The Holistic Approach to Requalifying a Resin
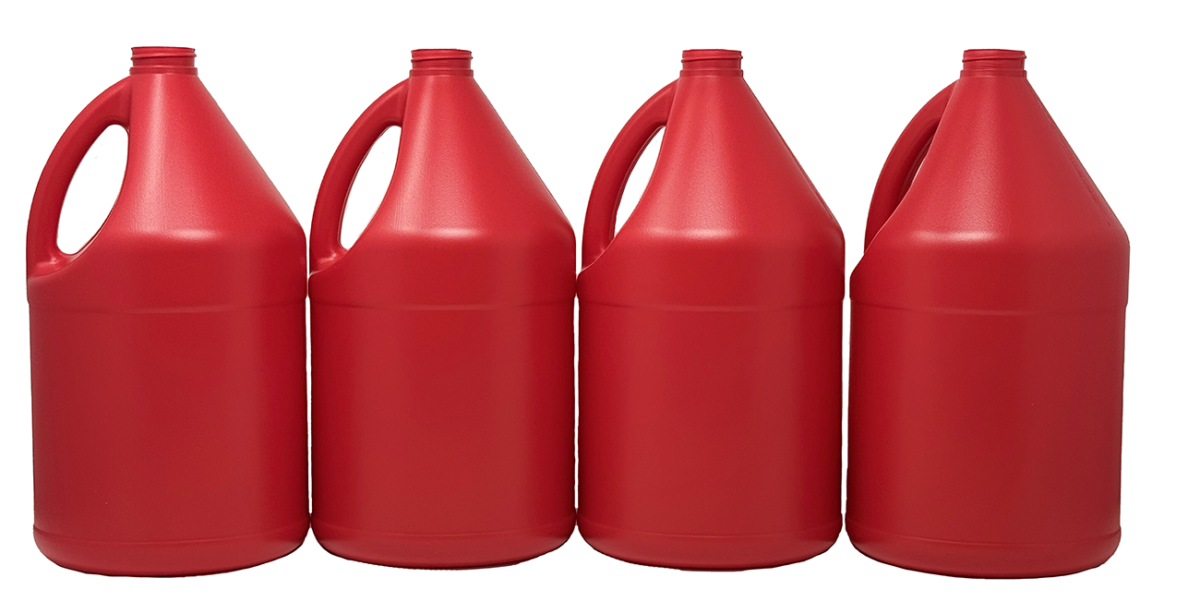
ExxonMobil Using Techmer PM’s Dispersion Technology to Reduce HDPE Colorant Costs
There can be many good reasons to switch resins for a particular application. But when requalifying a resin for a specific use, it’s important to remember to assess the situation holistically. That’s because if you focus solely on a certain aspect of the change, you may overlook opportunities to make additional improvements in your process or product.
“Consider the resin, the color, the process, even the mold design,” advises Steve Smith, rigid packaging market manager for Techmer PM LLC. “Take advantage of a resin requalification to do the best you can with the entire system.”
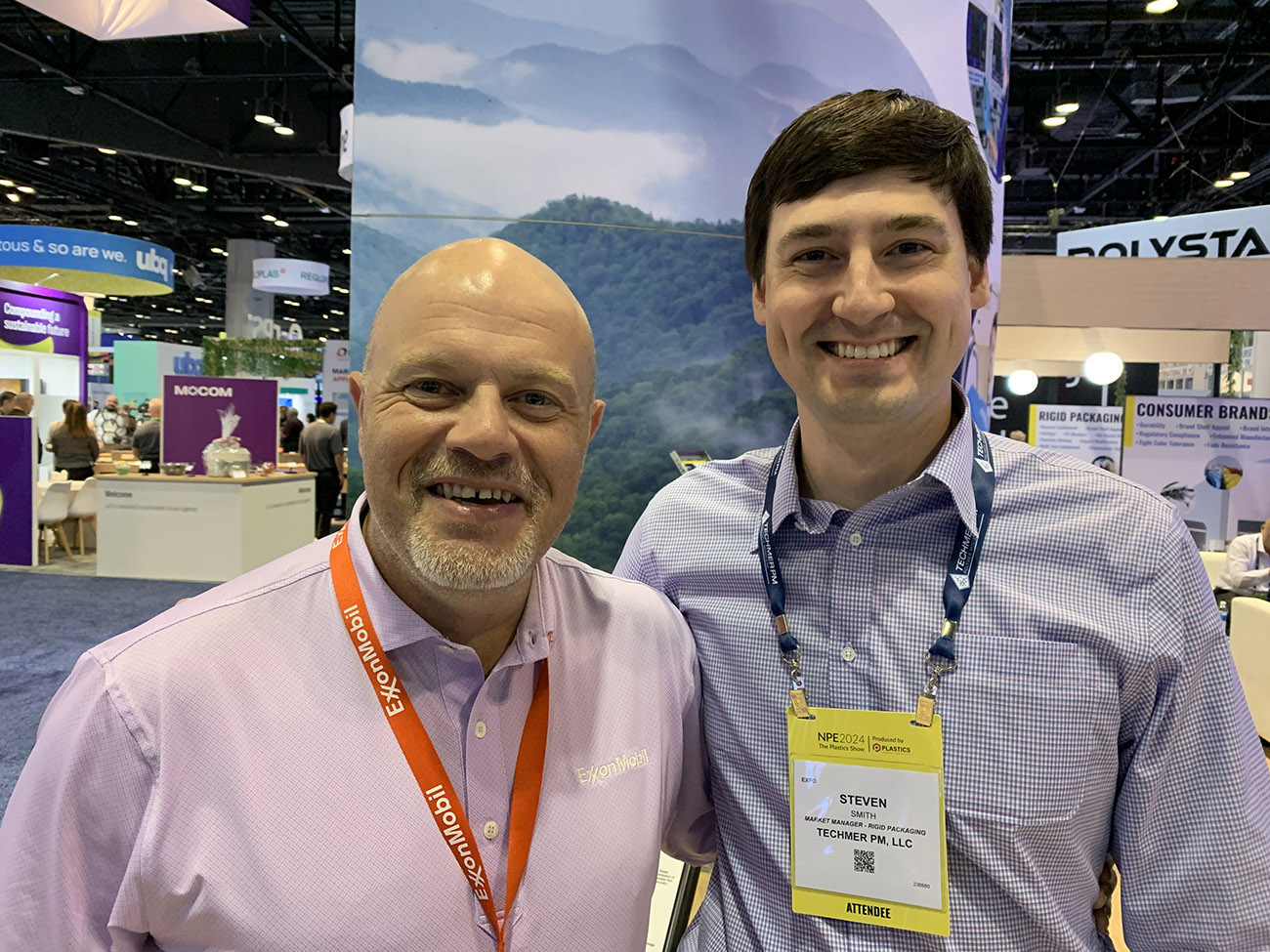
ExxonMobil’s Dr. James Stern (left) with Techmer PM’s Steve Smith at NPE 2024. Photo by Robert Grace
Improving HDPE’s Stress Crack Resistance
Techmer PM, a compounder and materials design specialist based in Clinton, Tenn., cited its ongoing efforts with ExxonMobil as a case in point. ExxonMobil’s Paxon™ SP5504 high-density polyethylene (HDPE) is well established as a unimodal blow molding resin that offers significantly improved performance when it comes to environmental stress cracking resistance (ESCR). It does so, the company said at the time of its 2021 launch, without compromising stiffness, impact, top load performance, or processability.
According to Dr. James Stern, HDPE market development manager—North America for ExxonMobil Product Solutions Co. in Spring, Texas, Paxon SP5504 fills the space between unimodal and bimodal HDPE grades in terms of performance and processability.
Between Unimodal and Bimodal
Paxon SP5504 “can be used as a drop-in solution for unimodal HDPE but with a better balance of properties,” said Stern. “Or it can replace bimodal HDPE grades in applications that have had to be over-engineered to obtain a desired balance of ESCR and stiffness.”
