Inside Materials – Prepreg Tack in Composites
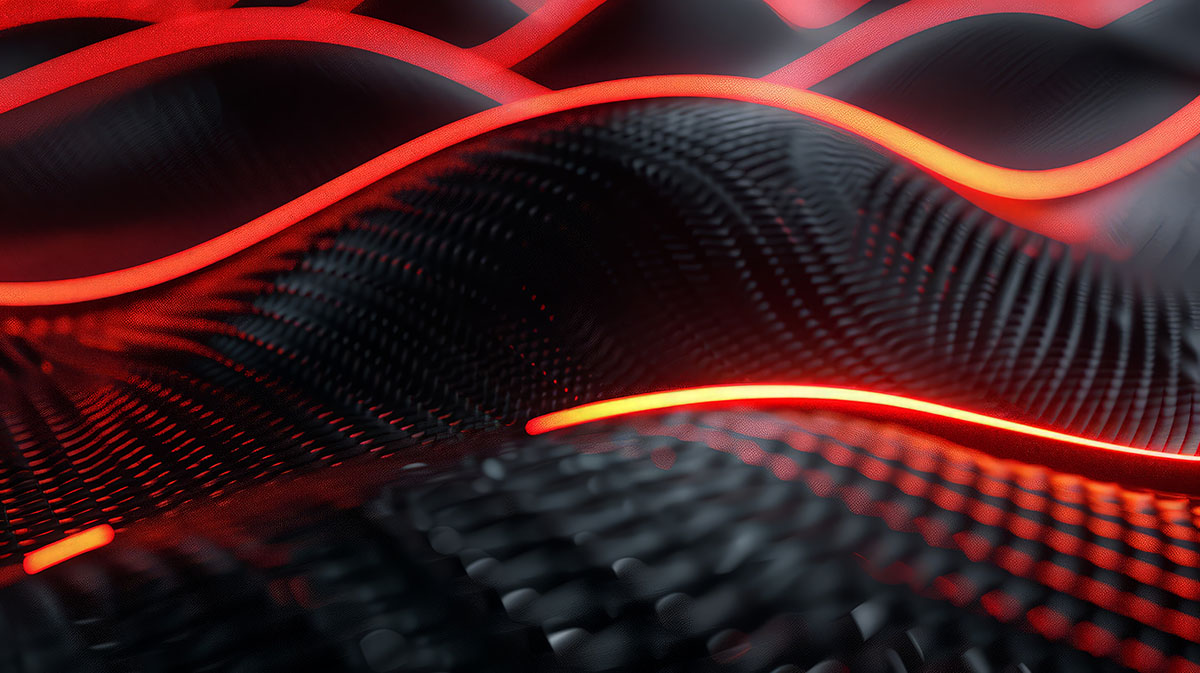
In the evolving world of composite materials, understanding prepreg tack has become essential, as it marks the success of the process.
This adhesive property directly influences the success of automated lay-up processes like Automated Fiber Placement (AFP) and Automated Tape Laying (ATL). With the increasing demand for lightweight and high-performance structures, especially in aerospace and automotive sectors, understanding and controlling prepreg tack is more essential than ever.
You can also read: A Closer Look at 3D Printing Materials: Composites.
What Is Prepreg Tack?
Prepreg tack refers to the inherent “stickiness” of partially cured fiber-reinforced composites before they are fully consolidated. Unlike traditional adhesives, tack is not caused by chemical bonding but by intermolecular forces like van der Waals interactions and hydrogen bonding. This property allows prepregs to adhere to substrates or previously laid plies without slippage or misalignment during lay-up.
Why Tack Matters in AFP/ATL Processes
Tack plays a dual role in lay-up processes. On one side, it ensures the prepreg stays firmly in place after being laid, especially when subjected to forces like peeling during backing paper removal. On the other hand, excessive tack can lead to machine jams, material misfeeds, and downtime due to adhesion to rollers and cutting tools.
Striking the right balance between too much and too little tack is therefore crucial. It directly impacts production quality, reduces defects like wrinkles, gaps, and overlaps, and ensures the overall efficiency of automated manufacturing systems.
Factors Influencing Prepreg Tack
Budelmann and colleagues categorize the influencing factors of tack into three key domains: process parameters, environmental conditions, and intrinsic material properties.
- Temperature
Temperature is a powerful control variable. Experiments show that prepreg tack typically follows a bell-shaped curve with temperature, reaching a maximum at a moderate range before declining due to excessive flow or loss of viscosity. Both tool and roller temperatures must be carefully controlled.
- Compaction Force and Dwell Time
Tack increases with both compaction force and time. These two factors define the true contact area between the prepreg and the substrate. However, increasing dwell time can conflict with productivity targets in AFP/ATL processes, as it reduces lay-up speed.
- Debonding Rate
The rate at which a prepreg is peeled from the substrate affects tack performance. Faster debonding rates increase adhesion-controlled failure, resulting in higher maximum tack force values but potentially lower work of adhesion.
