Bioactive Bone Implants: The ELAINE Project’s 3D Printing Breakthrough
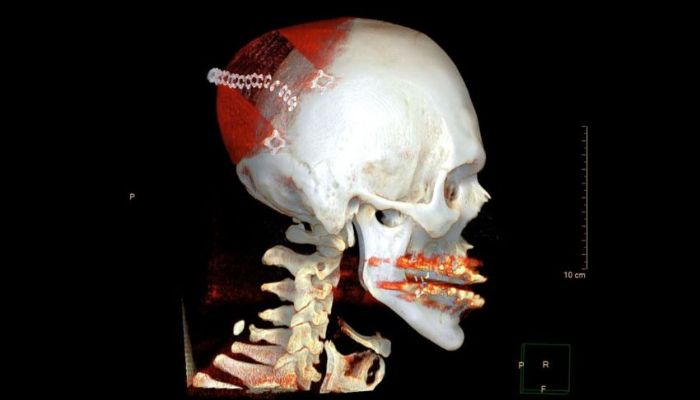
In the realm of medical innovation, 3D printing technology has opened new horizons, especially in the field of bone implants. One groundbreaking initiative, the Electrically Active ImplaNtatE (ELAINE) project at the University of Rostock, Germany, is at the forefront of research into 3D-printed bioactive bone replacements. Led by Professor Dr. Hermann Seitz, this Collaborative Research Center 1270 is redefining the future of bone implants.
The Challenge of Bone Regeneration
While bones possess remarkable self-healing abilities, they have limitations. In cases of extensive bone damage due to factors like tumors, traditional healing processes become insufficient. Conventionally, implants made of titanium or the patient’s own bone material have been employed. However, these solutions have shortcomings, such as inadequate adaptation to individual anatomy and potential long-term complications.
The ELAINE Project’s 3D Printing Revolution
The ELAINE research group recognized the need for a more advanced and patient-specific approach. They turned to 3D printing technology to craft bioactive bone implants that mimic the behavior of natural bone structures. Guided by the physiology of bones, the team leveraged their knowledge of piezoelectricity in bones, a phenomenon where mechanical deformation generates electrical signals that stimulate bone growth.
The Role of Piezoelectricity in Implants
Intriguingly, ELAINE researchers crafted implants from piezoelectric ceramics, specifically barium titanate, using 3D printing techniques. Barium titanate, known for generating voltage potentials under pressure, was combined with bioactive glasses. When exposed to bodily fluids, these materials release ions, thus displaying their bioactivity. The result is a bioactive implant, created through 3D printing, that closely mimics natural bone behavior.
Customization Through 3D Printing
One of the major advantages of 3D printing is customization. With digital reconstruction, ELAINE’s implants are tailored precisely to each patient’s unique anatomy. By utilizing Lithoz’s lithography-based ceramics manufacturing (LCM) technology, the team creates intricate structures by curing a photosensitive polymer loaded with piezoceramic particles. After a thermal post-processing stage, the sterile and biocompatible implants are ready for insertion.
The ELAINE project is not without its challenges. While their results show promise, there is still much basic research to be conducted before these 3D-printed bone implants can be widely used in clinical settings. It may take another decade or so to fully comprehend the underlying mechanisms and ensure safe and effective implementation. Nevertheless, the path is set, and 3D printing is poised to revolutionize the future of medical implants, offering a beacon of hope for patients with bone defects.
As ELAINE pioneers the frontier of 3D-printed bioactive bone implants, it’s clear that innovation knows no bounds in the quest to improve healthcare and quality of life. The intersection of technology and medicine promises a brighter, more customized future for patients in need of bone replacements.