Building Blocks Made of Plastics Waste Spur Affordable Construction
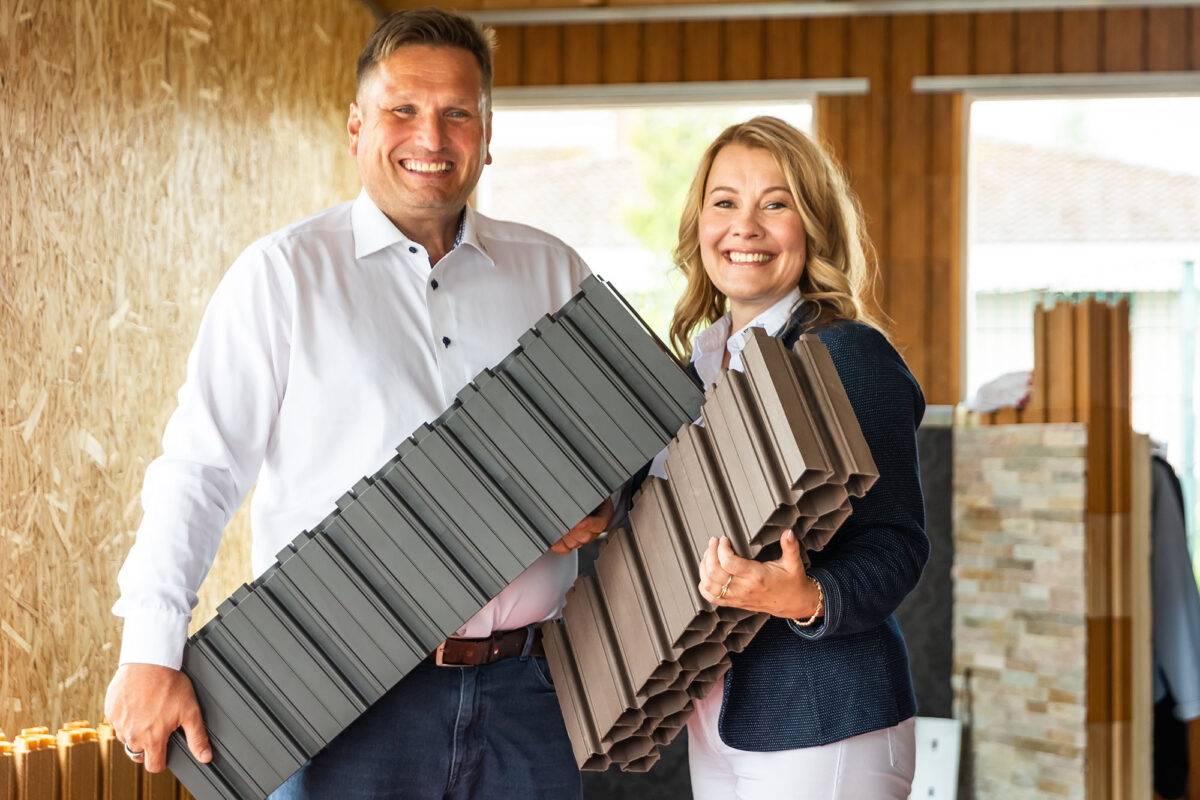
Finnish firm taps plastics waste for rapid, low-cost construction of housing and commercial buildings
Block Solutions Oy, of Mutala, Finland, wants to make sustainable and affordable building construction a snap. And the concept is quickly catching on globally.
Prompted in 2016 by discussions with the United Nations and driven by a desire to create a way to quickly build shelter for people in need, Markus Silfverberg conceived the idea of eco-friendly modular blocks. The aim was for these blocks to be used to easily build strong, safe structures without electricity or machinery or even highly skilled workers.
With master’s degrees in international business and industrial engineering from Tampere University in Finland, he pursued the idea. And so, Block Solutions was born. Silfverberg’s small team initially produced numerous 3D-printed versions until the team figured out the right shape and method of production. They then built a miniature house in a garage.
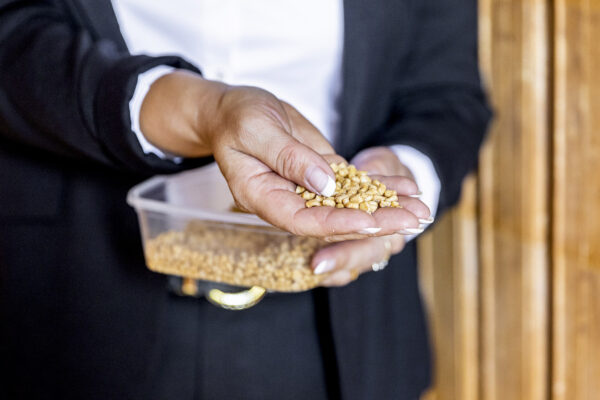
The biocomposite material typically uses a mix of waste polypropylene and wood fiber byproducts.
