Brunswick Calls New Veer Brand a Boat/Kayak Hybrid
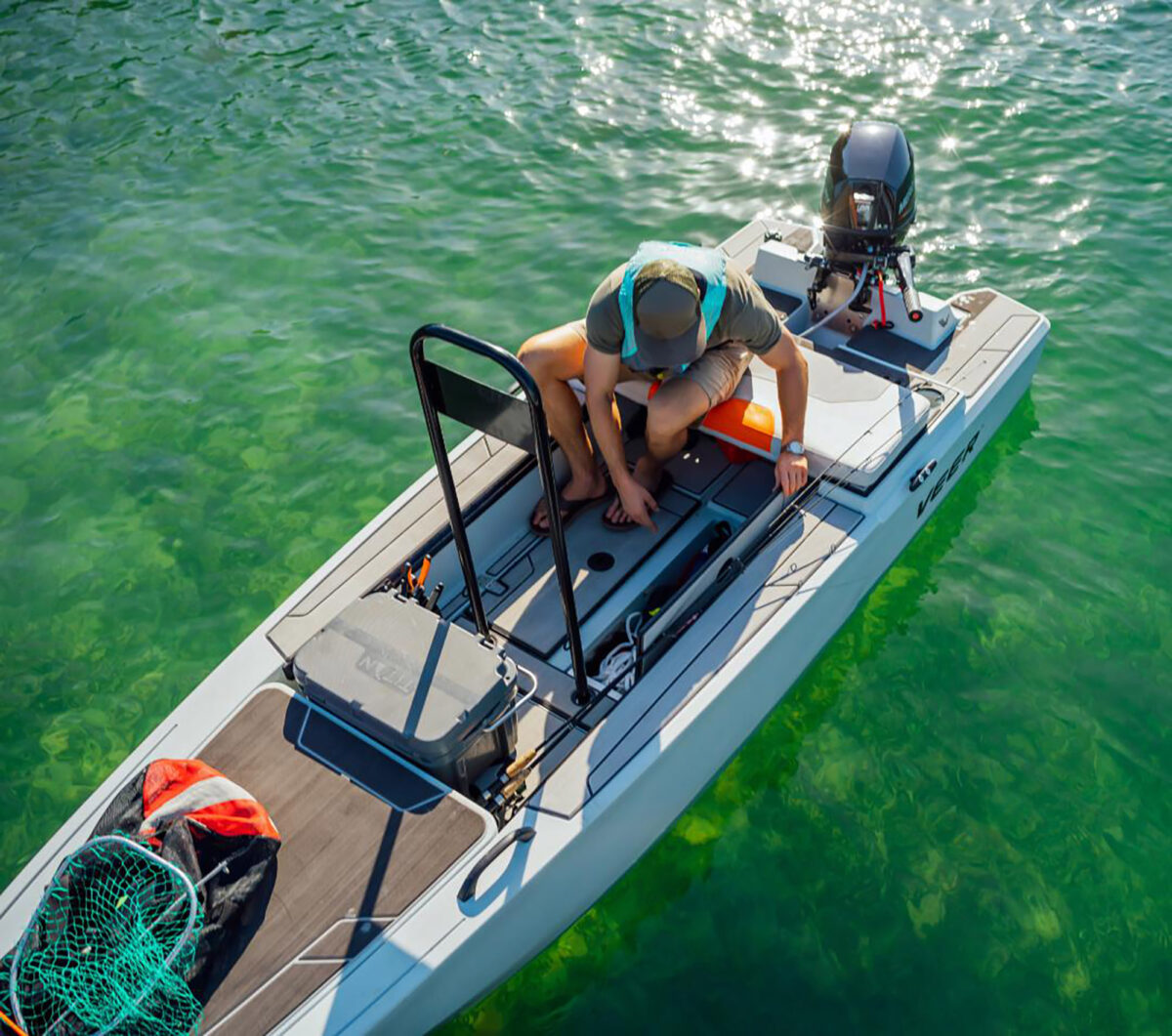
Forte Products is rotomolding the 13-foot polyethylene vessel
IDEA 2023: Part seven of a series
Brunswick Corp. hopes to introduce pleasure boating to a new generation of customers with its latest model—an affordable, 13-foot, rotationally molded, polyethylene vessel that it describes as a hybrid between a kayak and a boat.
Dubbed Veer, the brand earned a Bronze International Design Excellence Award (IDEA) recently from the Industrial Designers Society of America.
Chicago-based Brunswick, which was founded in 1845 and posted $6.81 billion of sales in 2022, owns major boating brands such as Sea Ray, Boston Whaler, Bayliner and Mercury Marine. It says its new Veer product line is designed to support electric propulsion and appeal to the next generation of boaters. The first model in the lineup, the V13, has intuitive controls and advanced digital displays integrated into the design and produces no direct emissions. It introduced the boat at two events earlier this year and began shipping product last May.
