Rethinking the System: We Need Molecular Recycling
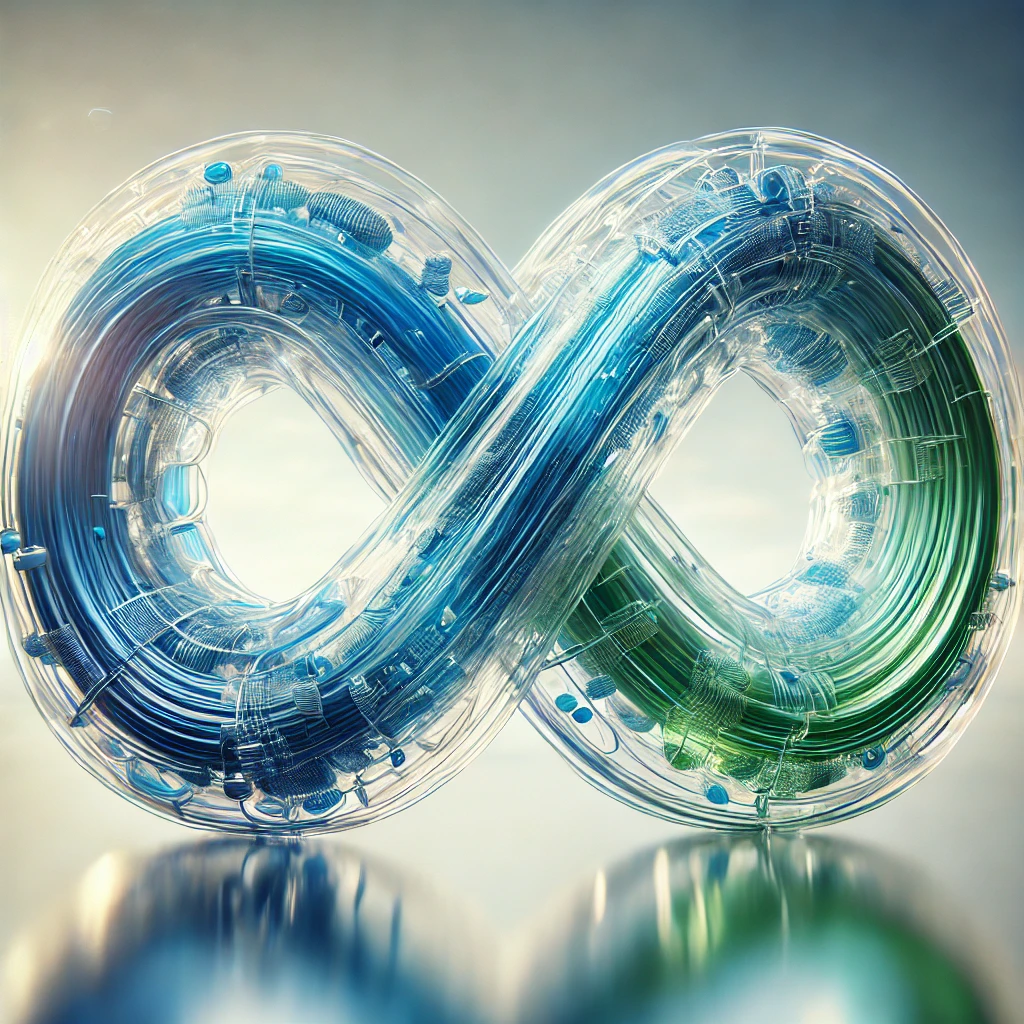
The lower recycling rates worldwide have demonstrated that effectively managing plastic waste needs multiple recycling technologies.
The plastic waste crisis primarily stems from single-use plastics, yet two-thirds of plastics serve other purposes. Nearly 100% of durable goods and clothes are in landfills without an end-of-life plan. Additionally, healthcare facilities in the US generate 3,500 tons of plastic waste daily, mainly disposed of in landfills or incinerated. Closed Loop Partners did a comprehensive study about molecular recycling technologies in the United States and Canada. They analyzed the future and viability of the recycling system as we know it.