A key to the firm’s technology is the biocomposite it has developed using a mixture of recycled polypropylene (PP) and other plastics with wood fiber byproducts from Finland’s forest industry. The resulting material is typically half recycled plastics and half organic fibers and does not incorporate any additives into the compounds.
Block Solutions (or their partners) then injection molds the biocomposite into forms that resemble large, interlocking, Lego-like blocks that snap together and can be used to construct low-cost buildings. They typically use 650-ton injection presses but will consider using 1,250-ton molding machines with dual-cavity molds when the right opportunity arises.
The only tools required are a rubber hammer, a water level and a ring wrench. No electricity is needed. Blocks can be used to construct the walls of the building and can be modified with normal woodworking machines, for example, to cut out holes for electrical sockets. “A 30-square-meter (322.9-square-foot) building can be built in 2.5 hours by two persons without any professional experience in construction,” the company says.
‘Classrooms of Hope’
The company, in collaboration with the Australian non-governmental organization (NGO) Classroom of Hope Ltd., built a five-room schoolhouse on the Indonesian island of Lombok, which was devastated by an earthquake in 2018. Duncan Ward, the Indonesia-based founder of Classroom of Hope, said of the project in late 2021: “It took six days to build the school with these things. It would usually take around three to six months [to build a school], but these blocks are fully interlocking and come in groups of two, four and eight, which makes things quicker.” It also cost about half the price of a conventionally constructed classroom in Southeast Asia, he added.
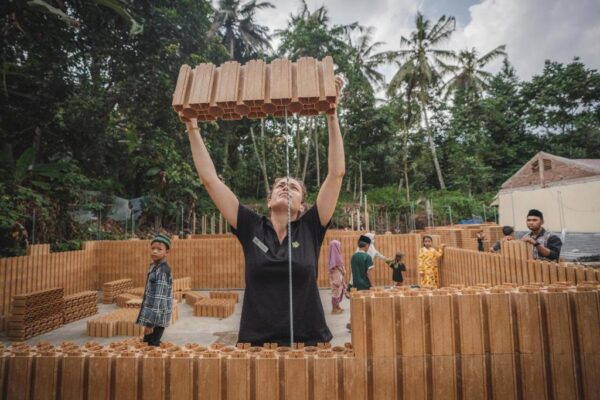
Block Solutions partnered with NGO Classroom of Hope to build in six days a five-room schoolhouse in Lombok, Indonesia, which replaced a structure destroyed by earthquake.
Once Block Solutions’ new factory—its first purpose-built facility—opens this summer on Lombok, Classroom of Hope will become a major customer. The South African-born Ward told Pro Bono Australia in late 2021 that his group will launch a program to build an additional 200 Lombok schools to replace those that were lost in the earthquake. Additionally, he said, “For every classroom we can build [with Blocks], we’re also removing two to three [metric] tons of plastics waste from the environment.”
As an added benefit, the plastics content in the base material lends the lightweight blocks a degree of elasticity, making them less likely to cause significant harm in earthquake-prone areas. The weight of the Block wall is only one-tenth that of a conventional cinder-block wall, but the Blocks still offer roughly twice the load-bearing strength of typical 5-inch cinder blocks.
The Blocks, which are patented in some countries and have patents pending in others, do have to be covered with gypsum board or concrete to comply with necessary fire-resistance requirements.
CEO Sanna Silfverberg says her firm collects its plastics feedstock from “normal household waste or other sources with safe and traceable origins.” The firm’s recycling partners “provide us with proof of origin for the material,” she added. “This is really to make sure that the blocks are safe to build with.”
Polypropylene Benefits
She said the company can use waste PP, polyethylene (PE) or PET, and continues to investigate other resins, though PP has demonstrated the best properties to date. It is the most suitable resin for processing and gives good-quality finishing and strength.
“PE is also very close in performance to PP, but a little softer,” Silfverberg noted. “PET has a slight disadvantage with the weight and processing, but it is working nicely in the production.”
