Optimizing Thermoset Epoxies for Additive Manufacturing with Sparse Infill
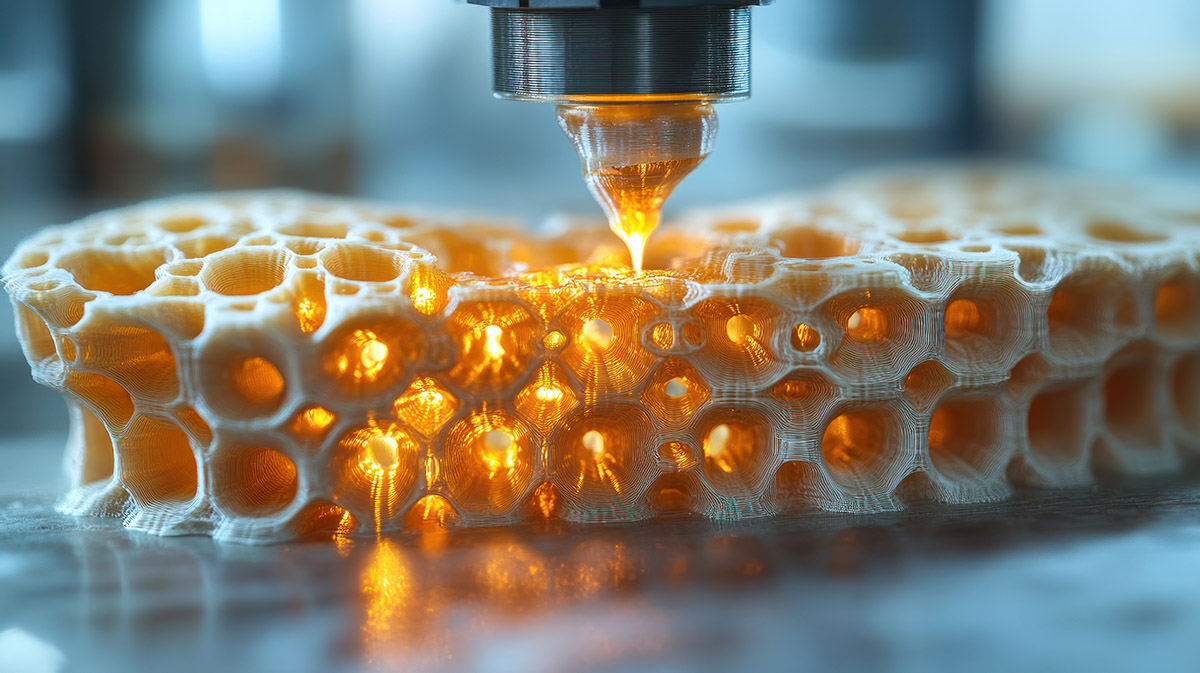
Michigan State University researchers unveiled novel thermoset epoxies capable of bridging unsupported gaps in sparse infill structures at ANTEC® 2025.
Sparse infill structures offer significant advantages in weight reduction and time savings. However, fully realizing these benefits requires materials that can effectively bridge unsupported gaps. Therefore, Mitchell Delemeester and Krishnamurthy Jayaraman conducted a study showcasing new thermoset resins for extrusion deposition additive manufacturing (EDAM). These materials exhibit enhanced rheological properties, significantly improving sag resistance in sparse infill structures.
You can also read: High-Performance 3D Printing with Photosensitive PEEK Ink.
Discovering Novel Formulations
Thermoset resins, often referred to as “inks,” require rheology-modifying additives to achieve yield stress behavior and strong shear thinning. In this study, researchers used Diglycidyl Ether of Bisphenol-A (DGEBA) as the resin base and tested three additives: montmorillonite-sepiolite clay, micronized amide, and carbon nanotubes (CNTs).
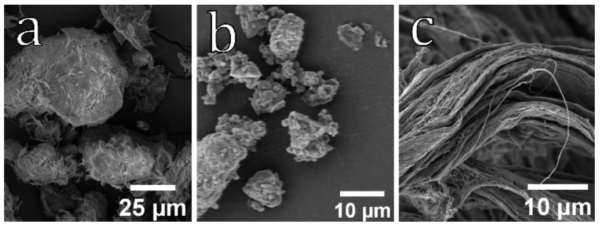
The figure illustrates: (a) Montmorillonite-sepiolite agglomerates, with surface fibrils from sepiolite measuring approximately 5 μm in length; (b) Micronized amide particles characterized by a rounded shape and a wide range of particle sizes, with a reported D50 of less than 14 μm; and (c) Carbon nanotubes clustered into fibrous bundles, resembling a woven textile. Courtesy of Novel Thermoset Formulations for Additive Manufacturing of Structures with Sparse Infill.
