Direct Compounding Injection Molding: Cost-Efficient Expertise
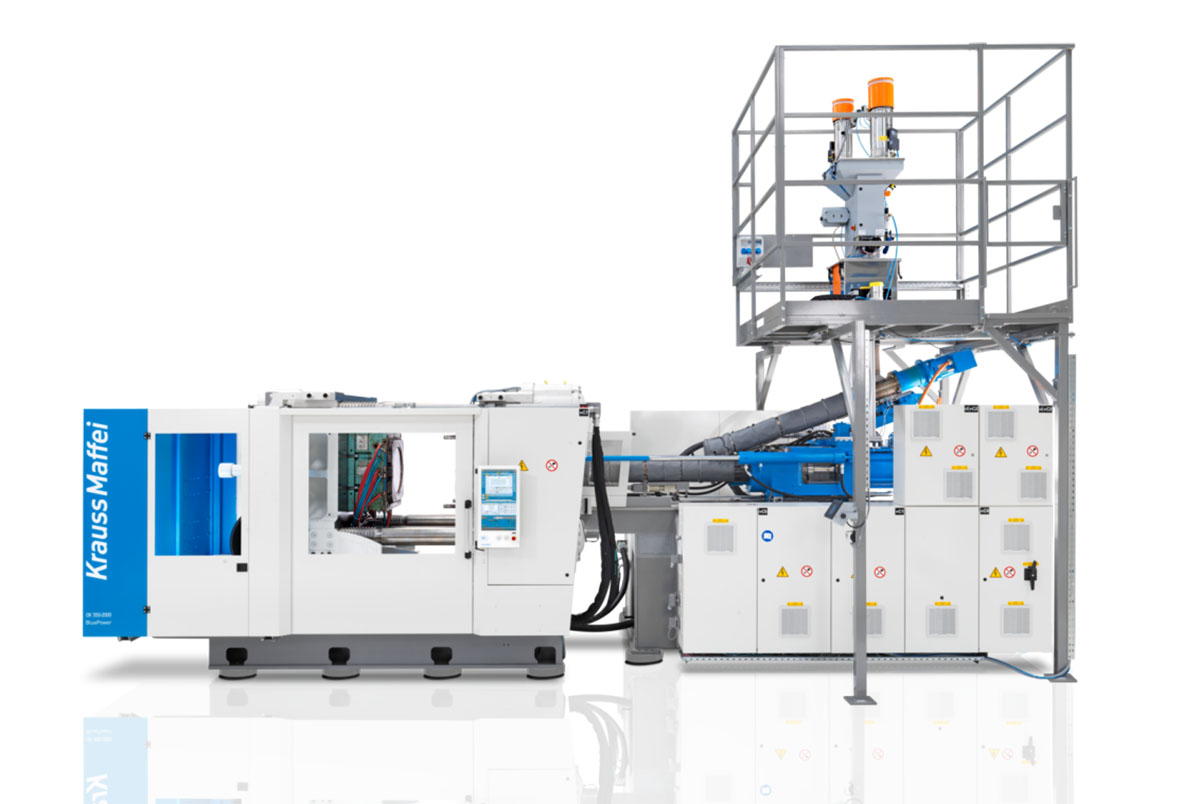
Tailored compounding for serial production and directly pelletized to the injection molding machine.
Shortened supply chain (10 to 3 steps) from compounding to injection, achieving up to €1.0/kg in energy and cost savings. It accomplishes high requirements with tailored compound formulation in-house.
