Scientists Say New Multiblock Polymer Mimics Polyolefin Properties but is More Easily Recycled
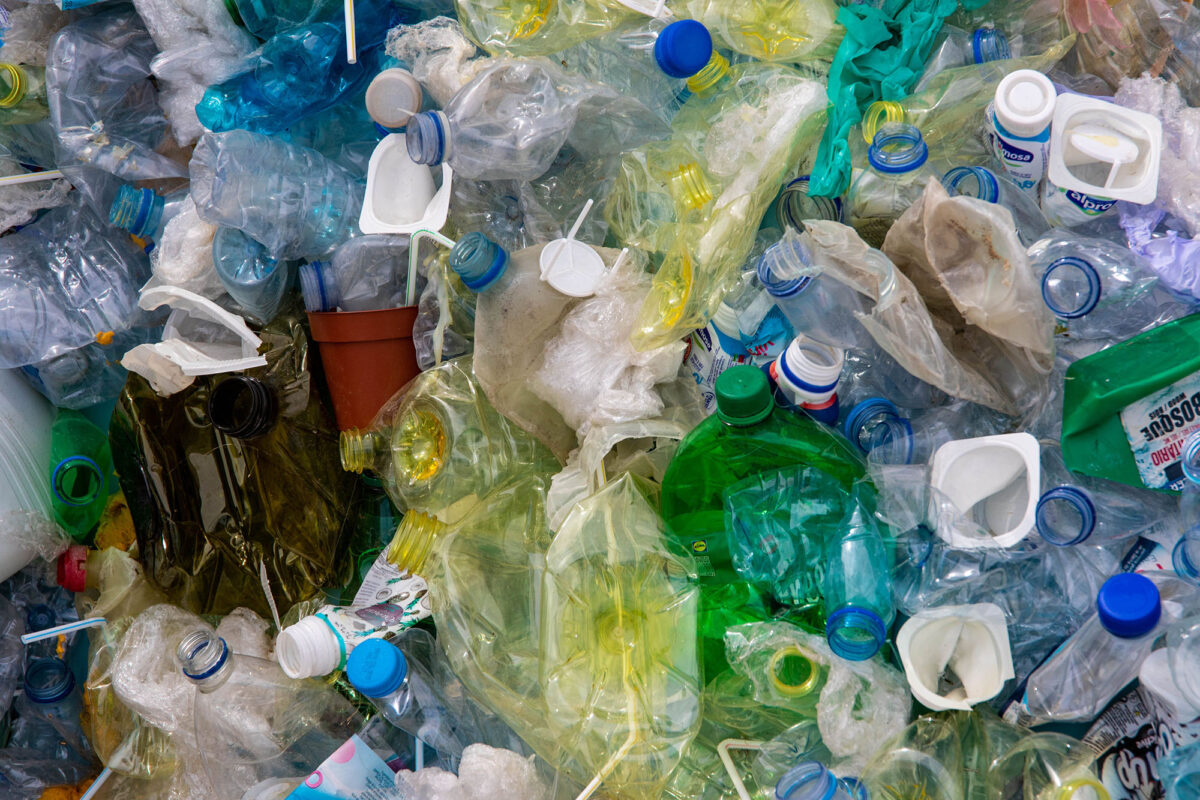
CSU researchers develop way to make diverse, high-value plastics that can be chemically recycled in one stream
A group of scientists at Colorado State University says it has developed a series of polymers that mimic the properties of polyolefins but enable those notoriously stable and durable materials to be chemically recycled more easily. In a world hooked on single-use consumption, they note, the extreme stability of polyolefins’ strong chemical bonds “is no longer a design feature but rather a design flaw.”
It is known that mixing two different plastics together during recycling often greatly diminishes their useful properties — to the point of making them useless. So the team from CSU’s Miyake Research Group set out to rethink plastics, starting by designing for end of use and coming up with ways it could create products with a wide range of mechanical properties from only two building blocks. They also wanted to ensure their methodology could be integrated with existing recycling protocols to recapture value –– or at the very least minimize contamination.