Brian Gross, Brunswick’s Minnesota-based vice president of product design and engineering, and Zach Handziak, a Tennessee-based senior designer with the firm, spoke with Plastics Engineering recently to elaborate on the Veer’s design journey.
Explaining Veer’s Design Philosophy
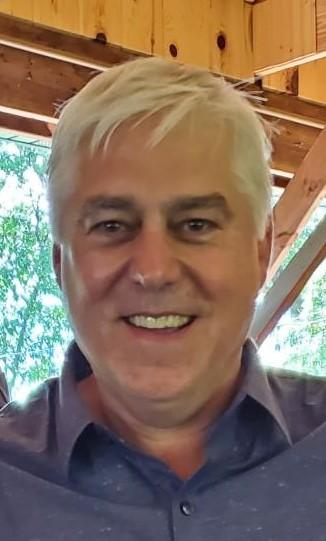
Brunswick Vice President Brian Gross.
Gross said Brunswick started with a different boat project but learned that they were designing too much complexity into the tool. “Some people were thinking we should be able to manufacture product similar to injection molded parts that are very well dimensionally controlled,” he said. Not so with rotational molding.
They applied the lessons learned and launched the Veer project. Gross and Handziak limited the features and removed all the inserts from the mold. Instead, they decided to do a post-molding operation to add inserts and other features.
For a 13-foot boat, Gross said, it can shrink up to three inches over the length of the boat as it comes out and cools. “We added jigs and fixtures to help control that. We built in a shear-tie structure within this boat to help give it rigidity and structural integrity.”
In rotomolding, added Handziak, this is called a kiss-off. “Getting those in the right locations was huge. We went through about five versions of that until we got the right structural requirement.”
The motivation behind the Veer, he explained, “was to create something more affordable, to get younger people into boating and make boating more accessible.” They needed something durable, easy to maneuver and lightweight (given its electric propulsion option). The end product also needed to be easy to stow and to tow using a trailer with just a car or a small SUV.
“We wanted to create a hybrid between a kayak and a boat. Kayaks can get into really tight spaces, they’re low maintenance, but we also wanted to add capabilities to it that you don’t often see in the kayak world.”
Farmington, Mo.-based Forte Products does the rotomolding for Brunswick, using a medium- to high-density polyethylene grade. Gross said they chose the resin for processing ease and availability.
Solving Adhesion Issues Was Vital
Still, manufacturing the boat, which also uses foamed PE for rigidity and flotation, had challenges. “Almost nothing wants to stick to polyethylene,” he noted. “So, we used a plasma-etched polyethylene with a Foamazol foaming agent in the second shot. The foaming agent adds an expanded layer of polyethylene for stiffness and the plasma-etched material allows the floatation foam (two-part rigid polyurethane foam) to bond [to it].”
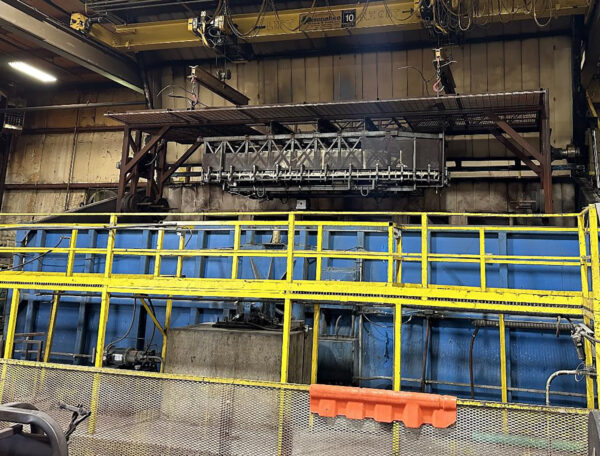
Forte Products bakes the polyethylene boat in the rotomolding oven.
They do an ozone treating process between the finished rotomolding process and adding the floatation foam. The ozone treats the inside surface to prepare the material for better foam adhesion.
The Veer consists of two rotomolded PE parts—the single-piece hull, which measures about 13 feet, 6 inches by 48 inches wide, and the bow lid, which is a secondary piece that sits in the front of the boat to be used as a standing/casting deck. Using rotomolding, Handziak said, “We can get really tight radii and some sharp features that allow the boat to have that modern, sleek aesthetic.” (See Veer video.)
Brunswick had a wide array of color options, he said, but they opted for seafoam green and a light gray. The firm has already shipped more than 100 of the boats to dealers and customers and is targeting first-year sales of about 200 units. It is priced at just under $12,000.
