Injection Molding: The Revolution in Glass Processing
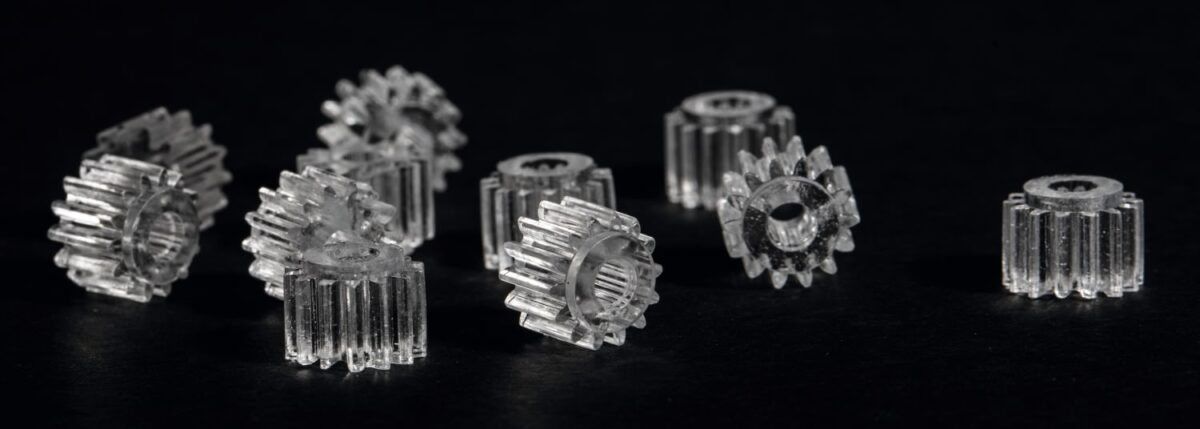
ENGEL and Glassomer make it possible to process transparent quartz glass in a plastic injection molding machine.
Glass stands as a high-performance material vital across multiple fields, notably in optics, chemistry, and medical technology industries. However, conventional glass processing faces constraints, particularly in designing very small structures.
The new process developed by Glassomer in Freiburg, Germany, makes it possible to process transparent quartz glass in the plastic injection molding machine. This method enables the production of thick-walled components, thin-walled components, and highly complex shapes from quartz glass.
Advantages of the injection molding machines
This new approach unleashes a wealth of potential in terms of efficiency and cost-effectiveness, as all conventional processing technologies for glass, such as casting, engraving, and etching, require either very high temperatures or toxic chemicals. On the other hand, molding glass in an injection molding machine is advantageous in terms of not just flexible design but even better, the energy footprint of glass production.
How does it work?
A new type of pellets, containing a high proportion of glass particles from glass fiber production, undergoes injection molding to create transparent glass. The pellets, processed similarly to plastic, utilize temperatures around 130°C with cycle times under 20 seconds. The material, designed for low abrasion, features non-toxic components with common plastic binders. After injection molding, the green body is immersed in a water bath to remove most of the binder, followed by further binder removal in a 600°C oven. This process yields a stable, compacted brown body of powder with high-purity glass particles. Subsequently, sintering transforms the pre-compressed brown body into the final high-purity glass product.
Controlling variables
Controlling the amount of powder used can manage the shrinkage during sintering, typically around 16 percent. During planning, one can precisely calculate this process as the component evenly shrinks all around. The consistent shrinkage allows for the production of shape-retaining components – for example, with perfectly spherical holes. Direct control of surface quality in the mold is achievable by manipulating the composition of the cavity surfaces. The parts can be milky or transparent. When using correspondingly high-quality moulds, the surfaces obtain visual qualities without requiring subsequent treatment.
Precision is a must
As simple as it sounds to process the Glassomer material, it nevertheless requires an injection moulding machine that works with absolute precision.
Any defect in the injection-moulded green body, no matter how small, would be visible in the sintered glass part. With this in mind, Glassomer employs machines from ENGEL’s all-electric and tie-bar-less e-motion TL series. These machines are also instrumental in producing components like polycarbonate smartphone camera lenses and cyclic olefin copolymers.
Glassomer’s new production facilities in Freiburg actively produce high volumes of injection-molded glass components.
The collaborative relationship benefits from ENGEL’s know-how and many years of expertise in the application fields of optics and micro injection molding as well as its experience with mass production processes. The joint development aims to ease entry into new technology with efficient and cost-effective processes and machinery.
Finally, this allows the exchange of transparent plastic parts for high-quality fused silica. This enhances the performance and haptic experience and to introduce lighting and colour effects if the application requires it.