Smart Manufacturing: Precision Heat Control via Mechatronics and ML
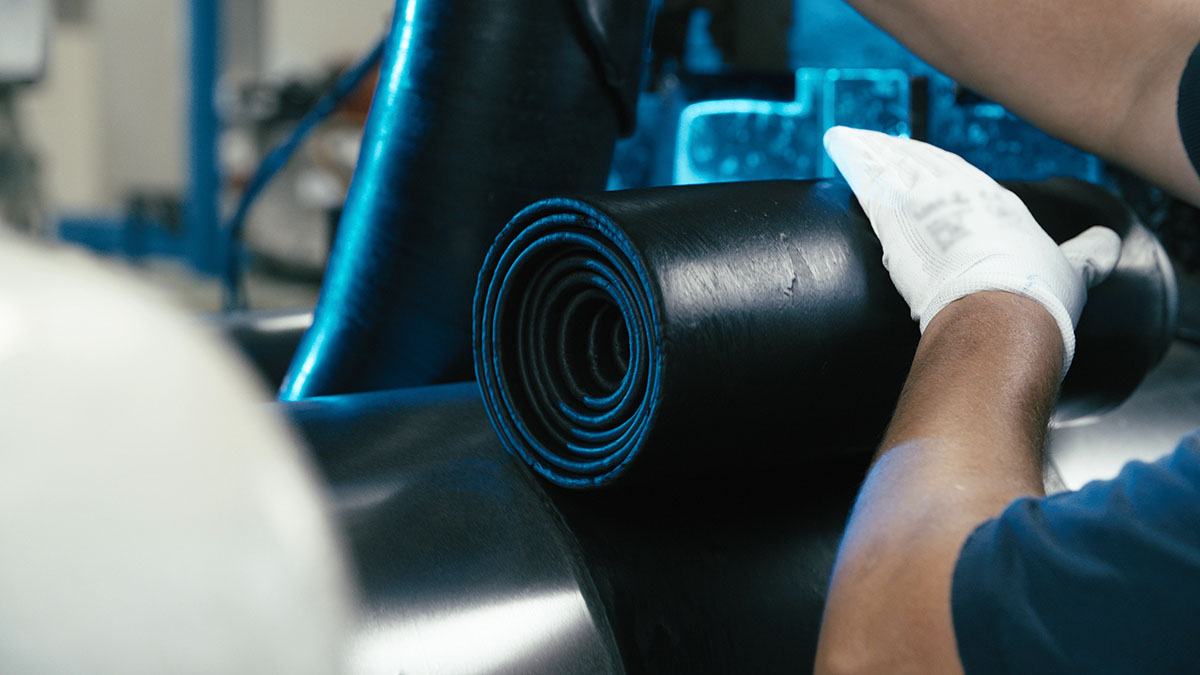
Mechatronics technology (MT) and improved machine learning (ML) algorithms improve rubber and plastic manufacturing temperature control.
Demand for rubber and plastic products has increased sharply. Temperature control systems (TCS) are a vital part of the manufacturing process for these products. Because of the characteristics of these materials, temperature control is difficult to describe and predict through mathematical modeling. Issues like temperature lag, high energy consumption, and complicated operation add difficulties to creating an effective TCS.
In a recent study, researchers combined a fuzzy neural network and MT to create a novel, circulating TCS. Using this approach, they optimized the system’s response time and accuracy.
You can also read: Redefining Quality Control with Machine Learning
Particle Swarm Optimization
This new fuzzy PID control algorithm (FPIDCA) technique uses fuzzy logic (FL) and conventional PID control strategies. Due to many changing variables, PID control can struggle to control circulating TCS in rubber and plastics manufacturing adequately. FL can change the PIDC settings online, helping to accommodate these changes.
