Polyurethane: Sustainable & Digital Check
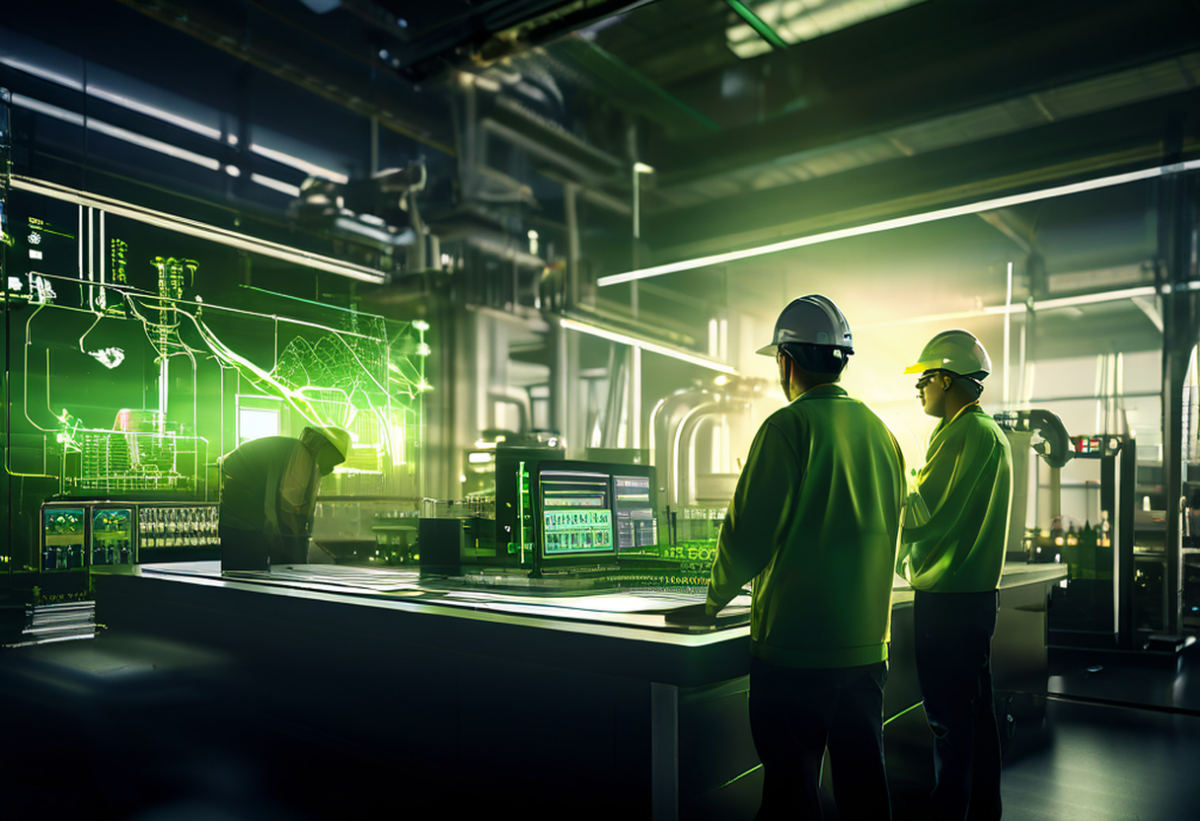
Digital technologies offer new opportunities for Polyurethane, not only from an environmental perspective but also in terms of improved properties and processing.
Polyurethane represents a market of over 20 million metric tons. However, sustainability issues are critical in its production, even though bio-based polyols are already available.
Polyurethane digitalization includes many predictive tools, such as digital twins, reverse engineering, and big data, allowing a shortened market time through an efficient development phase.
Let´s review these two major drivers and challenges from the perspective of Plastics Engineering.