You can also read: Can Chemical Recycling Transform Plastic Waste Management?
Current Recycling System
The current system is dominated by mechanical recycling. Nevertheless, low recycling rates in the US and the EU show that mechanical recycling has failed to recycle all types of plastics because it relies on the correct separation of the materials and the purity of the recycling stream. Moreover, mechanical recycling affects material properties, breaking and degrading material bonds. Our economy must get to the point at which materials remain at their original application or have an upgrade. However, over 50% of rPet in the US and Canada is downcycled into recycled content fibers for apparel. Those textiles currently don’t have an end-of-life solution and have a recycling rate of 1% globally.
You can also read: The Fashion Industry Needs an Alternative to Recycled PET
Recycled Content Demand
The demand for recycled plastics has created targeted interest for just a few plastic families, such as PET and HDPE. Other plastics remain economically unviable to recycle due to their multilateral nature and lack of a consolidated recollection and recycling stream, as in PS, thermosets, and black and colored plastic. Technical and financial barriers are some of the reasons that prevent the recycling rates from increasing.
Moreover, the supply of PCR with inconsistent processability and mechanical properties and the price of virgin resins are strong drivers for not including recycled content when it’s not mandatory.
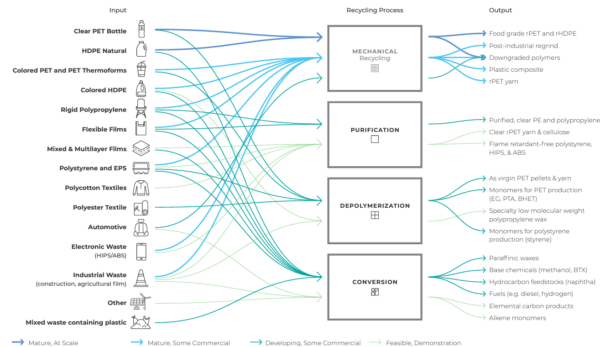
Recycling inputs and outputs: early and developing material flows by technology category. Courtesy of transitioning to a circular system for plastics assessing molecular recycling technologies in the United States and Canada.
You can also read: Post-Industrial Recycling Means Better Plastic
How Do We Effectively Address Plastic Waste?
No single sector, technology, or approach can solve the plastic waste challenge. Transitioning from a linear to a circular economy means bringing more technologies into the recycling system. A comprehensive approach involves both upstream and downstream strategies.
- Upstream solutions: These include reducing plastic via design innovation, considering end-of-life, reducing material use, incorporating alternative, renewable raw materials, and enabling modularity. They also include reuse models that extend the useful life of products and packaging and reduce our reliance on single-use materials.
- Downstream solutions: These include mechanical recycling, molecular recycling, and policies that incentivize circularity.Molecular recycling technologies can address the most difficult-to-recycle plastics and meet the growing demand for high-quality food and medical-grade recycled plastics. Even though mechanical recycling is the most developed technology, it also requires investment in materials recovery infrastructure, technologies, and companies that recapture and recycle materials after use.
You can also read: The Urgent Push for Recycling System Improvements in the US
Molecular Recycling: More Than Pyrolisis
Molecular recycling includes many technologies that purify or break down plastic into polymers, monomers, oligomers, or hydrocarbons. It encompasses “chemical recycling” methods like pyrolysis. Additionally, it uses enzymes, soundwaves, and other platforms to transform plastics. Generally, these processes fall into three categories: purification, depolymerization, and conversion.
Purification
These processes differ from other molecular recycling categories by not breaking plastic polymer bonds. Instead, purification is a physical process. These processes use solvents to remove color and additives from single-polymer or mixed plastics. Consequently, they produce virgin-like polymers. Furthermore, these processes ensure a plastic-to-plastic outcome.