The resin is said to be ideal for household and industrial chemical (HIC) bottles and containers, which contain products such as bleach, wipes, and agricultural chemicals. However, ExxonMobil would like to broaden its use and extend the potential benefits of switching to that grade further.
This has prompted it to work closely with Techmer PM, said Stern, to evaluate how Paxon SP5504 works with Techmer’s proprietary TechSperse dispersion technology, which uses a pre-dispersion step to process the pigments prior to making a custom color. The purpose of the pre-dispersion step, notes Smith, is to break the pigment into smaller particles in order to get the most out of it. As the final step in making custom color, one then can mix multiple pre-dispersions to match a specific color target.
Seeing Red (in Exactly the Right Shade)
The two firms worked with a custom red color as a model system and demonstrated that TechSperse enables a reduction in the let-down ratio (LDR), or the amount of colorant needed to achieve the desired shade. This was secured while Paxon SP5504 retained its superior performance in end-use properties compared to competitive standard HDPE resins. Using less colorant with a higher-performing HDPE resin saves money. Pure and simple.
Smith notes that, for instance, with the improved ESCR performance in a Paxon SP5504 bottle, brand owners likely could reduce the bottle’s wall thickness and overall weight. That also should allow one to use less color as, in proportion to the reduction in bottle weight. Same color, same performance, lower cost.
ExxonMobil has been able to demonstrate this result in real-life tests. For the sample red hue, Smith estimates that color costs could by anywhere between 25 and 50 percent. That said, TechSperse can work with any color. Smith noted that Techmer PM continues to look for more partners with which to collaborate. Its aim is to help customers maximize the possibilities and minimize the costs related to adopting or requalifying any resin.