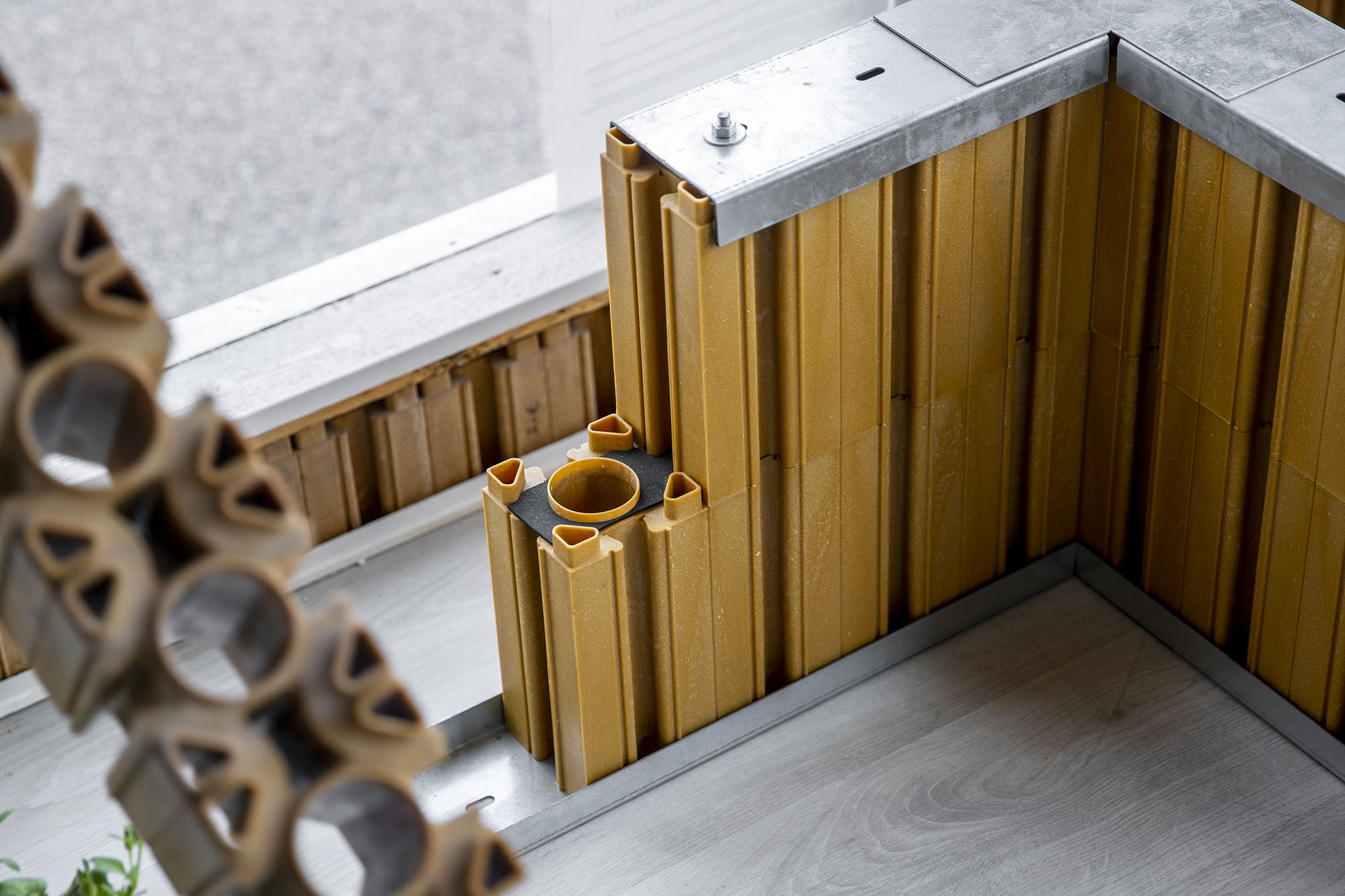
The injection molded Blocks resemble Legos and fit together in a similar fashion. Individuals with no professional construction experience can construct a building quickly using only a rubber hammer, level and wrench.
To date, Block Solutions uses its biocomposite mostly in Finland, as it is not yet widely available. “We have been doing a lot of R&D to increase the fiber sources significantly,” Sanna Silfverberg explained recently via email. “We have developed recipes for using bamboo, rice husk, sugar cane, coconut husk and even old, recycled clothes to access excess fibers in the local market. We have already been producing Blocks out of textile, coconut husk and rice husk mixed about 50/50 percent together with recycled polypropylene. This is our way to lower the carbon footprint to the bare minimum,” she said, noting that “the carbon footprint of our product is close to zero.”
The COVID-19 pandemic proved to be disruptive, but Block Solutions persevered and focused on creating factories around the world.
“We are already producing the Blocks in Jakarta, Indonesia, in an OEM’s plant,” Sanna Silfverberg said. The OEM, which also produces other plastics parts in its factory, began molding Blocks last December.
“The Lombok plant is the first custom-made plant based solely on the needs of Block Solutions,” she explained. Designed from scratch to accommodate only Blocks production, it will have the capacity to produce enough Blocks for 2,400 homes annually using only locally sourced raw materials. Once the plant opens in June, plans call for the OEM-based plant in Jakarta to continue producing Blocks, to supplement production.