Depolymerization
It can be divided into partial and complete depolymerization. The partial breaks some polymer chain bonds, producing low-molecular-weight polymers. These can be sold as standalone products. Additionally, they can be repolymerized after removing colorants and additives. In contrast, full depolymerization completely breaks down the polymer chain into monomers or oligomers. These can then be polymerized back into plastic or integrated into other supply chains in an open-loop system. Both depolymerization types require clean, plastic-only feedstock inputs.
Conversion
These technologies break bonds in the polymer chain and include “partial” and “full” sub-categories. Conversion targets polyolefin plastics such as polypropylene, polyethylene, and polystyrene (PS). Partial conversion, like pyrolysis, breaks polymer chains and involves side reactions, producing various hydrocarbon products with a wide range of molecular weights, including naphtha, paraffin waxes, petrochemical products, and fuels. In contrast, full conversion, including gasification and flash joule heating, completely breaks down the polymer to form syngas or elemental carbon products like methanol and hydrogen.
You can also read: Plastic Films: Solvent-Recycling Solutions
Companies Working in Molecular Recycling
Some companies are leading the path of molecular recycling with their technologies. Some examples are APK, PureCycle, GreenMantra, Carbios, Jeplan and Enerkem. These technologies differ in the processes used and the extent to which they break the bonds during the process.
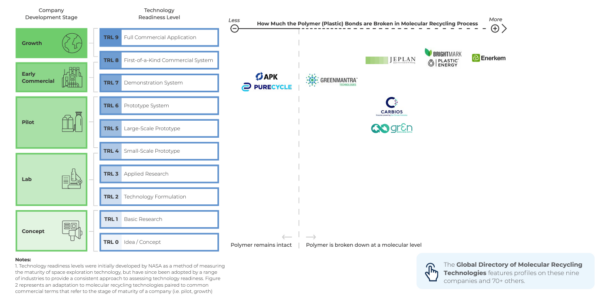
Breakdown of companies by technology in the molecular recycling sector. Courtesy of Transitioning to a Circular System for Plastics Assessing Molecular Recycling Technologies in the United States and Canada.
You can also read: Molecular Recycling for Hard-to-Recycle Plastics
Future of recycling
Molecular recycling outputs may not be economically viable for many sectors. For instance, plastic buckets and park benches manufacturers don’t need virgin-quality recycled polypropylene (PPP). Lower-grade plastics suffice for their needs. Therefore, the diversity of end markets for recycled plastics and their quality specifications show that mechanical and molecular recycling are complementary. Working together, these systems can recover a broader range of plastic waste. They can also produce diverse plastics and products for the most suitable markets.
Economic Impact of Molecular Recycling
Integrating new technologies into the downstream plastics recycling systems in the U.S. and Canada could have a great economic impact. The amount of plastic packaging recycled could be doubled, and up to $970 million (USD) annually could be generated.
Moreover, the potential for a symbiotic relationship between mechanical and molecular recycling is evident and can mark the difference between a successful business model or not. Material recovery facilities currently supply plastic feedstock to many molecular recycling companies in the U.S. and Canada. Collaboration between mechanical recyclers and molecular recycling operators can create new pathways to increase plastic recycling. This partnership can develop more circular and collaborative plastic supply chains involving recyclers, the chemical and petrochemical industry, plastic packaging producers, industrial users, and the retail and consumer goods sectors.
To read the complete study ‘Assessing Molecular Recycling Technologies in the United States and Canada’ click HERE.
Your choices of examples of companies in advanced recycling is lacking. You have left off Alterra and Nexus, the only volume pyrolysis companies, Eastman who is the largest advanced recycler operating today and Exxon. The whole article seems wrote and stale.
Hello Robert! Thank you very much for your comment and for reading the article. As you noted, we dedicated a section of the article to explain that pyrolysis is just one technology within the molecular recycling universe. The article specifically focuses on technologies that do not break down polymer molecules or do so on a smaller scale than pyrolysis. That’s why we did not cover any of the companies you mentioned. However, we appreciate the insightful information you provided about the pyrolysis market.