You can also read: Silent Polyurethane Tires for Electric Vehicles, Exploring Supercritical Foaming Technology
Sustainability from Raw Material
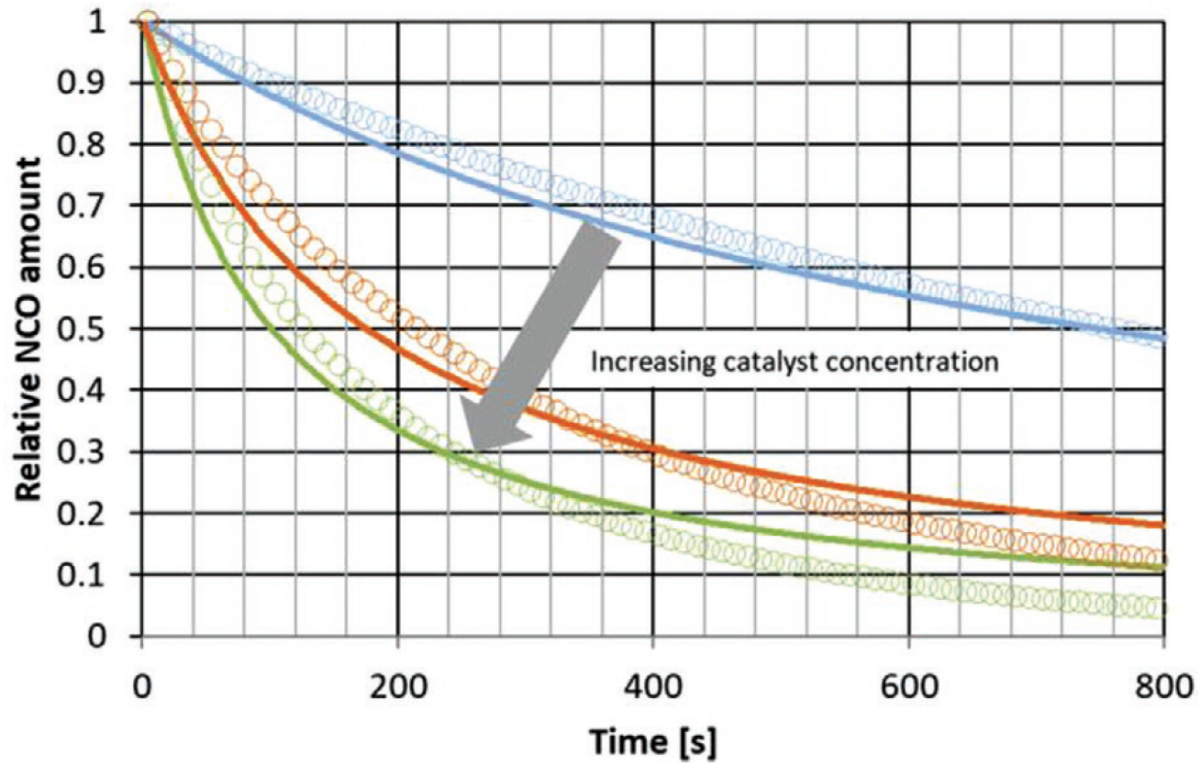
The consumption of NCO end groups in a polyurethane reaction process with varying amounts of a specific catalyst at different temperatures improves the fit of simulations to experimental results. Courtesy of Macromolecular, Physics & Physics Journal
By changing the type and functionality of the polyol and isocyanate, it is possible to tailor the forms and properties of polyurethane. The choice of polyol significantly influences the properties through its interaction with TDI and MDI based on its weight and chemical structure.
Since polyurethane materials are primarily produced from non-renewable resources, there is a concerted effort to develop innovative catalytic processes, low solvent process steps, adiabatic process management, closed-loop raw material cycles, and extensive production facilities with improved efficiency. In the past decade, intensive research has developed novel and sustainable polyols and isocyanates from renewable sources such as vegetable oils and biomass (including sugars, starches, and lignocellulosic biomass).
Notably, bio-based monomers like 1,3-propanediol and 1,4-butanediol, derived from sugar fermentation, are now produced on a large scale and used for creating bio-based polyether polyols, such as BASF’s PolyTHF 1000 and DuPont’s Cerenol.
Digitalization and Interconnection of the Whole Value Chain
Digitalization will play a key role in the current and future development of polyurethane systems. The collaboration of multiple disciplines enables the development of structure-property relationships and process models based on statistical and scientific methods.
Developing a digital twin requires validation with real data before becoming a fully functional virtual tool. While not all models are highly accurate, they allow companies to conduct virtual experiments to correlate various parameters, establish trends, and significantly reduce the number of real experiments needed, thereby speeding up decision-making and time-to-market.
In polyurethane value chain modeling, the emphasis on processing highlights the link between recipes, manufacturing conditions, and the morphology of the foams. For example, the consumption of NCO end groups in a polyurethane reaction process with varying amounts of a specific catalyst at different temperatures improves the fit of simulations to experimental results.
BASF’s Creation Center uses its simulation software, Ultra-Sim, to achieve robust process settings through optimization and venting concepts based on local material properties. However, the lack of real data still weakens these models’ ability to replicate shop floor reality, presenting a significant industry bottleneck.
These are just some of the recent trends in the polyurethane industry. In the next article, we will continue to explore recycling and energy aspects.
To read more: Current and Future Trends in Polyurethanes: An Industrial Perspective.