You can also read: No Pelletizing Needed for Injection Molding
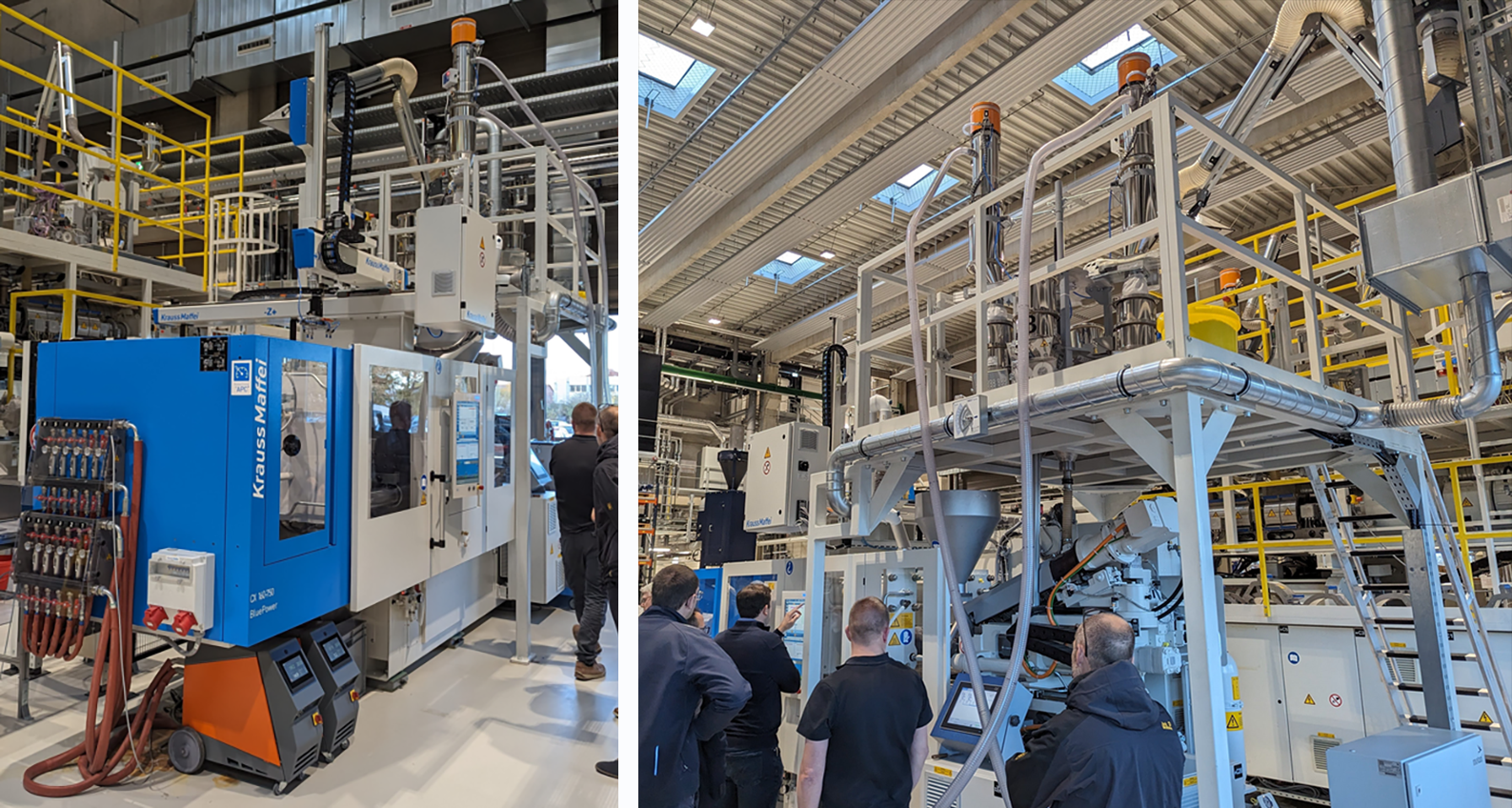
Left: IM Machine + DCIM, front view. during the IKK Event in Hannover, Germany. Right: . IM Machine + DCIM, rear view. during the IKK Event in Hannover, Germany. Courtesy of Andres Urbina
The practice of prefabricating compounds has been prevalent since the early stages of industrial plastics production. However, on the surface, it appears to be complex, costly, and environmentally detrimental. Over the years, alternative methods have been explored, with a particular emphasis on direct compounding molding (DCIM)—specifically, the manufacturing of plastic blends directly within the injection molding machine, in one heat, reducing CO2 impact and costs for storage, transportation, and above all costs for special compound formulations.
