A Closer Look at 3D Printing Materials: Composites
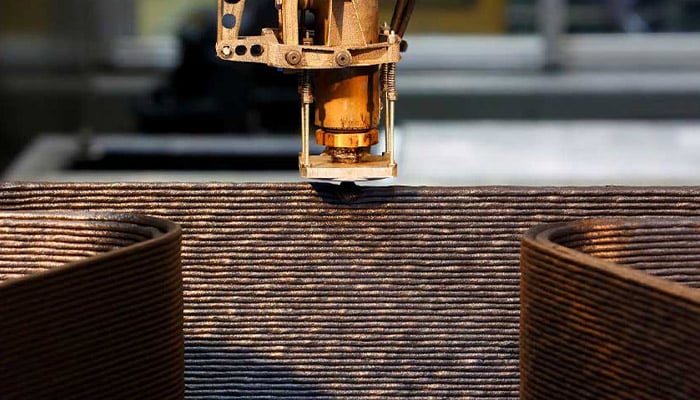
In 3D printing, composite materials have emerged as a groundbreaking frontier, offering unparalleled possibilities in various industries. The composite 3D printing market is projected to soar to $1.73 billion by 2030, highlighting the widespread adoption of this technology. Composite 3D printing involves blending a plastic matrix with reinforcing fibers, with carbon fiber, fiberglass, and Kevlar as the primary players.
Carbon Fiber Reinforced Materials
Carbon fiber, originating in 1860, has become a cornerstone in composite materials. Its crystalline structure and exceptional strength-to-weight ratio make it ideal for crafting lightweight and robust end parts. However, the integration of carbon fibers in 3D printing demands specific considerations, such as using a hardened steel print nozzle and choosing compatible matrix materials like PLA, PETG, or ABS.
Fiberglass Reinforced Composite Materials
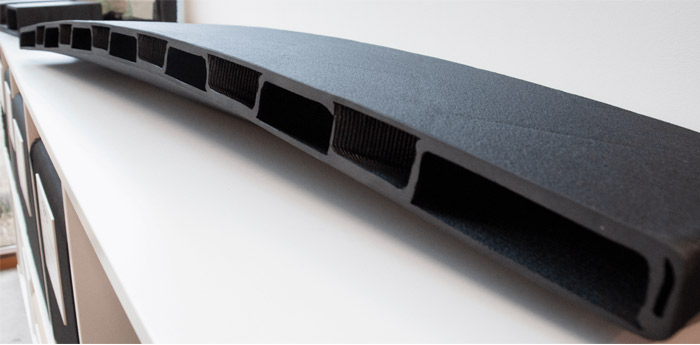
Prototype of a bridge part printed using fiberglass. Courtesy of CEAM
Introduced in 1930, fiberglass is a versatile reinforcement for thermoplastic polymers, offering parts ten times stronger than ABS. While exhibiting less rigidity than carbon-based materials, fiberglass composites boast cost-effectiveness, commendable mechanical properties, electrical insulation, and low thermal conductivity. This makes them valuable for engineering prototypes and end-use parts in industries ranging from construction to marine applications.
Kevlar Reinforced Materials
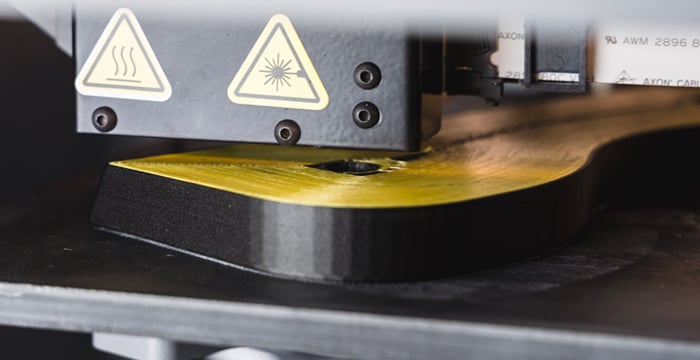
3D printing of a Kevlar composite material. Courtesy of Markforged
Developed by DuPont de Nemours in 1971, Kevlar stands out for its durability and exceptional mechanical traits. As an aramid fiber, Kevlar is known for its robust properties, surpassing steel with a fivefold strength-to-weight ratio. Employed in combination with plastics, Kevlar is a preferred choice for components requiring abrasion resistance and enduring intense vibrations. Its low density, versatile applications, and uniform molecular structure make it a prime candidate for additive manufacturing.
These composite materials have found applications across diverse sectors, from automotive to construction, illustrating their adaptability and transformative impact on contemporary manufacturing. Whether it’s crafting lightweight components with carbon fiber, reinforcing parts with fiberglass for superior strength, or leveraging Kevlar for exceptional durability, the world of composite 3D printing is reshaping the landscape of additive manufacturing. As industries continue to embrace these innovations, the future holds exciting possibilities for customized, high-quality, and functionally superior parts.