Composite 3D Printing in Aerospace and Robotics
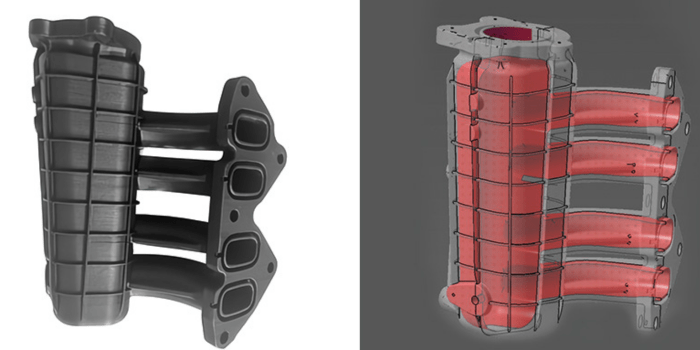
While 3D printing with polymers and metals has dominated discussions, composites have quietly emerged as a significant player in additive manufacturing (AM).
Combining the strength of metals with the lightness of polymers, composite materials are reshaping the landscape of 3D printing, particularly in fused filament fabrication (FFF) technology.
The global composite 3D printing market is forecasted to soar to $490.47 million by 2030, reflecting a remarkable trajectory from its $198.31 million valuation in 2023. This surge underscores the increasing demand for composite materials in AM. Notably, the Institute of Industrial New Materials in Dezhou, China, has recognized the pivotal role of composites in 3D printing.
3D printing offers unparalleled advantages over traditional manufacturing processes, especially in the realm of complex geometries and cost-effective design optimization. This versatility has spurred innovative applications across various sectors, including aerospace, maritime, and advanced manufacturing.
Case Study: Intake Manifolds for Aircraft Engines
The Institute of Industrial New Materials tackled the challenge of developing intake manifolds for aircraft engines using FFF 3D printing. These critical components demand intricate designs and precise performance characteristics, making traditional manufacturing methods cumbersome and expensive. By leveraging FFF technology and advanced materials like PEEK-CF, the institute achieved significant weight reduction and superior mechanical strength, surpassing conventional injection-molded products.
The adoption of composite 3D printing yielded substantial cost savings, reducing production expenses by 90% and shortening lead times from 45 days to just 4–7 days. This transformative impact underscores the economic viability and efficiency of additive manufacturing in producing complex composite parts.
Integrating with Existing Processes
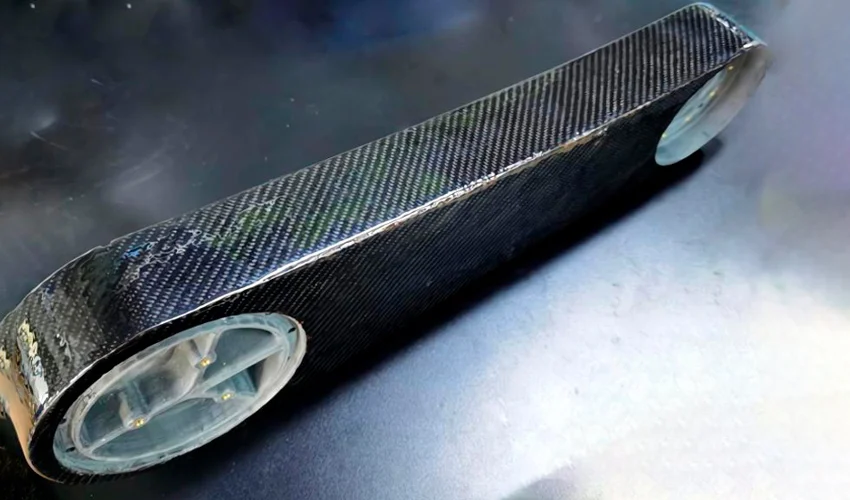
The robotic arm component, printed using composite 3D printing. Courtesy of INTAMSYS
Moreover, composite 3D printing can seamlessly integrate with existing manufacturing techniques, offering a hybrid approach to composite part production. Collaborative efforts with Chinese universities have demonstrated the feasibility of combining 3D printing with filament winding and layup methods, unlocking new possibilities in part design and fabrication.
As the Institute of Industrial New Materials has exemplified, composite printing holds immense promise for the plastics engineering industry. By augmenting or replacing traditional processes, it enables enhanced efficiency, cost-effectiveness, and performance in composite part manufacturing. Embracing this technology paves the way for a sustainable and innovative future in plastics engineering.