A Multiscale Approach for 3D4d Braided Composite Shafts
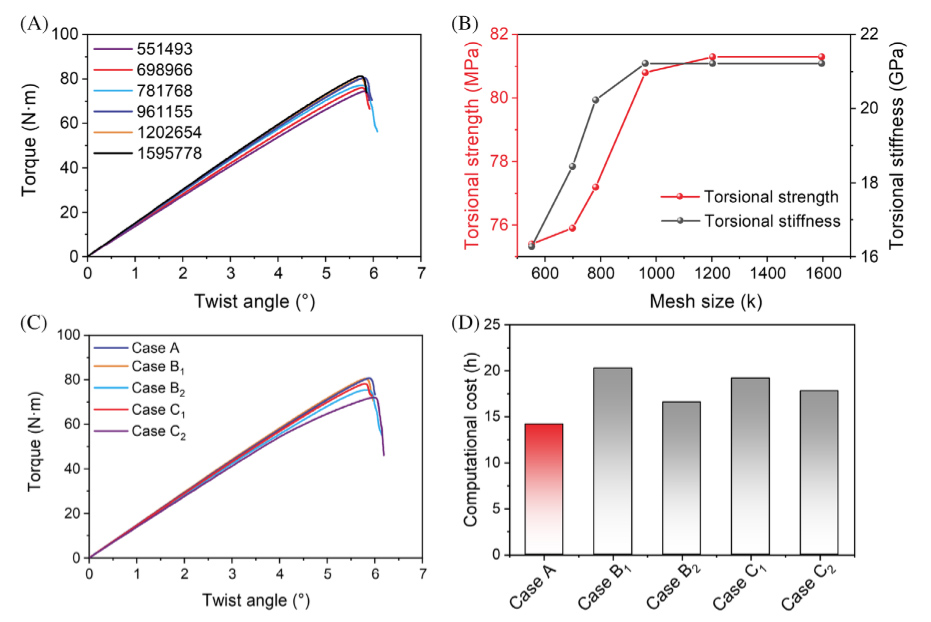
By Plastics Engineering | December 19, 2023
Home » News » Materials » Composites » A Multiscale Approach for 3D4d Braided Composite Shafts
The intricate mechanical properties of three-dimensional (3D) braided composites hold both mystery and promise. Particularly, understanding the nuanced multi-scale damage mechanisms in 3D four-directional (3D4d) braided composite shafts has been a challenge—until now.
In this article, we present a groundbreaking shell-based multiscale finite element model designed to predict compressive and torsional properties effectively. The key innovation lies in the development of a universal tubular unit cell, where the equivalent ply angle is intricately linked to yarn structures. Using deformation gradient theory and Nanson’s formula from continuum mechanics, our model derives the equivalent ply angle through local braiding and horizontal orientation angles, and the elastic properties of each equivalent ply through a stiffness averaging method.
Implementing LaRC04 failure criteria and an energy-based damage evolution law, we characterize the damage behaviors of the equivalent UD-ply. Experimental validation demonstrates excellent agreement between failure morphologies and load–displacement curves of finite element analysis (FEA) and experimental results.
Unveiling the major failure modes—fiber tension and compression damages under compressive and torque loads, respectively—the model provides an efficient tool for the design and manufacturing of 3D4d braided composite shafts. The article concludes with a comprehensive parametric study, contributing meaningful insights to the broader landscape of relevant studies.
This research not only advances our understanding of the mechanical intricacies of 3D4d braided composites but also offers a practical and efficient tool for engineers to design and manufacture these shafts with desired mechanical properties.
You can learn more about this topic in the article “A novel shell-based hierarchical multiscale model for studying three-dimensional four-directional braided composite shafts” by Ya Wang, Zhi-Jian Li, Zheng-Guo Liu, and Yun-Peng Yi, (Polymer Composites. 2023;44:7384-7417, DOI: 10.1002/pc.27632) is chosen for the November 2023 issue of PC. This paper provides a tool for understanding 3D4d braided composite shafts, and therefore allows the design and manufacture of these shafts with desirable mechanical properties. The authors validated the proposed model experimentally, and observed good agreement between the failure morphologies and load–displacement curves of FEA and experimental results.