Requirements
Almost any injection molding machine is suitable for the DCIM technology, the single-screw extruder should be mounted over the feed zone of the common injection unit, which in turn has up to 8 feeders that feed the desired ratio to the extruder, to do this, they cooperate with the company Motan, guarantying accuracy, and repeatability.
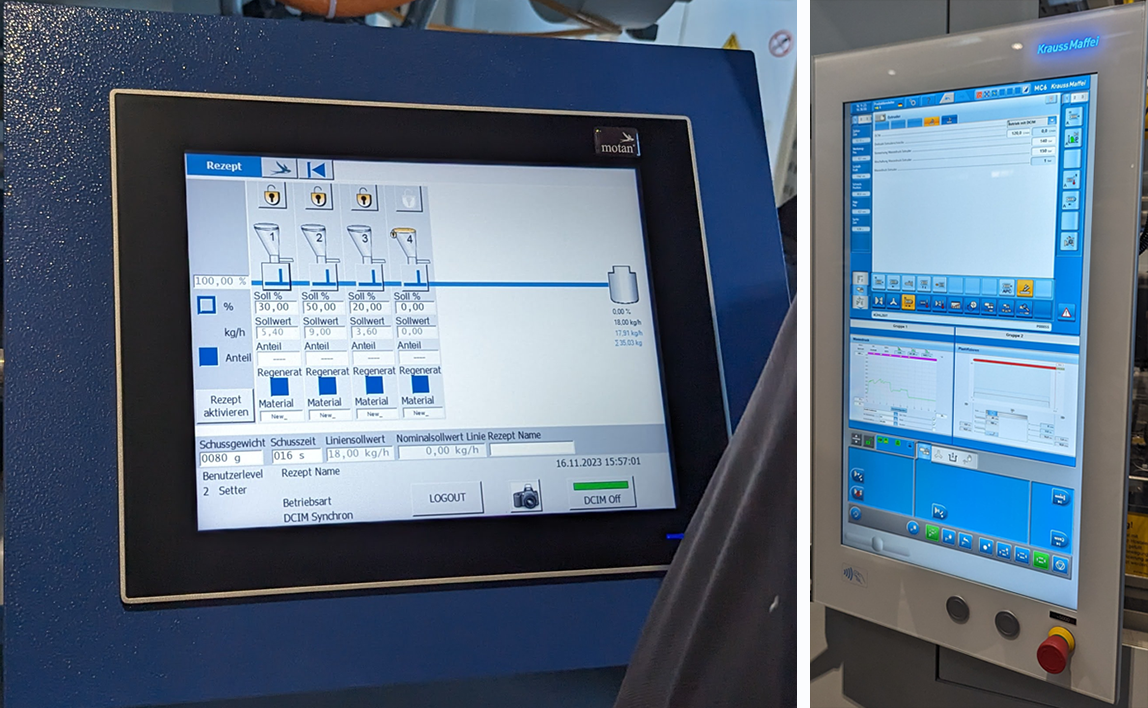
Left: Motan screen DCIM feeders, right: MC6 interface for the extruder in the machine control. Courtesy of Andres Urbina
The machine and the Direct Compounding system work in a discontinuous operation. This means that the extruder stops automatically, when the injection molding machine reaches the shot volume for the next cycle. The machine range covers until this moment machines from 160 to 1100 US Ton and shot weights between 50 and 2000 grams, so for bigger parts it should wait until the NPE 2024 when Krauss Maffei will present to the world, out of Germany, this key technology for an efficient and environmental future.
What are the benefits?
Highlighted features of the technology encompass the processing of higher viscosity recyclates, granting control over formulation for optimized material selection and achieving material cost savings ranging from €0.30/kg to €1.00/kg. The integrated design incorporates an outgassing zone, eliminating the need for a separate drying process.
It demonstrates efficient handling of poorly free-flowing materials, and excellent melting, and homogenization capabilities. Moreover, the system allows for a straightforward process configuration and monitoring, facilitated by integrating extrusion functions within the MC6 control system. This innovative approach streamlines operations and contributes to reduced energy consumption and a diminished CO2 footprint, particularly in heat-intensive production environments.
To read more: Our processes – KraussMaffei