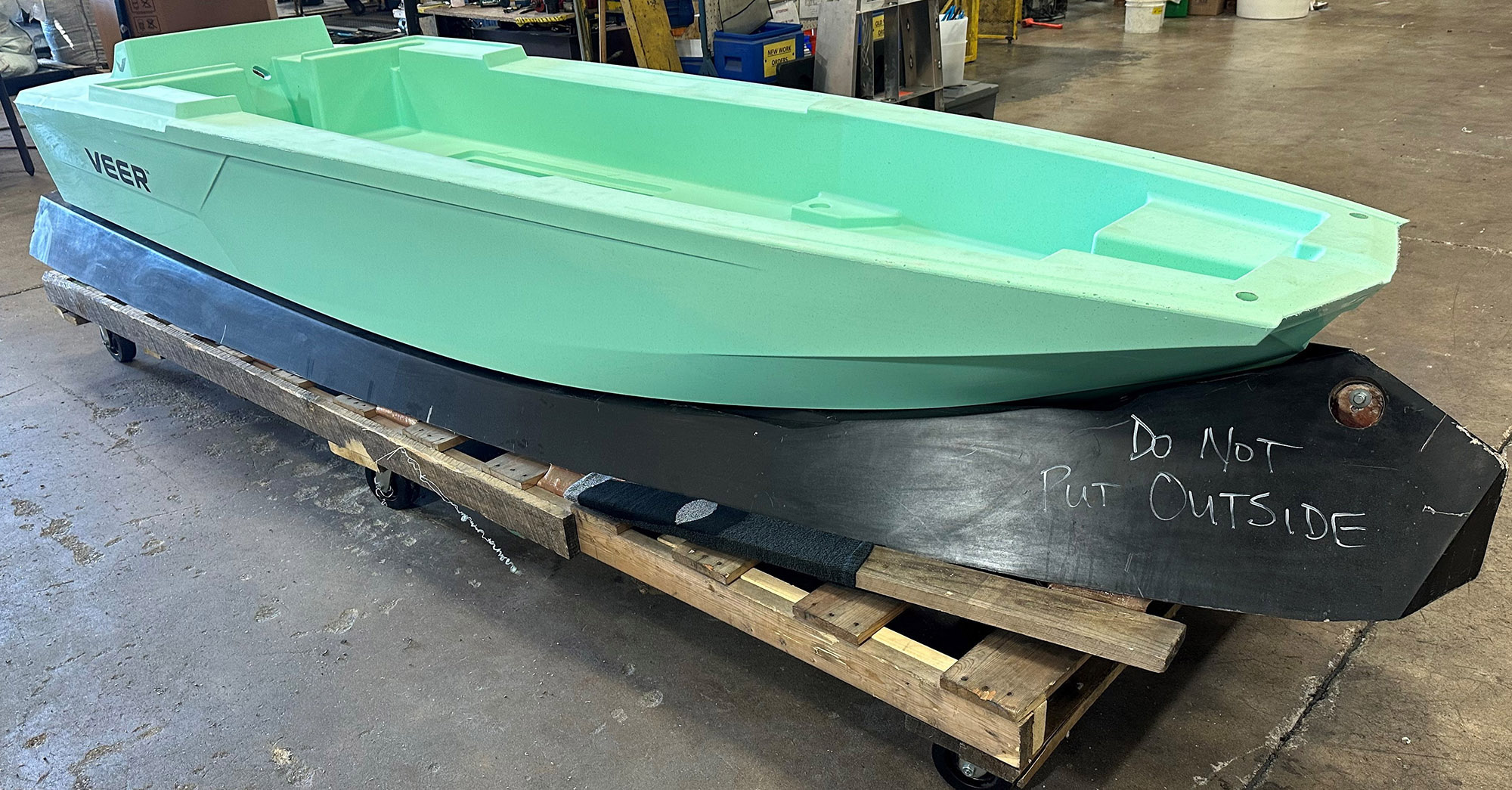
The Veer boat as it comes out of the mold.
Boating in America boomed during the Covid-19 pandemic. Some 800,000 first-time boat buyers entered the market in 2020 and 2021, according to the National Marine Manufacturers Association (NMMA). Axios reported that recreational boating saw a 35 percent increase in annual economic activity in the U.S. between 2018 and 2023, leaping to $230 billion from $170 billion, per NMMA.
U.S. sales cooled slightly in 2021, to 305,734 units, but that’s partly due to supply chain issues, which constrained inventory, NMMA said.
But still, with Veer, Brunswick hopes to ride this new consumer wave of interest.
View other IDEA 2023 stories in this series:
* Opinion Column (8/21/23): The Importance of Design
* Part 1 (8/23/23): Top honors go to Polyformer
* Part 2 (8/24/23): Retinal Camera and Digital Crop Sensor Win IDEAs
* Part 3 (8/25/23): Yamaha Hits the Right Notes with Molded Wind Instrument
* Part 4 (8/29/23): HP Leverages Recycled Materials in its Latest Monitor
* Part 5 (8/31/23): Avive’s New AED Redesigns Response to Cardiac Arrest
* Part 6 (9/6/23): Designs Meet Needs Created by Natural Disasters