Cobots to See Significant Global Growth Through 2029
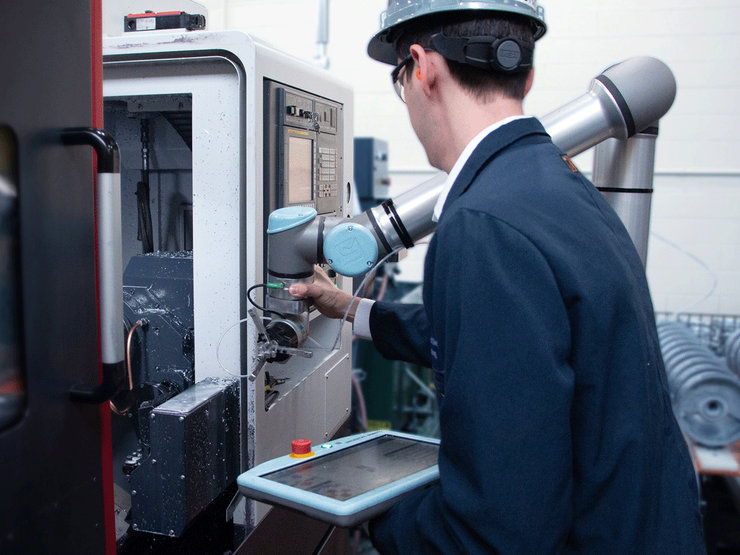
Report credits the economy of collaborative robots, safety and easy programming for the surge
Collaborative robots, or Cobots, have been used in plastics processing (and other industries) for a while. Smaller than most industrial multi-axis robots, they don’t require work cells or cages for operation and are easily programmed for repetitive tasks and, importantly, to work safely with humans. Many companies fill out their workforce with the diminutive Cobots and the trend will continue. Consultant Valuates Reports forecasts in a study that global demand for Cobots will grow to $1.35 billion in 2029 from $771 million in 2022, a compound annual growth rate of 8.2 percent.
Factors driving the growth of Cobot automation include their adaptability and flexibility, productivity improvements, cost-effectiveness, ease of programming and operation, set-up mobility and safety benefits.
Cobots also remedy chronic labor shortages, especially in redundant pick-and-place and loading jobs that humans don’t want. Cobots are suitable for advanced technology work cells and yield generally fast returns on investment.
Ease of Programming and Low Cost Attract Processors
The Valuates Reports study, “Global Collaborative Robots Market,” says Cobots are simple to assemble, disassemble and transfer across a factory without affecting production. Programming can be done by non-engineer employees, due to “kinesthetic leading” (i.e., hand guiding). Hand guiding allows a user to move the Cobot arm around in space at will by pressing a button on a teaching pendant, which is also the robot controller. The path is then logged and accessible for additional programming. Such programming is usually done in an hour.
Collaborative robots are popular with small-to-medium-sized manufacturers, especially those that create a variety of items at low volume and in short changeover time.
Cobots are less expensive than industrial robots, mostly because of their smaller size. But the report says the cost of the whole investment must be considered. It is, for example, cost-effective to do without a work cell and all that entails in hardware, labor and time. Employee training is not required, and a robotics expert is not needed to supervise or maintain operations.
Sensors Prevent Injuries When Workers Are Nearby
Each joint on a Cobot has a force sensor that responds quickly to a collision and makes the robot stop. When a human approaches a robot, extra sensors including laser sensors can be added to slow or stop the Cobot and prevent injury.
A second arm is a feature that a few businesses have introduced to Cobots. Two arms are thought to be advantageous for sensitive operations like tightening screws or assembling small pieces such as electronic components—this can speed the assembly process and increase flexibility. Another use would be parallel bin picking. With two robot arms, the task of picking small components from bins in haphazard positions can be quickly completed. However, the difficulty of synchronizing the two arms to work together is one reason why two-armed Cobots are not common.
Asia-Pacific has the largest share of the Cobot market, 54 percent, which is not surprising considering the region’s concentration of plastics and other manufacturing industries.
The major Cobot suppliers include Kawasaki, KUKA, FANUC, Rethink Robotics, ABB and Universal Robots.