Next-Gen Smart Skin: Force, Humidity, and Temperature Sensing Properties
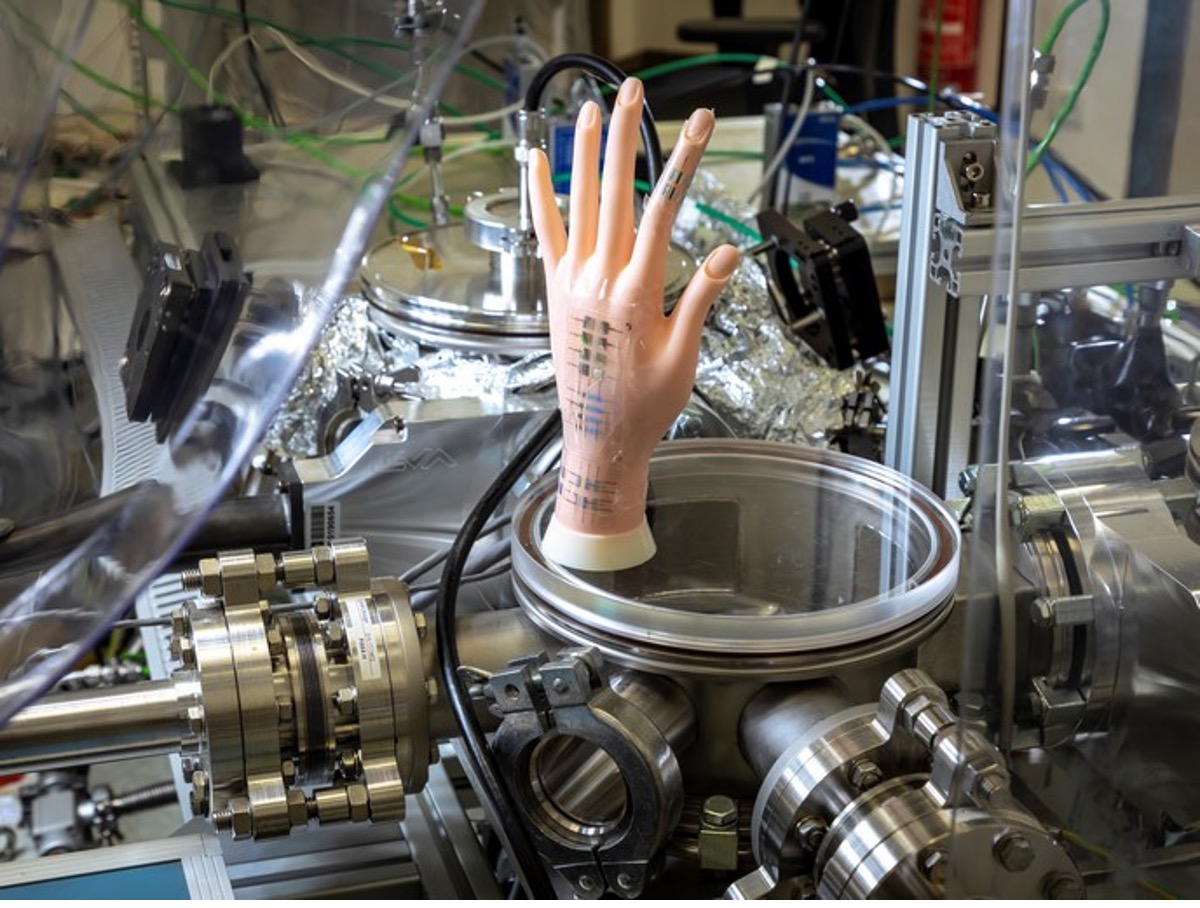
EU-supported SmartCore project creates nanorods with a core-shell structure comprised of a multi-stimuli-responsive smart polymer and a piezoelectric ZnO shell.
An array of these stimuli-responsive nanorods on a surface constitutes smart skin. These combine force, humidity, and temperature sensing (F-H-T) with high spatial resolution.
