Mono-Material PET Bottle Caps: Enhancing Recycling Efforts
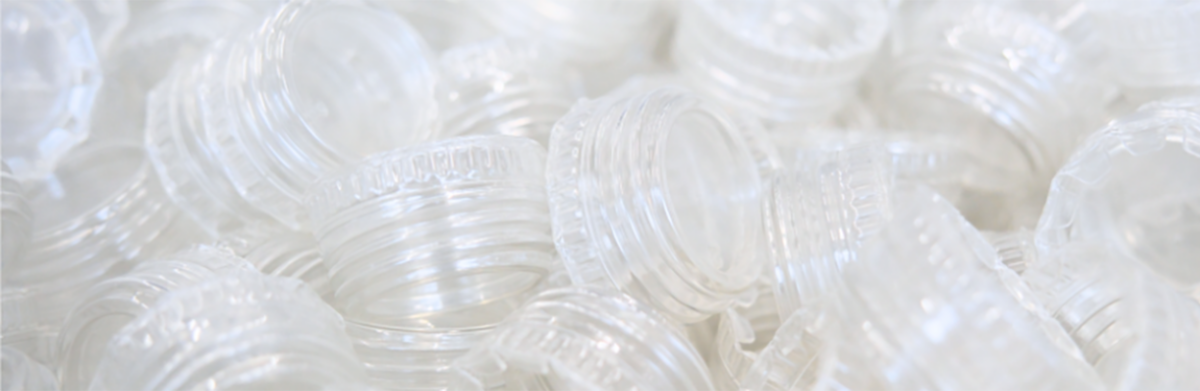
The mono-material approach could help to boost PET recycling.
A Swiss packaging machinery maker and a California “carbon-negative” materials company have collaborated to develop what they are calling “the world’s first PET cap and closure manufacturing system.” The aim is to further enable recycling by taking a mono-material approach. This involves pairing PET caps with PET bottles, instead of making firms separate caps made of different resins to avoid contaminating the recycling stream.
PackSys Global AG of Ruti, Switzerland, and Origin Materials of West Sacramento, Calif., were promoting their new technology at NPE 2024. Ueli Kobel, director of PackSys Global’s Slitting Division, said in an interview at the firm’s booth that they began the project two years ago and did most of the design work on the closure in the U.S. He noted that this is most suitable for simple screw caps and not likely for more complex molded caps such as those with flip-tops for sports drinks.
PET Caps Can Enhance Recyclability
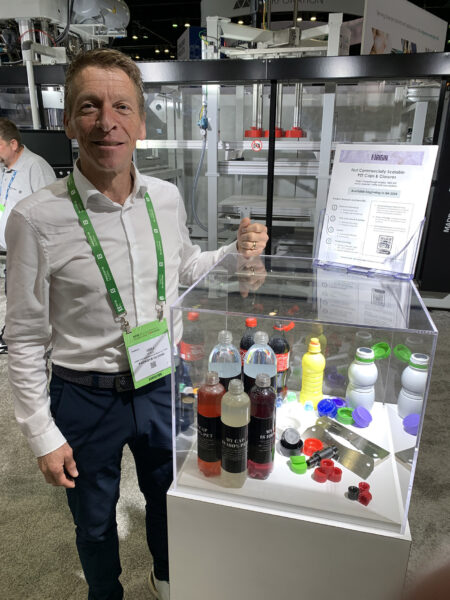
Ueli Kobel, director of PackSys Global’s Slitting Division, at NPE showcased the PET bottle caps that his firm developed jointly with Origin Materials. Photo by Robert Grace
“PET closures can be a game changer for closure recycling,” Kobel said in a statement. “Most beverage closures are today made from HDPE and, while closure recycling rates are increasing, especially in Europe where closure tethering will be mandatory starting July 2024, a beverage container remains a two-material solution. HDPE suffers from degradation when reused multiple times. Changing a closure to the same grade of PET as in the container avoids the need to separate the two materials and also solves the degradation topic at the same time.”
Origin Co-CEO and co-founder John Bissell said Origin’s high-throughput production system is the first to be able to make PET caps and closures at commercial scale. “We expect it will be the first of many such production lines for making not just beverage packaging better and fully recyclable, but containers of nearly every kind.”
Perfecting the Slit and Fold Process for PET Caps
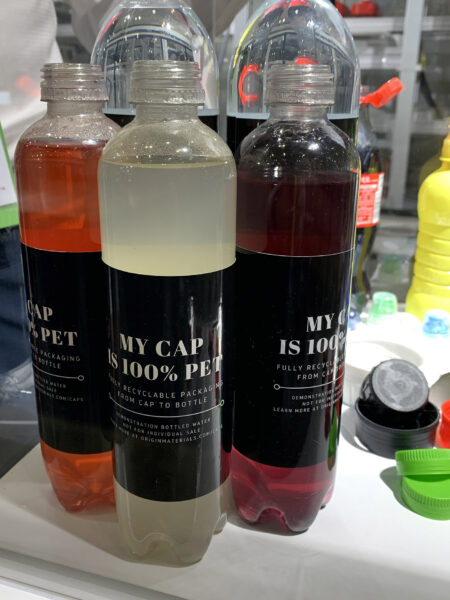
On its NPE stand, PackSys touted “fully recyclable packaging, from cap to bottle.” Photo by Robert Grace
Speaking to the latest project with PackSys, Origin senior research engineer Rachel Hess said: “We’ve been working on improving the process for a slit and fold on the PET caps. We have increased the speed of the process, reduced the number of overall steps, and increased the scale of our trials. Overall, we’ve crossed the 100,000 cap mark and are excited about the results.” (See a video of the process here.)
The partners, who first announced this project last August, said they can make the caps with virgin PET, recycled PET (rPET), or bio-based PET, and noted that this development “expands the ability to use rPET” in closure applications.
On May 14 Origin announced its 2024 first-quarter financial results. Despite reporting a net loss of $13.9 million for the three months to March 31, Co-CEO Rich Riley said: “We have seen strong progress on our pathway to profitability, led by our groundbreaking PET caps and closures business.” The firm reported $6.8 million in total revenues for the quarter.
Origin Ordering More Commercial Production Lines
Riley also said: “Today we are announcing that we have accelerated the procurement of multiple additional high-throughput commercial production lines to complement the first line, which we already ordered. We aim to bring our first manufacturing system online during the fourth quarter of 2024.” At full capacity, he said they expect their initial systems to generate between $45 million and $65 million in annual revenue.
“The caps and closures opportunity,” he continued, “is massive –– an over $65 billion market –– with currently engaged prospective customers alone consuming tens of billions of caps per year. We look forward to rapidly standing up additional lines addressing multiple product types, including tethered beverage caps and caps for non-beverage home goods applications.”