Tire Recycling: Feasibility and Profitability
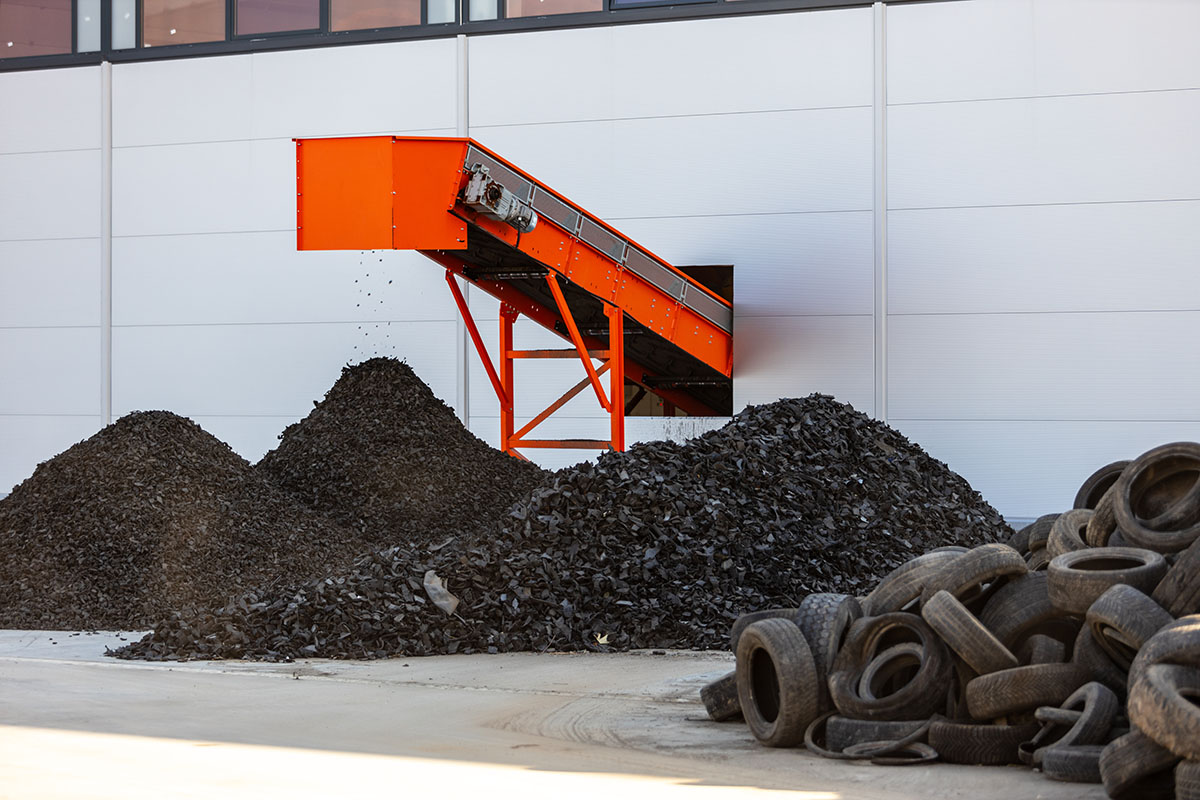
Tire recycling covers less than 30% of the new tires. As sustainability regulations tighten and raw material costs rise, the race is on to develop economically viable recycling methods that meet technical performance standards.
This article provides a comprehensive comparison of current tire recycling technologies, analyzing their feasibility, costs, and scalability for industrial adoption.
You can also read: Recycled Rubber – A Sustainable Alternative to Carbon Black in Tires
1. Mechanical Grinding (Granulation)
Technical Overview
Mechanical grinding is the most established tire recycling method, involving shredding tires into crumb rubber (1–10 mm particles). The process is simple but limited by material degradation—only 5–10% of the output can be reused in new tires.
Economic Feasibility
Cost: 0.10–0.30 per kg (cheapest method).
ROI: <2 years due to low infrastructure costs.
Market Demand: Declining in developed markets due to low-grade applications (e.g., playground surfaces, asphalt).
Applications: Low-cost, high-volume recycling where performance is not critical.
2. Pyrolysis (Thermal Decomposition)
Technical Overview
Pyrolysis heats tires in an oxygen-free environment, breaking them down into:
Oil (40–45% yield) – Used as industrial fuel.
Carbon black (30%) – Often downgraded for non-tire uses.
Steel & gas (byproducts).
Economic Feasibility
Cost: 0.50–1.00 per kg.
ROI: 5+ years due to high energy and emission control costs.
Market Trends: Strong in Asia (China processes 65% of global pyrolyzed tires).
Applications: Energy recovery but not high-quality tire recycling.
3. Chemical Devulcanization
Technical Overview
This method breaks sulfur bonds in vulcanized rubber, restoring plasticity. Companies like Evonik and Michelin are advancing this technology, enabling 20–30% recycled content in new tires.
Economic Feasibility
Cost: 0.80–1.50 per kg (expected to drop to $0.60/kg at scale).
ROI: 3–5 years, depending on policy incentives (e.g., EU’s 30% recycled content mandate).
Key Projects: Michelin’s BlackCycle initiative (targeting 2026 commercialization).
