Aurum Thermoplastic Polyimide Is a Highlight of Fakuma Expo
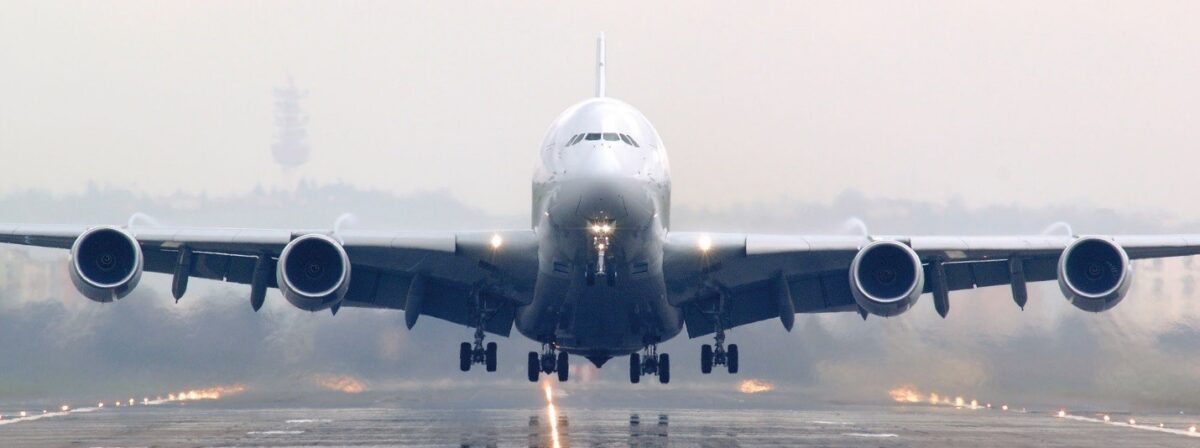
Mitsui polymer yields high heat resistance, dimensional stability and other key properties
The Fakuma international expo for plastics processing opens Oct. 17, in Friedrichshafen, Germany. Some 1,500 exhibitors will show a range of new and recently developed products and technologies for machinery, molds and dies, materials, automation, processing operations and related gear.
Though primarily a machinery and equipment show, there will also be many innovative materials on display. One which is bound to attract attention is Aurum, a thermoplastic polyimide from Mitsui Chemicals Inc., of Tokyo (U.S. offices are in Rye Brook, N.Y., and San Jose, Calif., us.mitsuichemicals.com), that reportedly combines the performance benefits of a polyimide, usually a thermoset, with the processability of a thermoplastic.
Aurum is not new. It was first presented in a research paper in 2004 as a thermoset polyimide. Over the years, however, Mitsui has tweaked the chemistry to produce a thermoplastic version of the material with various grades—and it is these that continue to attract attention, as high-performance thermoplastics are increasingly specified for lightweight metal replacements in automotive, aerospace, heavy machinery and nuclear power components among other demanding applications.
Mitsui describes Aurum as a “high-heat-resistant super engineering plastic that enables high-efficiency production through injection molding, challenging the conventional thinking that polyimides have outstanding performance but are difficult to process.”
Aurum’s glass transition temperature, Mitsui says, is 245℃ (473°F), suitable for most high-temperature parts and higher than that of polyetheretherketone (PEEK). Aurum is also said to be more dimensionally stable than PEEK, and to outperform polytetrafluoroethylene. The resin is melt-processable and can be injection molded or extruded. It can also be applied in powder form for insulation and wire coating in electronics and other end uses.
Properties such as high-temperature stiffness above 150℃ (302°F) and compatibility with fiber reinforcement make Aurum more workable than PEEK, Mitsui states. Due to these and other properties, Aurum has been specified for automotive thrust washers, seal rings, bearing retainers and bearings. In aerospace it is used in the structural components of aircraft engines.
When compounded and filled with additives, Aurum’s coefficient of expansion can be controlled. This makes it suitable for automotive, as well as for pistons, oil pumps and oil seals in construction machinery.
Aurum grades reportedly exhibit the highest critical PV (pressure x velocity—the value equal to the maximum combination of pressure and speed that a bearing material is capable of withstanding) of any thermoplastic in a non-lubricated sliding atmosphere. This property is useful in such applications as bearing retainers, thrust washers, seals and related parts.
Properties of low outgassing at high temperature and resistance to radiation with minimum reduction in tensile strength make Aurum applicable in building switches and socket components for nuclear power and other applications in harsh working atmospheres like those in the oil and gas industry.
The resin also has high dimensional stability.