How does the PFAS ban affect the plastics industry?
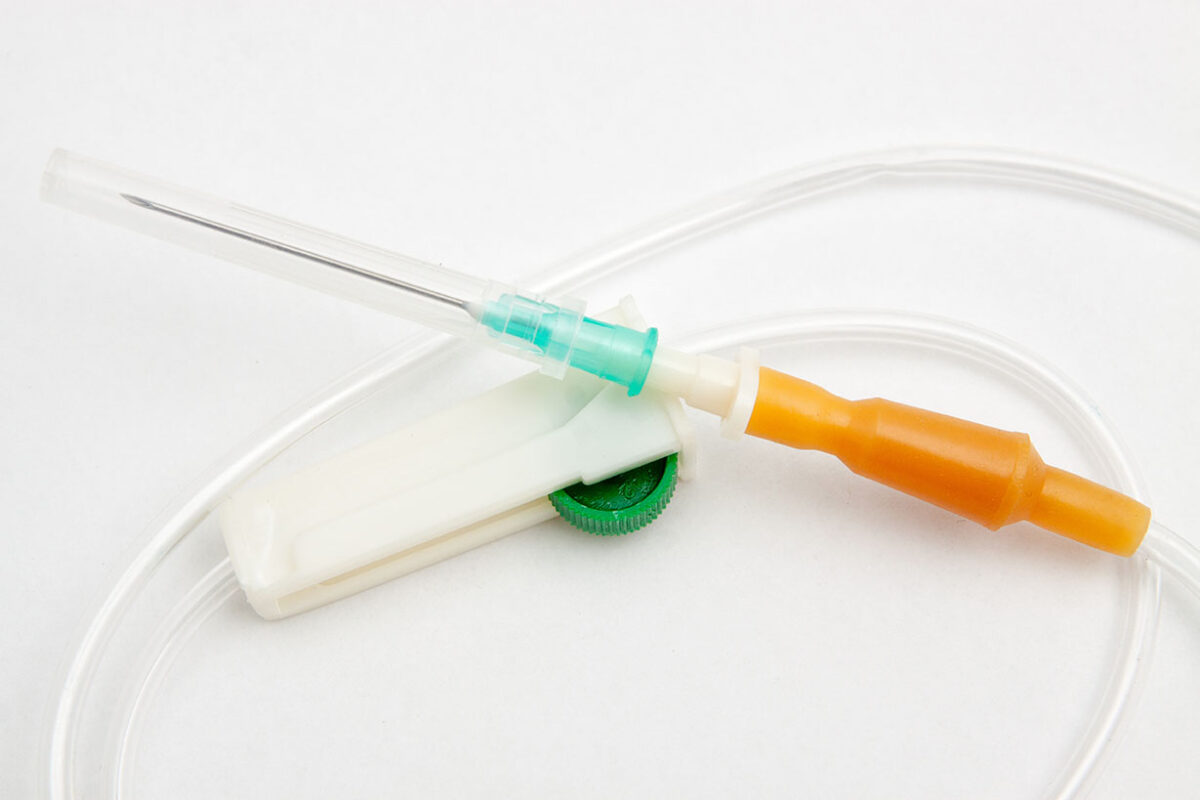
Many applications rely on PFASs and fluoropolymers, but not in all cases can they be substituted as quickly as the legislation requires.
PFASs are on their way to being prohibited in the European Union, and the U.S. will continue that policy. According to the European Chemicals Agency classification, most fluoropolymers fall into perfluoroalkylated and polyfluoroalkylated substances (PFAS), which justifies their ban. But what about applications that rely on them?
Switch to PFAS-free alternatives
Companies now have two options, try to switch to PFAS-free solutions or ask for an exemption, which could be temporary.
Since using PFAS as polymerization aids is the main cause of PFAS emissions related to the fluoropolymer life cycle, several additive companies have developed PFAS-free auxiliaries to comply with the looming ban.
Companies such as Avient, AMPACET, MOMENTIVE, BAERLOCHER, and GFL have developed different polymer processing aids with different chemistries. Depending on the application, one will be more suitable than another. These solutions directly solve problems such as melt fracture, matrix formation, energy consumption, dimensional and thermal stability, and flame retardancy.
Finding a substitute as quickly as the legislation requires
Other industries, such as biomedical, use fluoropolymers, especially PTFE, for a wide variety of products, from surgical instruments to guidewires and catheters. This is because PTFE has the lowest coefficient of friction of all polymers, and is self-lubricating and inert. Another concern is the rigorous regulation of medical devices, making material changes a lengthy and approval-intensive process.
The aerospace sector, also, may encounter challenges in substituting PFAS due to its need for standardized solutions, potentially extending the transition period.
But requesting an exception is, for many experts, an option to gain time to move to a PFAS-free solution. In the long term, this could create a crisis in the material supply chain, as some PFAS producers may choose to withdraw from the market in 2025.