Applications: High-performance tire manufacturing.
4. Microwave/Ultrasonic Devulcanization
Technical Overview
Microwave and ultrasonic methods precisely break sulfur bonds without damaging rubber polymers. Lab tests show 15–25% recyclability in new tires.
Economic Feasibility
Cost: 1.20–2.00 per kg (high initial investment).
ROI: 7+ years due to R&D and scaling challenges.
Current Status: Limited to pilot projects (e.g., Bridgestone’s ENVISION program).
Applications: Premium tire production if costs decrease.
Comparative Analysis
Method | Recycled Content in New Tires | Cost/kg | ROI Timeline | Scalability |
---|---|---|---|---|
Mechanical Grinding | 5–10% | 0.10–0.30 | <2 years | High |
Pyrolysis | 0% (downgraded) | 0.50–1.00 | 5+ years | Medium |
Chemical Devulcanization | 20–30% | 0.80–1.50 | 3–5 years | High |
Microwave Devulcanization | 15–25% | 1.20–2.00 | 7+ years | Low |
Future Outlook & Industry Challenges
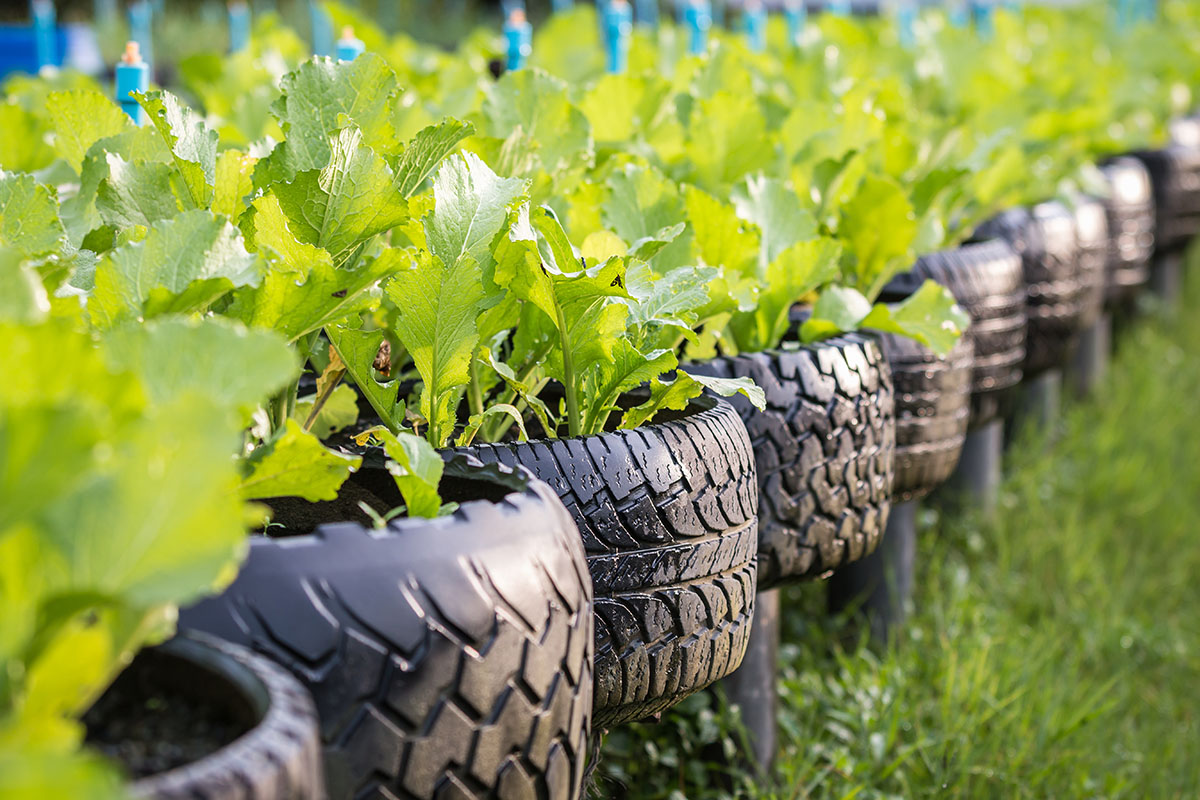
No single recycling method dominates—mechanical grinding leads in cost, chemical devulcanization in performance, and pyrolysis in energy recovery. The industry’s future hinges on scaling advanced methods while reducing costs, supported by stricter regulations and carbon pricing.
No single recycling method dominates—mechanical grinding leads in cost, chemical devulcanization in performance, and pyrolysis in energy recovery. The industry’s future hinges on scaling advanced methods while reducing costs, supported by stricter regulations and carbon pricing.
1. Policy & Regulations
EU’s ELT Directive mandates 30% recycled content by 2030.
U.S. Bipartisan Infrastructure Law funds sustainable material R&D.
2. Economic Barriers
Virgin rubber ($2.10/kg) remains cheaper than high-grade recycled rubber.
Carbon taxes could shift the balance toward advanced recycling.
3. Technology Roadmap
2024–2027: Hybrid mechanical-chemical systems gain traction.
2030+: Microwave scaling if renewable energy reduces costs.
To read more: Tire Recycling Market Size And Share | Industry Report, 2030