- Contact Materials
The surface material in contact with the prepreg—like stainless steel, release films, or prior layers—also influences tack. Smooth, clean surfaces offer better adhesion than rough or contaminated ones. The presence of release agents significantly reduces tack, complicating first-ply lay-up procedures.
Measurement Challenges and Methods
Despite its importance, prepreg tack is not well-documented in material data sheets, often described vaguely as “low,” “medium,” or “high.” Two primary challenges have hindered progress:
- Lack of a standardized measurement method.
- Complex interplay of multiple influencing factors.
Common Measurement Techniques
- Probe Tack Test
Adapted from PSA testing, this method simulates the thumb test and provides quantifiable data on adhesion force and energy. Rheometers and universal testing machines are often used for precise control.
- Peel Tests
Using 90°, 180°, or T-peel angles, peel tests assess the progressive removal of a prepreg from a substrate. These tests help quantify the work of adhesion and provide force-displacement curves that describe tack behavior.
- Modified Techniques
Crossley’s floating roller method and Boeckl’s inline friction monitoring represent advances that better replicate real AFP/ATL conditions. These tools offer more realistic assessments and have been applied in industrial simulations and trials.
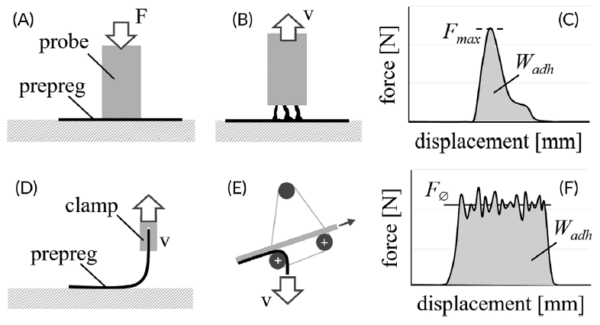
Upper figure: Compression, A, and tension/measurement, B, phases in probe tack test; lower figure: 90_, D, and floating roller, E, peel test setups; right figure: Characteristic force/displacement curves, C, and, F. Courtesy of Prepreg tack: A review of mechanisms, measurement, and manufacturing implication.
Environmental Effects on Prepreg Tack
- Ageing and Degree of Cure (DoC)
Prepregs are stored frozen to prevent premature curing. However, even cold storage allows some ageing. Ageing reduces tack over time by increasing matrix stiffness and reducing flowability. Material exposed to elevated temperatures loses tack faster, shifting its optimum processing temperature.
- Moisture and Humidity
Humidity is another critical factor. Moisture absorption can plasticize the resin, altering its viscosity and wetting behavior. Some studies report increased tack at moderate humidity, while others show reduced tack due to moisture-induced cure acceleration. This complex interaction requires more focused research.
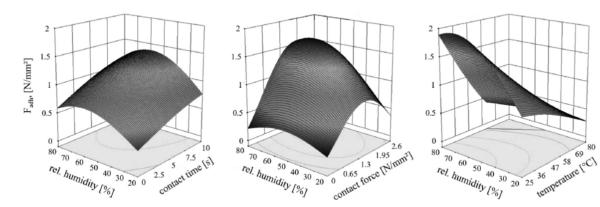
Response surfaces of tack (Fadh) measured as a function of relative humidity and second input variables (contact time, contact, and temperature). Courtesy of Prepreg tack: A review of mechanisms, measurement, and manufacturing implication.
Material Properties That Matter
Intrinsic prepreg features also play a role in tack performance.
- Resin Viscosity
The resin’s flow characteristics are central to forming a good bond. Dahlquist’s criterion—suggesting a modulus below 0.3 MPa for optimal contact—serves as a useful benchmark. However, prepreg-specific features such as fiber surface roughness mean that tack values may deviate from PSA-based predictions.
- Fiber Type and Areal Weight
Variations in fiber architecture, reinforcement volume, and surface texture influence both the mechanical and adhesive performance of the prepreg. Manufacturers need to tailor formulations based on both end-use properties and processing needs.
The Path Forward: Modeling and Optimization
Recent advances in modeling tack behavior are promising. Researchers have developed numerical models that split tack into bonding and debonding phases, using “degree of intimate contact” as a key variable. These models help predict defect formation, optimize parameters, and reduce waste in manufacturing.
However, full integration into AFP/ATL simulations remains challenging. Further work is needed to validate models against real-world trials, considering the diversity of materials and lay-up conditions.
Toward Smarter Prepreg Design
Prepreg tack is far more than a sticky inconvenience—it’s a finely tuned parameter that shapes the efficiency and quality of composite manufacturing. Manufacturers can better control tack to reduce defects and increase productivity by refining measurement techniques and understanding influencing factors.
As aerospace, automotive, and energy sectors continue adopting automated lay-up technologies, the demand for smart, data-driven control of prepreg tack will only grow. Future work should focus on standardizing test methods, improving modeling accuracy, and exploring innovative materials that offer both performance and processability.
Ultimately, mastering prepreg tack paves the way for faster, cleaner, and more reliable composite production—unlocking the full potential of advanced materials for modern engineering challenges.
To read the complete paper click here.