Solar Energy for Rotational Molding: A Case Study from Morocco
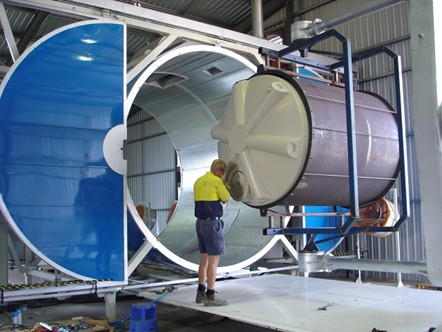
Solar thermal energy offers a viable way to cut emissions and energy costs in industry if it can affordably meet roto molding’s high heat demands.
The rotational molding process is essential to the plastics industry, and it is widely used to manufacture hollow plastic products such as tanks, containers, and vessels. However, this energy-intensive process relies heavily on fossil fuels to achieve the high temperatures (up to 300°C) required for melting plastics. With growing concerns over greenhouse gas emissions and volatile fuel costs, the industry is pressured to adopt cleaner, more sustainable alternatives. Solar thermal energy presents a promising solution, particularly in regions with abundant sunlight, such as Morocco. Today, we explore a real-world case study of integrating solar heat into rotational molding, highlighting its technical feasibility, economic benefits, and potential to reduce the environmental footprint of plastic manufacturing.
You can also read: Rotational Molding: Balancing Sustainability and Performance.
The Challenge: Energy Consumption in Rotational Molding
Rotational molding involves four key steps: charging the mold with plastic powder, heating and rotating the mold to distribute the melted plastic, cooling, and finally demolding the finished product. The heating phase, which accounts for most energy demand, traditionally depends on gas burners. In Morocco, where the industrial sector consumes 26% of the nation’s energy, this reliance on fossil fuels contributes significantly to CO₂ emissions and energy insecurity due to dependence on imported fuels. Solar heat for industrial processes offers a viable alternative. By harnessing solar thermal energy, industries can offset fossil fuel use, stabilize energy costs, and reduce emissions. The challenge lies in designing a system that meets the high-temperature demands of rotational molding while remaining cost-effective.
The Solution: Solar Thermal Integration
In this study, researchers from Morocco’s Institut de Recherche en Energie Solaire et Energies Nouvelles IRESEN developed a solar thermal system for a rotational molding plant in Casablanca. Because the process requires 300°C, they selected Linear Fresnel Reflectors (LFRs), arranged in parallel rows for cost-effective thermal performance.The system includes a thermal oil circuit, which transfers heat between the solar field and a heat exchanger that preheats air.
>Since solar output can vary, the system connects in series with a gas burner that activates automatically when solar input declines.
>Moreover, a control system monitors temperature continuously and adjusts both the oil flow rate and gas burner to maintain process stability.
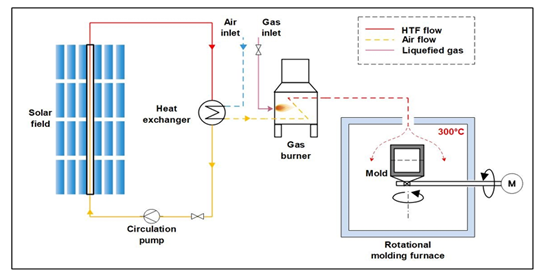
Scheme of the proposed solar heat integration in rotational molding processes. Courtesy of Solar Heat Integration in Rotational Molding Process: Case Study.
Key Design Features
Solar Field Configuration
The team evaluated six solar field sizes based on the Solar Multiple coefficient, which compares the solar field’s thermal capacity to the process demand. The optimal configuration used two FLT10v-60 collectors, achieving a 14% annual solar fraction.
Hybrid Operation
The solar field preheats air via a heat exchanger, while the gas burner supplements heat to reach the target 300°C when solar input is insufficient.
Financial Metrics
The team used Annual Life Cycle Savings and payback time to assess feasibility. The optimal design yielded €650,000 in savings over its lifecycle, with a payback period of 6.2 years.
Results and Benefits
The simulation, conducted using EBSILON® Professional software, demonstrated compelling results:
Energy Savings
The solar system provided up to 26% of the process heat during peak solar months (e.g., August), reducing gas consumption significantly.
Economic Viability
With a solar field cost of €300/m² and modest maintenance expenses (2% of initial investment), the project proved financially attractive. The 6.2-year payback period aligns with industrial investment horizons.
Environmental Impact
By displacing fossil fuels, the system cuts CO₂ emissions, supporting Morocco’s renewable energy goals and improving local air quality in Casablanca, a city plagued by industrial pollution.
Limitations and Future Research
While this study confirms the viability of solar heat for rotational molding, several opportunities remain to improve system efficiency and adoption.
Because the current solar fraction is 26%, incorporating thermal energy storage could increase this value and extend system functionality.
Moreover, stored thermal energy would allow continued heat supply during cloudy conditions or nighttime, thereby enhancing operational reliability and flexibility. This upgrade would reduce reliance on backup gas systems while maintaining consistent production temperatures.
For broader industry impact, manufacturers should consider implementing similar solar thermal systems, particularly in regions with high solar insolation. The Moroccan case study provides a replicable model that could be adapted to different production scales and local conditions. Future research should focus on optimizing collector efficiency and evaluating hybrid configurations that combine solar thermal with other renewable sources.
The plastics industry stands to gain substantial benefits from this technology, including reduced energy costs and lower carbon footprints. However, wider adoption may require supportive policies, financial incentives, and technology demonstration projects to build confidence among manufacturers. These developments could position solar-powered rotational molding as a standard sustainable practice in plastic manufacturing worldwide.
Call to Action
The integration of solar thermal energy into rotational molding is a win-win for the plastics industry. This case study from Morocco showcases how Solar Heat for Industrial Processes can reduce reliance on fossil fuels, lower operating costs, and mitigate environmental impacts, all without compromising production quality. For industrial stakeholders, the message is clear: solar heat is not just an environmental imperative but a smart business decision. As technology improves and costs decline, solar-powered rotational molding could become a standard in sustainable plastic manufacturing.