From Insulator to Conductor – Modifying Electrical Properties in Plastics
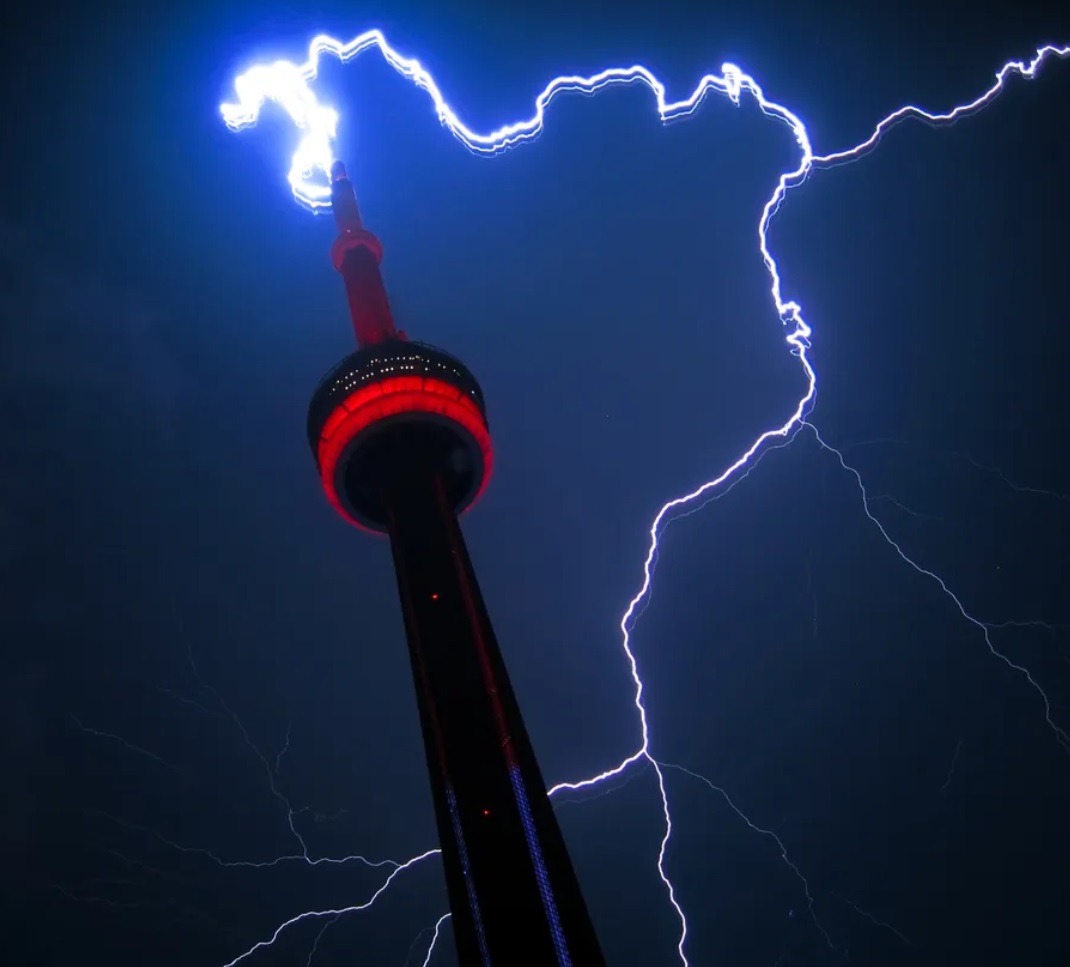
When two surfaces rub, static electricity builds as electrons move from one material to another during the contact and separation.
Polymers such as Polyethylene and Polypropylene have non-polar chains; therefore, they are not electrical conductors (insulators). A conductor carrying an electric charge can efficiently dissipate to the ground. However, an insulator does not have a conductive path for the charge to go to the ground. Because of this, static electric charges are built up.
You can also read: Modifying the Slip of Plastic Films with Additives.
This charge on the surface of a plastic product can damage packaged electronic components, making them a fire hazard in flammable atmospheres. Problems during package formation, sealing, or attracting dust can also make the product less attractive on store shelves.
A static charge can be dissipated from a non-conductive material by exposing it to a field of ionized air or radioactive ions. This procedure will dissipate an existing static charge but will not prevent a new one from building up after removing the material. The most efficient method for dissipating a static charge on an insulating material is to make it conductive enough to carry the charge to the ground.
There are several technical alternatives to modify the electric conductivity of plastics to reduce static charge buildup:
Antistatic Additives
You can make a plastic static-dissipative by incorporating specific hydrophilic chemicals. Manufacturers often apply these chemicals topically as external antistatic agents, which provide only temporary protection. Regular handling can remove them from the surface, reducing their effectiveness.
Alternatively, processors can blend internal antistatic agents directly into the polymer during extrusion. These agents gradually migrate to the surface of the finished plastic product. Once on the surface, they attract environmental moisture, forming a microscopic water layer. This layer conducts electricity well enough to dissipate static charges.
However, the performance of internal antistatic agents depends on the relative humidity of the environment, as insufficient moisture can limit their effectiveness.
