Extrusion Troubleshooting – Key Drivers (Part 1 of 3)
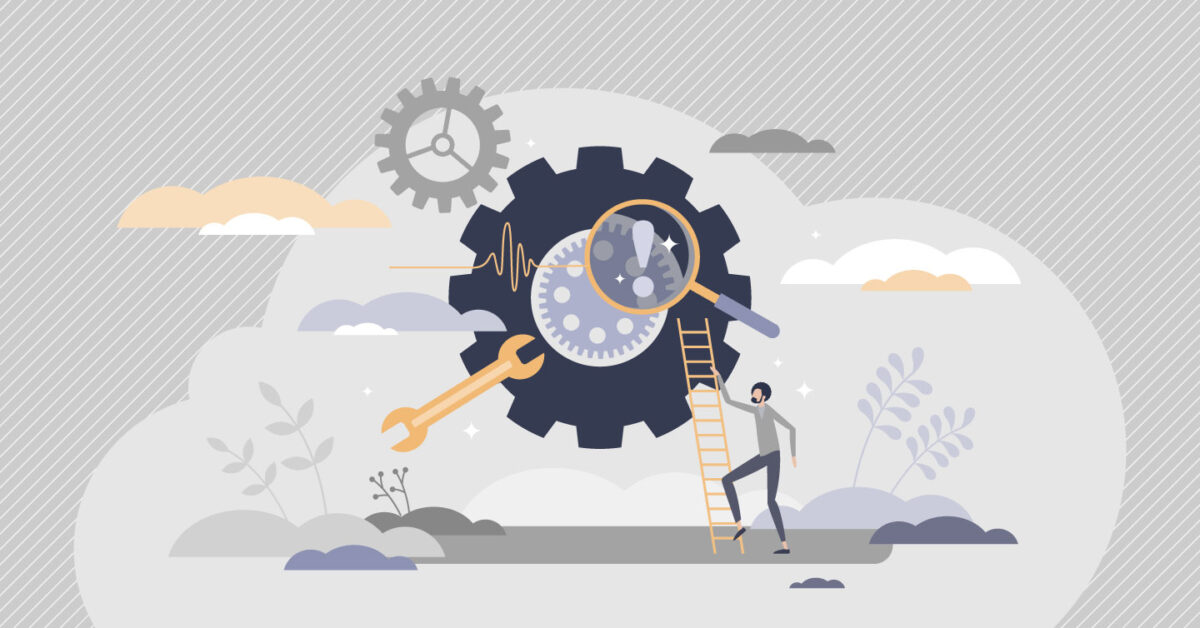
Extrusion Troubleshooting becomes crucial to ensure high productivity, effectiveness, quality, and profit. All in a frame of the promising outlook of 4.7% market growth by 2032.
Extrusion troubleshooting again? why? The plastics extrusion market is poised for substantial growth over the next decade. Forecasts indicate a 4.7% increase in the machines segment from 2022 to 2032, with its value projected to reach a staggering U$10.7 billion by 2032. This growth is primarily driven by key industries such as automotive, packaging, construction, and consumer goods.
You can also read: Precision Production
Given this promising outlook, it becomes crucial to focus on potential troubleshooting drivers to ensure high productivity, competitiveness, quality, and profit. We’ve compiled a comprehensive guide into three articles to address this need. Here are the first four key drivers:
Elevated Engine Amperage
May stem from various factors including low melt temperature, inappropriate resin selection, grid blockages, motor capacity issues, or system contamination. Troubleshooting facts involve initially raising temperatures and inspecting heater electrical outputs, along with replacing perforated plate grids. Regarding material choice, a low molecular weight polymer could be help. Engine performance assessment is crucial; maintenance or speed adjustment may be necessary. Additionally, inspecting screws for contamination is advisable to determine if the increased current is solely attributable to the need for thorough cleaning.
Discontinuous Material Outlet
Potential causes of this issue include hopper clogs, bridging, or blockages, as well as potential cooling jacket malfunctions. Resolving this problem includes reducing temperatures in the feeding zone, employing a cram feeder, or extruding material into pellets separately. Additionally, other recommended troubleshooting approach are first, assessing the material degradation or cross-linking in the screen pack and second, ensuring that the cooling jacket operates efficiently without excessively solidifying zones.
Uneven Flow (Surging)
Inadequate temperatures, contamination, or melt transport issues can lead to uneven flow. Addressing this concern involves several actions: Adjusting heating zone temperatures, considering removal of the internal mixer if applicable, lowering feed zone temperatures to prevent bridging, cleaning the screen pack, checking for hopper obstructions, inspecting the screw for contaminants, and increasing product traction pressure. It may also be necessary to assess if the polymer’s viscosity is too low, necessitating pelletization or the use of a cram or starve feeder. Lastly, modifying the screw design could provide a solution.
No Material Outflow
This issue involves elements such as the hopper, screw, screen pack, and/or extrusion die. To address this significant challenge, one or more of the following actions should be taken: Open the hopper distribution valve, use a soft bar to dislodge bridging, apply vibration pads, and/or utilize an mixer agitator in the hopper feeding zone. Other activities to tackle this issue relate to the screw, such as: changing the drive motor terminals, conducting repairs, cleaning, applying a low-friction coating, or having prefabricated spare parts ready for assembly. Additionally, clearing the feeding opening blockage, using finer mesh screens, or replacing them with new ones, and/or increasing die temperature could also be effective measures.
To read more: Plastic Extrusion Machine Market Size, Demand, Trends – 2032