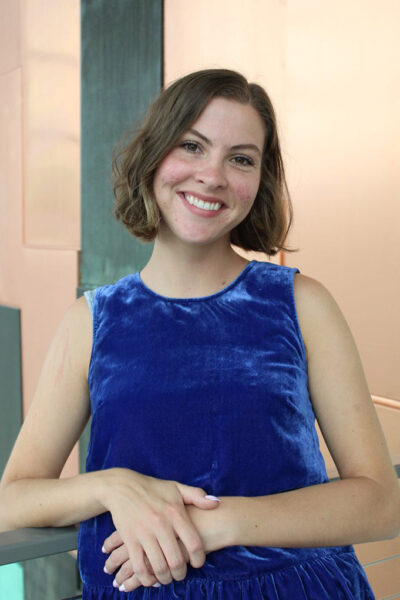
Emma Rettner
The group, which began work on this project about a year ago, published a report on their work in Science magazine on Oct. 19. On the same day, two of its members –– Emma Rettner, a Ph.D. candidate in materials science and engineering, and Katherine Harry, a Ph.D. candidate in chemistry –– expanded further upon it in an article in the independent, nonprofit publication The Conversation. They shared additional thoughts with Plastics Engineering in an Oct. 31 phone interview.
“When we mixed samples of polypropylene with a polymer we made,” they wrote, “we were still able to depolymerize—or break down the material—and regain our building blocks without chemically affecting the polypropylene. This indicated that a contaminated waste stream could still recover its value, and the material in it could go on to be recycled, either mechanically or chemically.”
Building multiblock polymers
The team further explained that it started with just two simple polymer building blocks –– one soft polymer and one hard polymer –– and then link these into a single, long molecule called a multiblock polymer. “By just by adjusting how much of each polymer type goes into the multiblock polymer, our team created a wide range of materials with properties that spanned across polyolefin types.”
“We’re not the first to make multiblock polymers,” acknowledged Rettner, “but they’re very challenging to make synthetically and this methodology really enables that.”
The team achieved this by adapting a technique that had previously been used on very small molecules. This method, she explained, is improved relative to traditional methods of making polymers in a step-by-step fashion, developed in the 1920s, where the reactive groups on the end of the molecules need to be exactly matched.
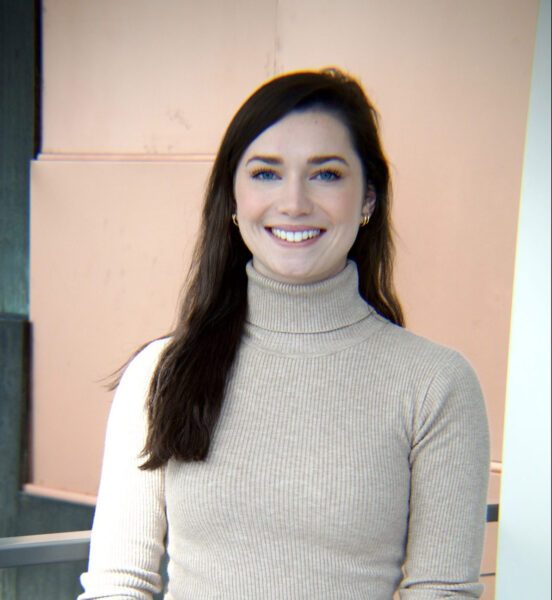
Katherine Harry
“In our method,” said Rettner and Harry, “the reactive groups are now the same as each other, meaning we didn’t have to worry about pairing the ends of each building block to make polymers that can compete with the polyolefins we already use. Using the same strategy, applied in reverse by adding hydrogen, we could disconnect the polymers back into their building blocks and easily separate them to use again.”
The group contends that using just two building blocks to make plastics that have a wide range of properties can help reduce and streamline the number of different plastics used to make the products that are needed.
“We wanted to make polyolefin-like materials,” Rettner said, “because there are so many examples of them and we’re really familiar with what performance is needed for those materials to be successful, but they are really challenging to characterize because of how inert they are.”
Harry said the group currently is running several additional projects related to this work to address ongoing questions and gain more fundamental understanding of the system. She added that the team’s ultimate goal is to access such a diverse range of properties that the resulting materials could, potentially, replace a vast range of useful plastics. “That would have the most impact,” she said.