as battery packaging, puts this potential under the microscope, evaluating how woven CFRP laminates behave as Li-ion polymer (LiPo) battery packaging.
You can also read: Polymeric Interface Enhances Lithium-Batteries Efficiency.
This study examines a composite laminate of plain-weave carbon fabric in a bisphenol-A epoxy matrix, manufactured via vacuum bag resin infusion. The research evaluates how the CFRP withstands long-term exposure to water and battery electrolyte, testing its structural strength and barrier effectiveness.
Stable Under Electrolyte Exposure
Mechanical testing in tension, compression, and bending showed that CFRP retains strength after long-term immersion in LiTFSI-based electrolytes. Therefore, this performance is promising for designers of structural battery parts such as current collectors and electrodes exposed to electrolytes. Although the composite absorbs around 0.4% electrolyte by weight, it shows no statistically significant loss in mechanical properties. In contrast, water immersion caused greater absorption, exceeding 1%, and moderately decreased flexural performance. However, tensile and compressive strength remained largely intact, indicating CFRP’s resilience in harsh conditions with minimal degradation. CFRP continues to perform effectively under mechanical stress, especially when electrolyte exposure is limited to surface regions.
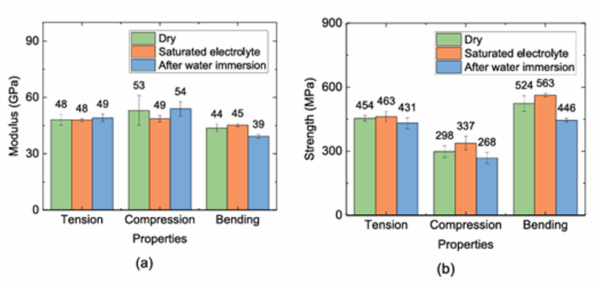
Mechanical properties including (a) modulus and (b) strength of CFRP laminate at various immersion conditions. Courtesy of Permeability and barrier layer properties of a woven carbon fibre polymer composite as battery packaging.
The Barrier Bottleneck
The key challenge for CFRP in battery packaging lies in its permeability to water vapor and oxygen. Two indicators help evaluate this: WVTR (Water Vapor Transmission Rate) and OTR (Oxygen Transmission Rate). WVTR measures the amount of water vapor that passes through a material over time, while OTR does the same for oxygen gas. In both cases, lower values indicate better barrier performance.
In this study, the CFRP laminate showed WVTR and OTR values much higher than those of aluminum foil, a common standard for battery packaging. That difference is critical. Even small amounts of moisture or oxygen inside a battery can reduce performance, raise internal resistance, or trigger unwanted chemical reactions. For any packaging material in direct contact with sensitive battery components, strong resistance to permeation is essential.
However, these findings highlight key opportunities for optimizing CFRP. The polymer matrix acts as a continuous, tunable phase that can easily incorporate targeted reinforcements, many of which build on existing material technologies.
Building Better Barriers with Polymers
Contrary to disqualifying CFRP, this study establishes methodological approaches for performance optimization within the composites field. Promising development pathways include:
- Hybrid Layers
Adding a thermoplastic barrier layer (like a polyethylene-acrylic acid ionomer) to CFRP can dramatically reduce permeability. These hybrid structures maintain the strength of composites while adding the protective benefits of specialized films.
- Matrix Innovation
Switching from epoxy to low-permeability thermoplastics like polyvinylidene chloride could help reduce diffusion of gases and moisture. These polymers already perform well in food and pharmaceutical packaging, battery enclosures could benefit next.
- Nanoparticle Enhancement
Adding nanofillers like titanium dioxide or magnesium oxide to the polymer matrix can reduce gas flow through the material. This method takes advantage of the polymer’s inherent flexibility and compatibility with additive integration.
- Architectural Adjustments
Thin-ply composites, with fewer fiber undulations and higher fiber volume, have shown better gas barrier properties in other applications. These architectures could tighten the structure and reduce permeation pathways.
Rethinking Battery Enclosures
The study reinforces CFRP’s value in structural energy storage components, especially where contact with electrolytes occurs. Its mechanical stability, even after prolonged immersion, shows real promise. However, when used as external battery enclosures, the laminate’s high water and oxygen transmission rates suggest a need for barrier enhancements. For now, CFRP laminates have applications as current collectors and electrodes exposed to the electrolyte.
Nevertheless, this creates an opportunity, not a setback. By applying solutions rooted in polymer science, such as barrier films, nanoparticle-filled matrices, or low-permeability thermoplastics, CFRP can evolve into a multifunctional battery housing material.