You can also read: Cast21’s Innovative Resin Casts for Improved Healing
Skin is the largest organ of the human body. It has a specialized sensory system that identifies multi-environmental stimuli and transmits this information to the brain by electrical signals. The properties and functions of natural skin pose a substantial challenge for e-skin. It requires biocompatibility, mechanical properties, and sensory perception. Researchers need suitable fabrication techniques to control the layer’s thickness and dimensions at the micro/nanoscale.
The Broad-Ranging Potential of Artificial Skin
Artificial skin has three potential fields of application.
- Aid burn victims.
- Advanced smarter humanoid robots.
- Coat prostheses.
Smart Core-Shell Nanostructures
An array of vertical core-shell nanorods pixels make up the flexible e-skin. They consist of a Poly-N-vinylcaprolactam-co-di (ethylene glycol) divinyl ether (p(NVCL-co-DEGDVE)) hydrogel core and a zinc oxide (ZnO) piezoelectric shell. Each vertical nanorod measures 500 nm laterally. It means that each pixel of the skin has thousands of sensing nanorods.
The smart polymer p(NVCL) is biocompatible and has hydrophilic functional groups. On the other hand, the ZnO piezoelectric shell is relatively biosafe, biocompatible, and semiconductive.
The hydrogel core swells while detecting changes in temperature and humidity in the environment. This swelling induces mechanical stress in the ZnO shell, which generates a measurable current charge. Furthermore, in a lateral resolution of 0.25, the ZnO can detect directly applied force. The latter is smaller than the resolution of the human skin, which is of 1 .
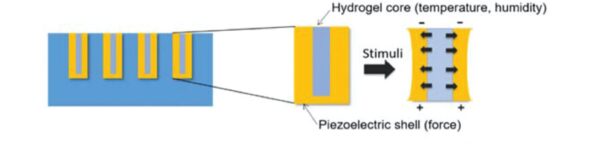
Cross-sectional view of the core-shell nanorod sensing concept. Courtesy of Smart Core-Shell Nanostructures for Force, Humidity, and Temperature Multi-Stimuli Responsiveness.
F-H-T have unique sensitivities. In the case of the force, its sensitivity is . The scientists conducted measurements for humidity and temperature sensitivities in an environmental chamber. Below the LCST of the hydrogel () and with a relative humidity of , the maximum sensitivity to relative humidity is . Moreover, above the hydrogel LCST and at saturated relative humidity, sensitivity is SH4 = 0.1 nC %−1. The maximum sensitivity to temperature is ST = −0.14 at 96% RH in a temperature range between 30 and 50°C.
Dry Vapor-based Techniques For Smart Skin Fabrication
The researchers fabricate core-shell structures by vapor deposition in vacuum chambers. The figure below shows the complete process.
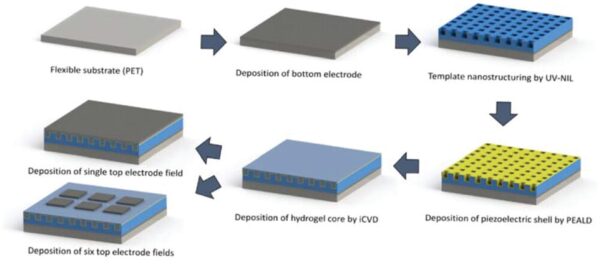
Smart skin fabrication. Courtesy of Smart Core-Shell Nanostructures for Force, Humidity, and Temperature Multi-Stimuli Responsiveness.
Firstly, e-beam evaporation deposits BE over a PET substrate. Then, scientists apply a PUA template layer by UV-NIL. Continuously, PEALD deposits ZnO shell. Next, iCVD deposits hydrogel core and finally, e-beam evaporation deposits two different TE designs.
Overall, smart skin with multi-stimuli is a significant advancement for this new field. In fact, most of the knowledge gained before this project focused on sensors for a single physical stimulus. Therefore, SmartCore researchers demonstrated the development viability of electronic skin for biomedical applications. Finally, The connection between e-skin and the human brain should be the subsequent research.