The team first evaluated clay and micronized amide individually. Clay offered good elasticity and some sag resistance but showed poor pumpability due to high viscosity at low shear rates. In contrast, micronized amide provided moderate sag resistance and strong thixotropy, allowing the resin to flow under stress and recover. Despite these advantages, its yield stress (~550 Pa) was insufficient for large unsupported spans. Additionally, after heating, the structure weakened during extrusion, temporarily reducing mechanical strength.
Building on these findings, researchers decided to develop new hybrid formulations by incorporating CNTs into the micronized amide resin. The addition of CNTs significantly increased the yield stress—reaching 1400 Pa with 0.5 wt% CNT—and improved sag resistance. This enables the resin to bridge spans up to 20 times the nozzle diameter. However, extrudability decreased, making the material too viscous for fine nozzles (e.g., 18 gauge).
Despite this issue, the formulation with 15 wt% micronized amide and 0.5 wt% CNT proved to be the most effective combination.
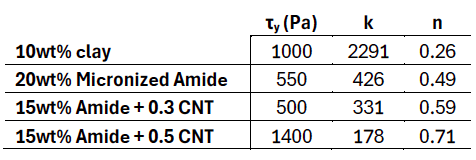
The table indicates that the clay exhibited a high consistency index (k), notably higher than that of the micronized amide suspensions. Incorporating CNTs into the amide formulation significantly increased the shear thinning exponent (n). Notably, adding 0.5 wt% CNT effectively boosted the yield stress, although it made extrusion through an 18-gauge nozzle very challenging. Courtesy of Novel Thermoset Formulations for Additive Manufacturing of Structures with Sparse Infill.
Connecting Lab Rheometer Data to Real-World Print Performance
Beyond developing a new resin formulation for EDAM, one of the study’s most significant breakthroughs was the connection between laboratory results and real-world printing performance. The research team conducted rheology and bridging tests to directly link material behavior to actual print outcomes.
To physically evaluate span bridging, they built a custom testing apparatus. While lab-scale measurements provided controlled, quantifiable data, the real-world simulation demonstrated whether those rheological properties translated into practical printing success.
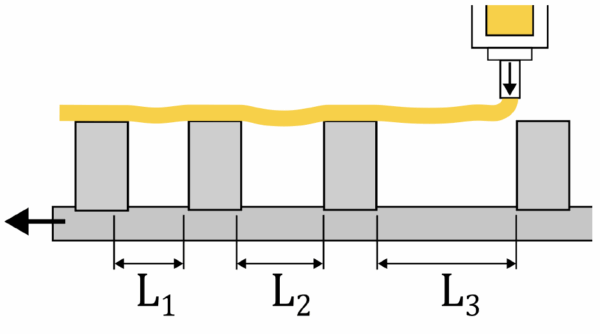
This figure illustrates the custom bridging fixture designed to precisely control and test span lengths during material deposition. Courtesy of Novel Thermoset Formulations for Additive Manufacturing of Structures with Sparse Infill.
The bridging fixture included a syringe pump with 18-gauge nozzles, a linear slide table with an aluminum bridging platform, and a camera system. This setup allowed the team to validate rheological findings from creep tests, oscillatory sweeps, and flow curves.
Formulation Innovations for Superior EDAM Performance
Overall, this study demonstrates the benefits of combining additives to achieve superior resin formulations. By mixing micronized amide with CNTs, the resin exhibited increased yield stress and enhanced sag resistance. This significantly improved bridging performance. In the best case, the resin showed excellent sag resistance. The total sag measured less than one nozzle height over a span of 20 times the nozzle diameter.
Researchers noted that further studies are needed to reduce the shear thinning exponent and increase the elastic modulus at high shear rates. Despite this, the results represent a significant advancement for EDAM of sparse infill structures. With these new formulations, such structures could become not only lightweight and cost-effective but also exhibit improved mechanical properties. This opens the door to broader applications across various industries.