Scientists Using AI to Accelerate Materials Discovery
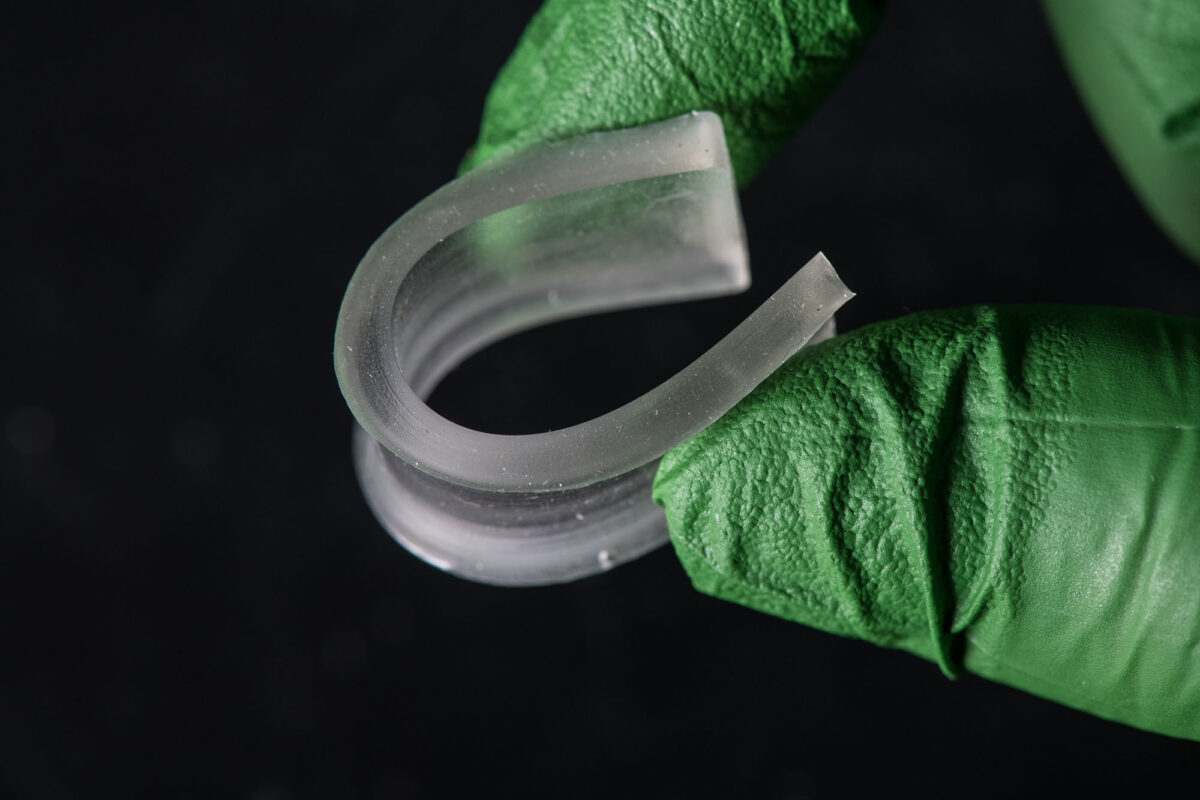
NREL’s new tool, called PolyID, can help scan thousands of polymers for specific properties.
National Renewable Energy Laboratory (NREL) scientists have developed a machine-learning tool to help users find the most sustainable polymers possible for various high-performance applications. The tool –– called PolyID (Polymer Inverse Design) –– uses artificial intelligence (AI) to accelerate materials discovery. It does so by predicting material properties based on molecular structure. That allows it to screen millions of possible polymer designs to create a short list of candidates for any given application.
“Petroleum largely comprises hydrocarbons—essentially arrangements of carbon and hydrogen chemically linked together that have some pretty remarkable and advantageous properties,” said NREL scientist Brandon Knott. “But hydrocarbons lack heteroatoms like oxygen and nitrogen, and it can require significant energy to add them in when manufacturing polymers needing broader functionality than what hydrocarbons provide.”
Mix in some good waste
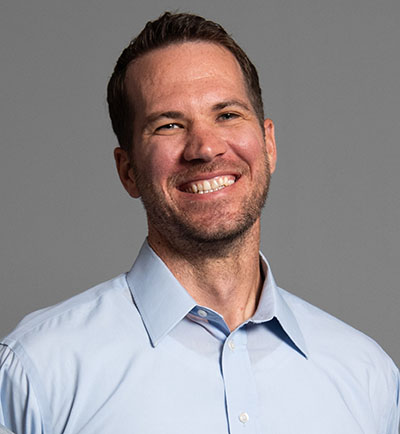
NREL scientist Brandon Knott
A good solution, Knott explained, is adding oxygen- and nitrogen-rich biomass and waste to the ingredient list. Corn stalks, algae, and even garbage contain extra chemical linkages that often afford chemists greater flexibility for achieving specific properties.
Knott noted that the algorithm behind PolyID is “a state-of-the-art advancement to a foundational approach known as ‘group-contribution theory’. The tool builds associations between arrangements of oxygen, hydrogen, carbon, and other elements and material properties to predict attributes like elasticity, heat tolerance, and sealant performance.”
Tailoring polymers to industry’s needs
With thousands of polymers in its reference library, the tool enables scientists to work backward when searching for new polymer designs. They can identify desired properties first and select potential polymer designs.
NREL scientists, for example, used PolyID to rapidly screen more than 15,000 plant-based polymers in search of biodegradable alternatives to today’s food packaging films. Primarily made from HDPE — a petroleum-based material — packaging films are often designed to withstand high temperatures and create a strong vapor seal to keep the food fresh.
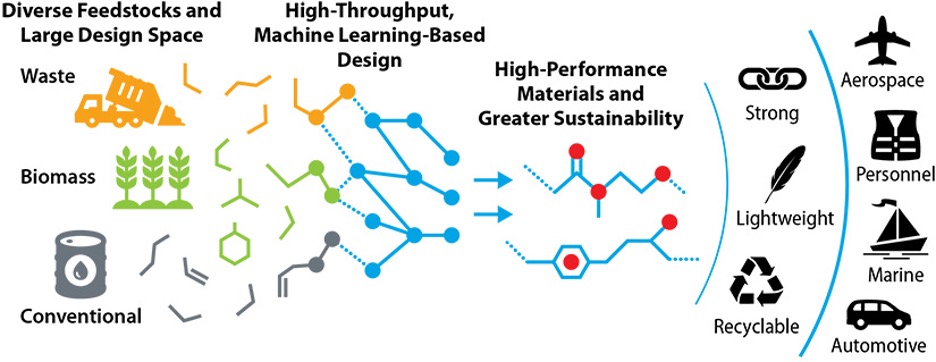
PolyID revolutionizes materials discovery by making it faster and easier than ever to find sustainable and high-performance polymers for a given application. Courtesy of Elizabeth Stone, NREL
NREL’s team prioritized those properties in PolyID while adding other desirable attributes, including biodegradability and a lower greenhouse gas footprint. The tool generated a short list of seven polymer designs that could be made from biomass.
Further lab testing confirmed the tool’s prediction that all seven polymers would not only withstand high temperatures but could also lower net greenhouse gas emissions and keep food fresh for longer periods.
Nolan Wilson, the lead author on the paper, said “Some of these might serve as direct replacements for comparable petroleum polymers,” he explained. “But, in many cases, they are even better in terms of performance and sustainability.”
You can access the online PolyID tool here and read more about it in this Macromolecules article. NREL created PolyID with support from the U.S. Department of Energy Bioenergy Technologies Office.