AI Mastery: Scaling from Research to Serial Application
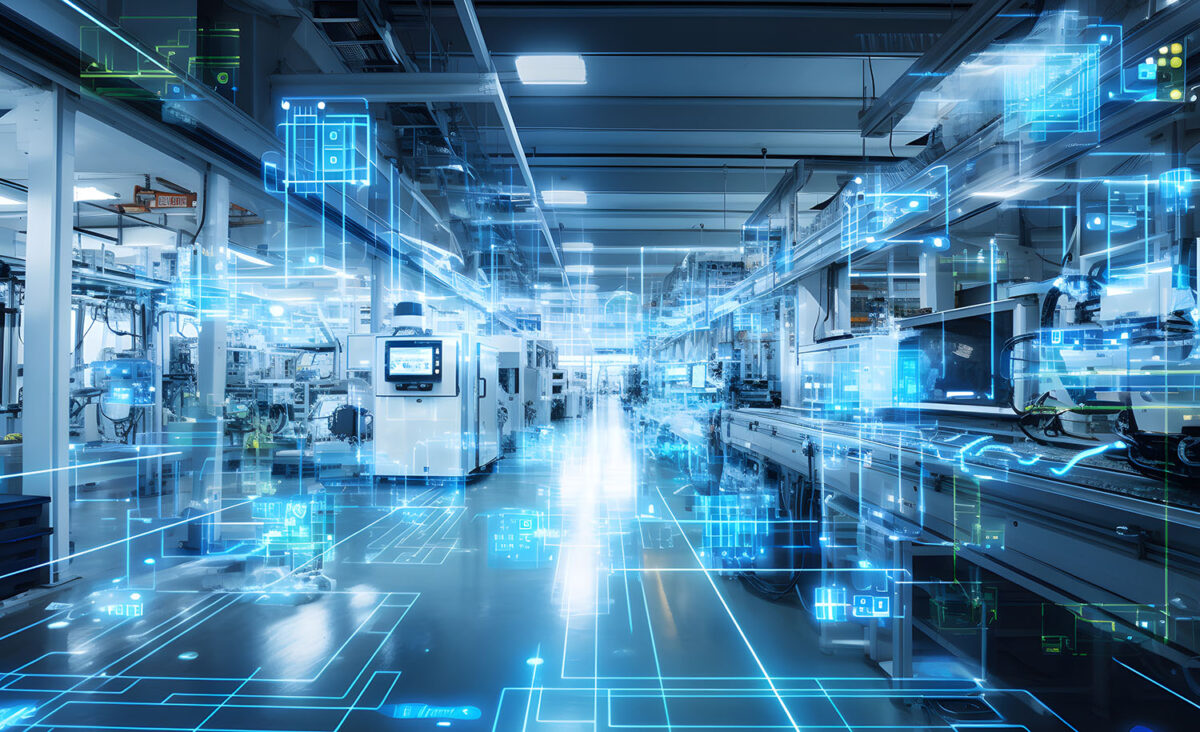
How Artificial Intelligence (AI) can succeed 6% reduction in energy consumption, a 9% decrease in rejects, and a 10% enhancement in systems efficiency.
This approach significantly accelerates the timeline from project planning to AI deployment, condensing it from months to a matter of weeks.
You can also read: AI for Enhanced Materials Development and Manufacturing, AI-Based Sensor Improves Productivity in Composites Manufacturing, Robotics and Automation to reap benefits from AI, Scientists Using AI to Accelerate Materials Discovery
How is the breakthrough?
Leveraging generative AI and foundation models, manufacturing initiatives in two German plants from Bosch utilize synthetic images to expedite AI solution development. This approach significantly accelerates the timeline from project planning to AI deployment, condensing it from months to a matter of weeks. Research to production achieved 6% energy reduction, 9% fewer rejects, and 10% system efficiency improvement.
Expanding synthetic data services to all sites follows successful pilots. Chairman Stefan Hartung, from Bosch, underscores AI adoption benefits, citing substantial cost savings and heightened productivity. Savings range from hundreds of thousands to low millions annually, varying with plant size and production scale.
AI projects deliver measurable and tangible benefits
Pilot plants deploy Artificial Intelligence for seamless transitions from low-scale testing to serial production in production planning, monitoring, and control. In Hildesheim, the plant cut cycle times by 15% in new line production ramp-up, thanks to AI-driven data analysis. Similarly, the plant in Stuttgart-Feuerbach reduced component testing processes from 3.5 minutes to 3 minutes, using new algorithms.
At the plant in Hildesheim, synthetically generated images have already been successfully used for training in the first series of systems in electric motor production. The artificially generated images cannot be distinguished from real images with the human eye.
Optimizing Quality Assurance by Eliminating Manual Checks
To read more: Künstliche Intelligenz (KI) in der Produktion | Bosch Global