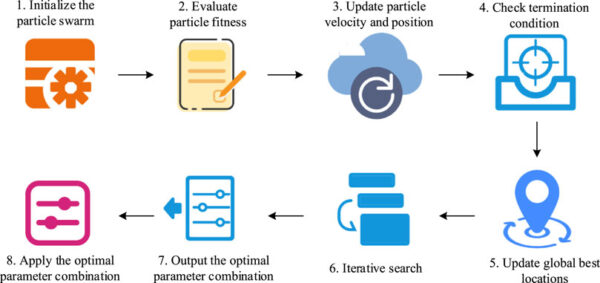
The eight steps of the novel temperature control algorithm’s operation process. Courtesy of Design of circulating temperature control system for rubber and plastic industry based on mechatronics.
Researchers introduced a particle swarm optimization (PSO) algorithm to counteract the constraints of affiliation function selection and fuzzy rule formulation. This function iteratively updates the position and velocity of particles to find their most optimal values. This study proposed an improved particle swarm optimization (IPSO) algorithm. When combined with the FPIDCA, this forms the IPSO-FZPID temperature control algorithm.
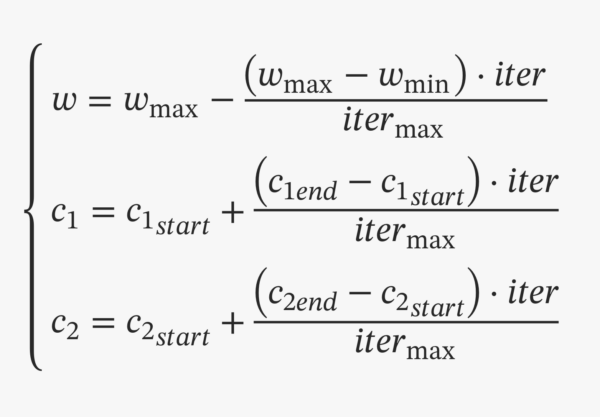
The adaptive IPSO-FZPID algorithm used in this study. Courtesy of Design of circulating temperature control system for rubber and plastic industry based on mechatronics.
Mechatronics combines mechanical engineering and automation to better optimize mechanical devices using electronic components. In the rubber and plastics industry, the circulating TCS is mainly comprised of six modules. These include temperature acquisition, temperature control, actuator, and circulating cooling modules. In this study, researchers used a low-pass filter to reduce sensor noise’s effect on the temperature data. Additionally, using a monitoring module allows the system to detect abnormal conditions so the system can enact protective measures. These six modules work together to precisely control temperature during rubber and plastic processing.
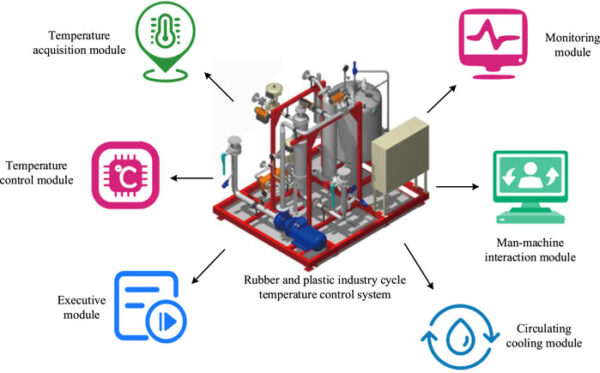
The six modules of the TCS in rubber and plastic applications. Courtesy of Design of circulating temperature control system for rubber and plastic industry based on mechatronics.
Promising Results for Industry Application
During simulation, researchers found that the novel TCS could quickly restore stability and suppress temperature fluctuations during disturbances. Resolving these issues quickly is vital in a manufacturing environment, as these disturbances can affect product stability and production efficiency. In a comparison of energy use, the TCS demonstrated a significantly better energy-saving rate than comparable systems.
In previous research, predictive control algorithms based on deep learning had high demands for computational resources. Additionally, the model training process was fairly complicated. Using the novel IPSO-FZPID algorithm reduced hardware requirements and computational complexity while maintaining high efficiency. Because of this, this algorithm has potential for realization in industrial applications.