Plastic Films: Solvent-Recycling Solutions
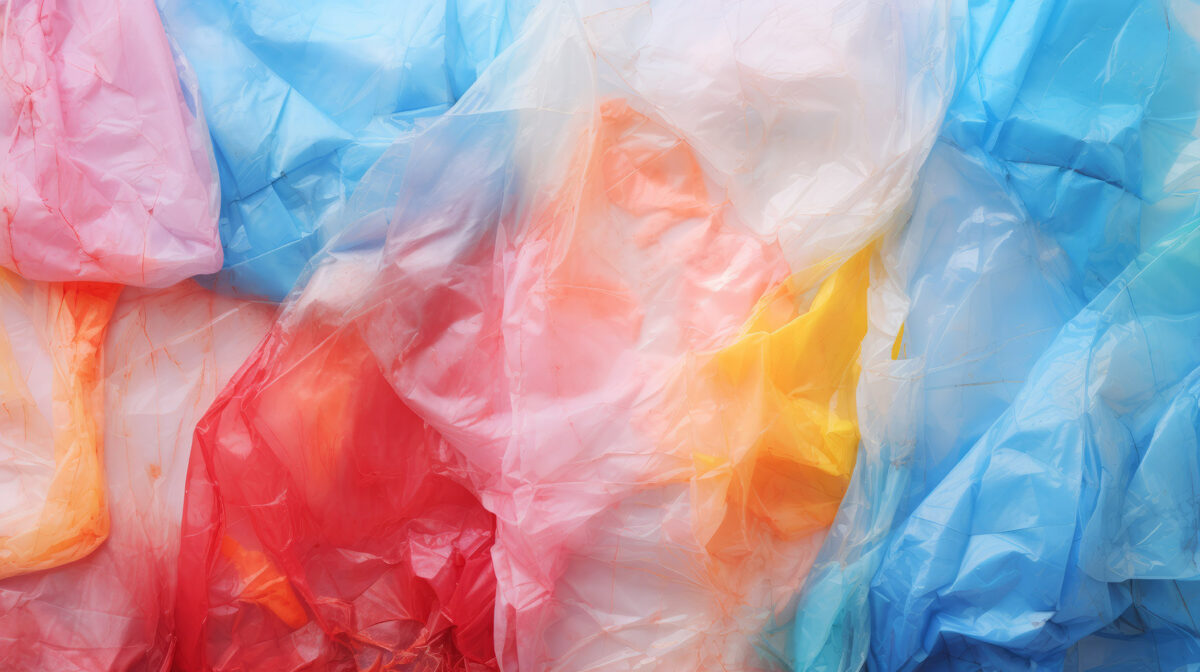
Recycling plastic films through Solvent-Targeted Recovery and Precipitation (STRAP) is crucial for environmental sustainability since packaging commonly uses these materials. While experts are testing pioneering methods, scaling these techniques remains a challenge.
Recycling Multi-Layer Films
The STRAP technology emerges as a promising solution for recycling complex multilayer plastic films. It demands a thorough analysis of scalability, cost-effectiveness, and environmental impacts. Layering various plastics creates stronger, impermeable materials with unique features that preserve food quality and extend its lifespan. This multilayer packaging approach reduces the need for materials, cutting down on greenhouse gas emissions. It also minimizes food waste by enabling more efficient consumption through smaller, portioned packaging. Single-layer plastics cannot match the benefits of these multilayer films. However, the chemical incompatibility of the different layers poses challenges to easy mechanical recycling of multilayer plastics. These films often end up in landfills or are incinerated, contributing to environmental pollution and greenhouse gas emissions. Recognizing the urgent need for innovative recycling solutions, researchers have developed STRAP technology as a novel method to address this challenge.
You can also read: Flexible and Recyclable: Monomaterial Packaging Meets Sustainability Needs
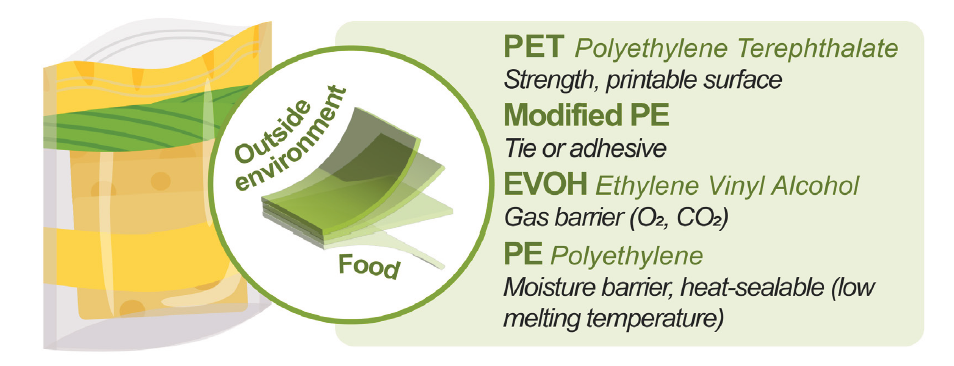
Layering various plastics creates stronger, impermeable materials with unique features that preserve food quality and extend its lifespan. Courtesy of CUWP.
STRAP: A Solvent Approach
STRAP processes multilayer films with solvents, separating them into their plastic resins for recovery and reuse. This method recycles plastics previously deemed non-recyclable and upcycles them into more valuable products. Its ability to recover pure plastic resins from mixed waste, including disposable face masks and other contaminants, is particularly significant.
Scalability is the Key
STRAP’s scalability is appealing. Initial tests show its capability to produce recycled resins on a commercial scale. By creating a process development unit for large-scale resin production, STRAP moves closer to commercial viability. Its environmental benefits, like lower greenhouse gas emissions compared to virgin polymers, highlight its sustainability potential.
Economically, STRAP produces high-quality resins at competitive costs, based on process models and experimental data. This cost-effectiveness, coupled with environmental advantages, makes STRAP a sustainable recycling alternative.
The launch of the first commercial STRAP plant in Wisconsin, a key player in the flexible packaging and plastics industry, is a major step toward sustainable plastic recycling. Supported by the local industry and academic institutions, this project aims to reduce plastic waste and promote circular economy principles.
STRAP technology’s introduction marks a major advancement in recycling multilayer plastic films. With its scalability, economic viability, and environmental benefits, STRAP is set to transform the plastics recycling industry and push us toward a more sustainable future.