Redesigning Marine Structures for Sustainability
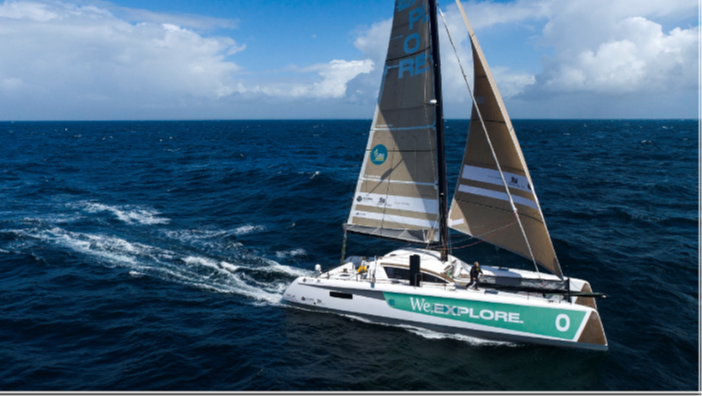
The maritime sector contributes to approximately 3% of global greenhouse gas emissions. The international shipping industry aims to reduce emissions by at least 20%, with a target of 30% by 2030 compared to 2008.
The marine industry has traditionally relied on glass fiber-reinforced thermoset polymers like polyesters and epoxies. However, there is now a significant shift towards sustainability due to the urgent need to reduce environmental impacts and greenhouse gas emissions.
You can also read: Natural Fibers are Trending for Plastic Reinforcement
Eco-Resins: Pioneering Sustainable Solutions
Companies offer products with up to 56% biobased components, improving their Life Cycle Assessment (LCA) profiles. However, the inability to recycle these resins limits their end-of-life sustainability.
Recent innovations in resin chemistry have led to the development of recyclable epoxy and unsaturated polyester formulations. A notable example is Recyclamine™ technology, developed in 2012. Boatyards can process these recyclable resins using existing technologies like infusion, which allows adoption without significant new investments.
The Future with Thermoplastic Matrix Polymers
Another method to facilitate the recycling of marine composites is adopting thermoplastic matrix polymers. Mechanical grinding and thermal forming cycles can recycle thermoplastic composites. This approach requires changes in the forming process, as thermoplastics need elevated temperatures and pressures to reduce viscosity and impregnate fiber reinforcements.
Various thermoplastic polymers, including polypropylene (PP), polylactic acid (PLA), and technical polymers like polyamides, are available for marine applications.
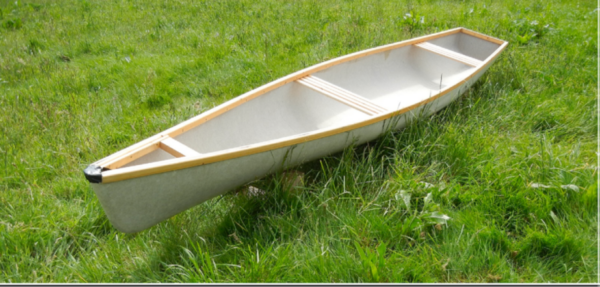
Flax/PLA canoe (4.40 meters long), produced by vacuum forming followed by autoclave processing, utilizing film stacking, as part of the NAVECOMAT project. Courtesy of Sustainable polymer composite marine structures: Developments and challenges.
Studies such as the NAVECOMAT project have explored the use of Flax/PLA composites for marine applications, highlighting the recyclability and biodegradability of these materials. Challenges remain, particularly in coating thermoplastic hulls due to their low surface tension, which inhibits adhesion.
Reduced Impact Sandwich Cores
Marine structures extensively use sandwich construction due to their excellent strength-to-weight ratio, and innovative core materials now offer more sustainable design opportunities. The two primary types of cores are foam and honeycombs.
Traditionally, manufacturers have used polyvinyl chloride (PVC) foams, but now they are shifting towards polyethylene terephthalate (PET) foams. Manufacturers can recycle PET foams and produce them from recycled PET, providing a more environmentally friendly alternative.
Honeycomb cores are another crucial component of sandwich structures. While the Nomex range, based on resin-impregnated aramid paper, remains widely known, lower-performance alternatives like PP-based honeycombs such as Nidaplast provide improved end-of-life possibilities.
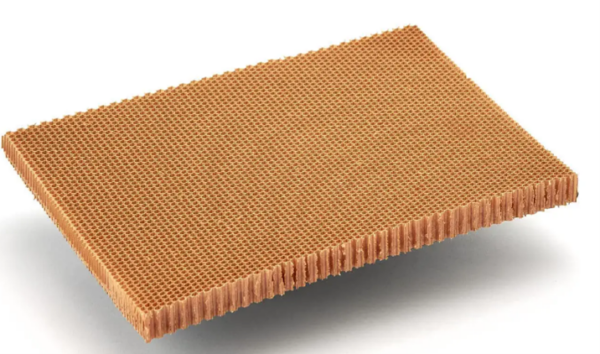
Nomex aramid honeycomb core material. Courtesy of GelComponents.
Challenges in End-of-Life Disposal
The marine industry’s shift towards composite materials has led to significant challenges in disposing of aging vessels. Unlike wooden boats, which degraded naturally over time, composite boats do not decompose easily, posing severe environmental concerns.
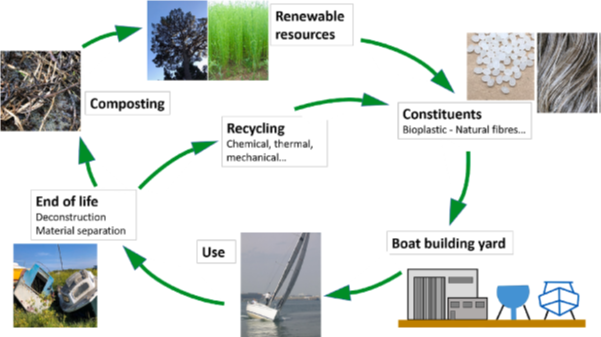
Illustration of how the concept of recyclability can be applied to bio composites. Courtesy of Sustainable polymer composite marine structures: Developments and challenges.
In France, the Association pour une Plaisance Eco-Responsable (APER) has been established to manage the dismantling and recycling of old boats, reflecting a growing recognition of the need for sustainable end-of-life disposal methods.
Replacing traditional thermoset matrix resins with recyclable thermoset resins or thermoplastics and reusing them through thermo-mechanical processes is a logical step toward sustainability. Additionally, developing new manufacturing methods will play a critical role. The marine industry’s transition to sustainable materials and practices is essential for reducing its environmental footprint. By adopting advanced composite materials, thermoplastic matrices, and innovative recycling technologies, industry can steer toward a greener future, ensuring the longevity and health of our planet’s marine ecosystems.