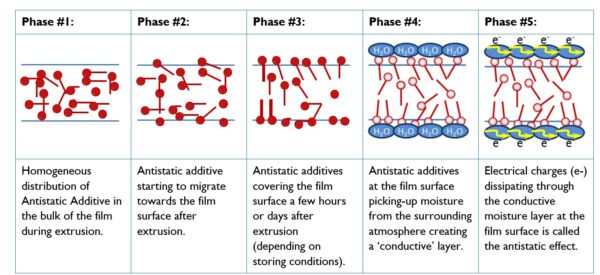
Mechanism of migration of antistatic additives in polyolefin films. Courtesy of Ampacet Corporation.
Antistatic agents fall into two main categories: ionic and nonionic. Ionic antistatic agents include both cationic and anionic compounds. Among the cationic types, manufacturers often use quaternary ammonium, sulfonium salts, and phosphonium compounds. For anionic agents, they typically employ sodium salts of phosphates or sulfonates. Because of their polarity, experts recommend ionic antistatic agents for use with polar resins such as PVC.
Nonionic Antistatic Agents
In contrast, nonionic antistatic agents consist of compounds like glycerol esters of fatty acids, diethanolamides, and ethoxylated tertiary amines. These are more commonly applied to nonpolar materials like polyolefins.
Specifically, processors frequently use glycerol esters as antistatic agents in polyethylene and polypropylene. However, their effectiveness is short-lived, lasting only one to two months. For longer-term performance, ethoxylated amines and amides offer greater durability. Amine-type agents, while highly effective, tend to react chemically with polycarbonate, a material widely used in electronic circuit boards. Therefore, they are unsuitable for such applications.
Furthermore, amine-type antistatic agents have limited FDA approval, which restricts their use in food-contact applications. Nevertheless, they remain among the most effective antistatic options. Amide-based agents also have limited FDA approval, though their approved use is broader than that of amines. In contrast, esters carry FDA approval for use at any concentration, making them highly versatile in regulated applications.
Inert Conductive Fillers
Polymers can also achieve resistivities in the conductive range (<106 ohms/sq) by adding electrically conductive fillers, which form an interconnecting or percolation network that dissipates static charge. The most common are carbon black (high surface-to-weight ratio) and metallic fibers. A high filler loading is required to achieve an adequate level of conductivity. Therefore, the mechanical properties of the product may be affected. Carbon blacks are often the most economical alternative. They have a permanent effect, regardless of time and environmental conditions.
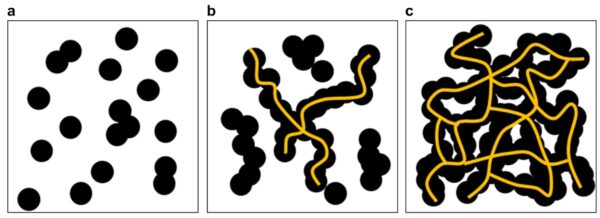
Schematics of percolation thresholds of CB/polymer composites. Orientations of carbon black in polymer matrix: carbon black was (a) disconnected, (b) partially connected, or (c) fully connected. Courtesy by Electrical percolation threshold of carbon black in a polymer matrix and its application to antistatic fiber | Scientific Reports.
Non-migrating Polymeric Antistatic Agents
These materials form a percolation network using a clear ionomeric polymer, which requires high loadings to achieve effective antistatic properties in polyolefin films. Due to their high cost, manufacturers recommend using them specifically in the skin layers of multilayer films. Unlike other antistatic agents, these materials do not rely on atmospheric humidity and deliver an immediate, permanent antistatic effect.
Measurement of Antistatic Properties
Engineers commonly use two properties to measure the antistatic performance of a plastic part: surface resistivity and static decay time.
- Surface Resistivity: It is the electric resistance of a part on its surface and is measured in Ohms. It can be tested in accordance with ASTM D257-76, “D-C Resistance or Conductance of Insulating Materials”. The higher the resistance, the greater the insulation. The greater the insulation, the more susceptible a material is to static building.
- If a part has surface resistivity in the range of 109 to 1012 Ohms/sq, it is considered antistatic. A sample having surface resistivity > 1012 Ohms/sq is considered insulative. Typically, PE and PP without any antistatic agent have surface resistivities in the range of 1015 to 1016 Ohms/sq.
Static Decay Time (or Charge Decay Time):
Testers measure static decay rate in seconds, defining it as the time needed to dissipate a specific fraction of an applied 5 kV static charge. They perform this test according to Federal Test Method 4046, Standard 101C, “Electrostatic Properties of Materials.” If a sample fails to retain the applied 5 kV charge, it shows no measurable antistatic performance.
Experts typically evaluate a product’s antistatic performance by comparing it to a standard specification established by a recognized standards organization. These specifications define the test conditions for assessing antistatic behavior, along with acceptable limits for static decay time and surface resistivity.
The most used specifications are “NFPA-99” and “Mil-PRF-81705D” (commonly known as “Military spec.”), which are described below:
- NFPA-99: Test conditions: 50% Relative Humidity, 73°F. Static decay time for 10% cutoff (90% dissipation of 5 kV) < 0.5 sec; or Surface resistivity < 1011 Ohms.
- Mil-PRF-81705D: Test conditions: 12% Relavite Humidity, 73°F. Static decay time for 0% cutoff (99% dissipation of 5 kV) < 2.0 sec, and Surface resistivity < 1012 Ohms
In conclusion, static charge in plastic products creates challenges during both processing and end use. Engineers and manufacturers can choose from various technical solutions to address this issue. However, to select the most effective option, they must evaluate several key factors—such as the required surface resistivity, target static decay time, relevant standards, desired duration of antistatic performance, and the type of polymer involved.