Miniplast Ltd., an OEM molder in Accra, Ghana, began producing Blocks in May 2022. Miniplast operates a large recycling facility and dozens of injection molding machines. A factory in Cairo, meanwhile, started production in late 2022 with a capacity per line of about 350,000 Blocks per year.
Demand for Blocks continues to increase rapidly in Asia, and Silfverberg said Block Solutions is on track to launch two or three additional factories in the region this year. “If schedules allow,” she remarked, “we will have at least an operational plant in Thailand and India by the end of 2023.”
A Typical Blocks Plant
The normal indoor footprint of one plant, she explained, is about 300 square meters (3,229 square feet) with the capacity to make components for about 2,400 homes per year. The capital investment varies based on location, “but generally we are starting from €1.1 million (about $1.21 million), plus €300,000 euros for working capital. Usually there are some governmental incentives, but the funding is mainly coming from the entrepreneurs themselves and impact investors. One plant will employ directly between 20 to 30 people, but indirectly up to 400 people, mainly in construction and waste collection.”
Block Solutions also has its sights set on the United States. While multiple locations are engaged in the process, the most likely location for a new plant will be in Omaha, Neb., according to Silfverberg. “They are well on their way with existing model housing and agreements with recycling companies.”
Meantime, work continues on expanding the company’s portfolio via what she called “a new add-on product” that would help to enable construction of multi-story buildings. While most current buildings are one story high, the Blocks’ light weight allows them to be easily carried to upper floors, which the company says will have a dramatic impact on labor costs and time.
One square meter of a Blocks wall only weighs about 20 kg (44 pounds) compared with 200 kg for traditional brick and mortar construction. This means a weight savings of 18,000 kg per 100 square meters of partitioning wall per floor. Two– and three-story Block buildings have been constructed, and the developing technology will enable more.
“The research and development are done in Finland, and we are continuously improving and enhancing the product. The corner block is a novelty in the product line and will allow us to start building multi-story buildings without a major reduction in our demand for cutting carbon emissions.” The product will most likely be deployed first in Saudi Arabia, she said.
This newly designed corner block allows easy installation of insulation panels to cut down on heating and cooling costs, resulting in lower life cycle costs. The new structure will also allow future users to dismantle the Blocks without having to mechanically remove different materials from them. “This means a huge improvement for recycling in the future,” Silfverberg said.
If the Silfverbergs have their way, Block Solutions—with just seven full-time staff in Finland and licensees worldwide—will reshape how safe, low-cost construction is done in areas of need.
This story first appeared in the May/June 2023 issue of Plastics Engineering.
Color black or need additive or avoid sunlight
Need to know resin base to set molding conditions. Moisture control for wood fiber and PET…. Finance of molds and their time use are critical.
Do you have photos of a finished home including kitchen and bathroom? Also photos of the exterior with doors, windows and roof?
This post highlights an innovative approach to addressing two critical issues: plastic waste and housing shortages. I’m really intrigued by the potential of using recycled plastics in construction. It’s a great way to tackle environmental concerns while also providing affordable housing solutions. I would love to see more case studies on successful projects using these methods!
This is a fascinating approach to addressing both housing shortages and plastic waste! It’s incredible to see how innovative thinking can turn environmental challenges into sustainable solutions. I’m curious about the durability and safety of these materials in various climates. Looking forward to seeing more developments in this area!
This is such an insightful post! It’s amazing to see how we can repurpose plastic waste into sustainable building materials. The potential for reducing environmental impact while addressing housing needs is truly inspiring. I’m looking forward to seeing more innovative solutions like this in the future!
This blog post offers a fascinating perspective on how we can utilize plastic waste for sustainable housing solutions. It’s incredible to see innovative ideas that not only address housing shortages but also tackle the pressing issue of plastic waste. I would love to learn more about the real-world applications of these materials in construction and the challenges faced in implementing such initiatives!
This is a fascinating approach to tackling the dual issues of plastic waste and housing shortages! I’m intrigued by the potential of using recycled plastics not just for eco-friendly buildings but also in making housing more affordable. It would be great to see more examples of successful projects and the technology behind these innovations. Looking forward to seeing how this field develops!
This approach to repurposing plastic waste for housing is both innovative and necessary. It’s amazing to see how we can tackle two major issues—plastic pollution and the housing crisis—simultaneously. I’m curious about the structural integrity and long-term sustainability of these materials. Looking forward to seeing more developments in this field!
This is a fascinating approach to tackling the plastic waste problem! Utilizing plastics for rapid, low-cost housing could really transform how we think about waste management and affordable housing. I’m curious about the long-term durability and sustainability of these materials in different climates. Great insights!