Sorting Through Recycling
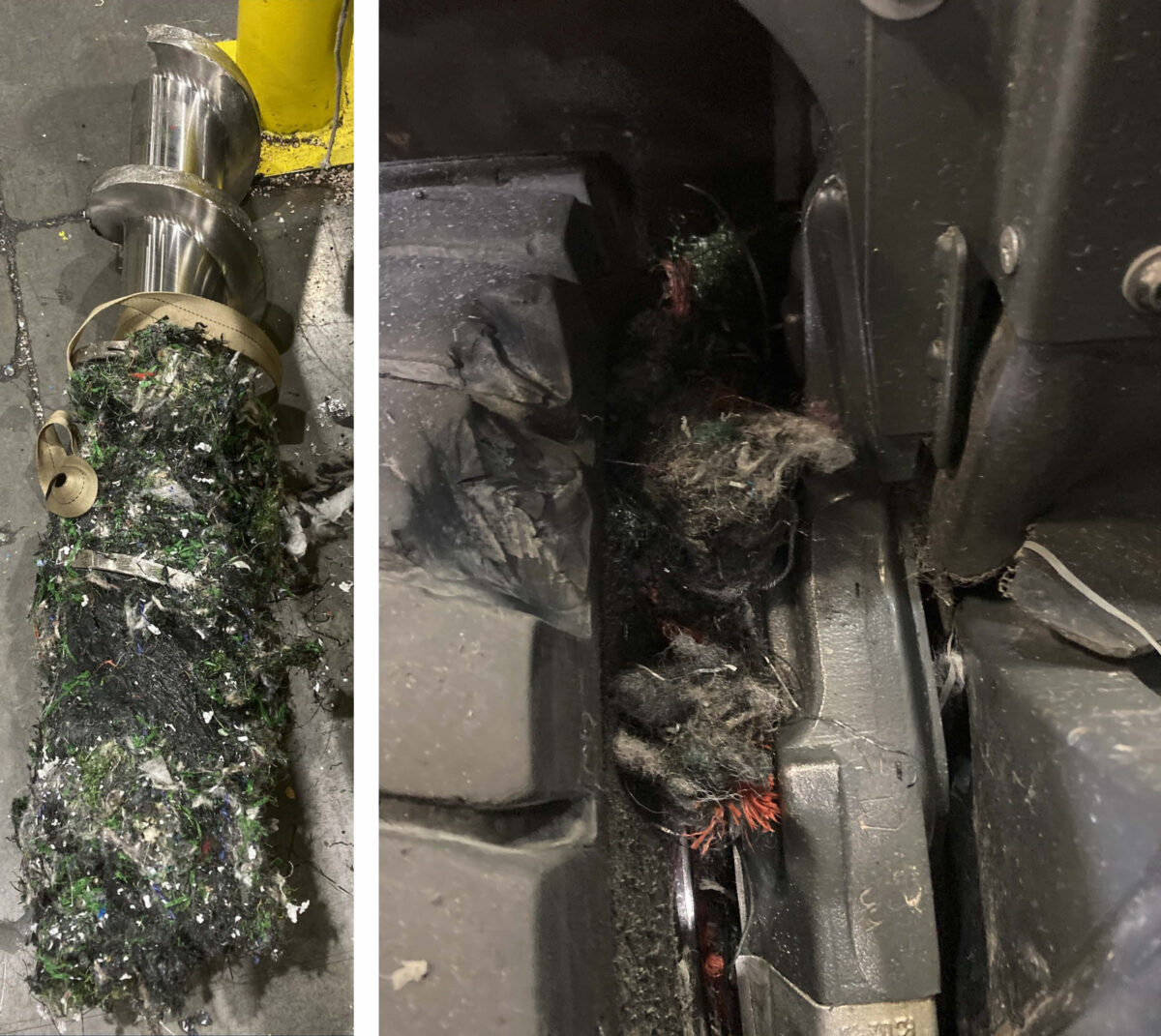
Multiple factors affect ability of suppliers to provide high-quality streams of recycled material
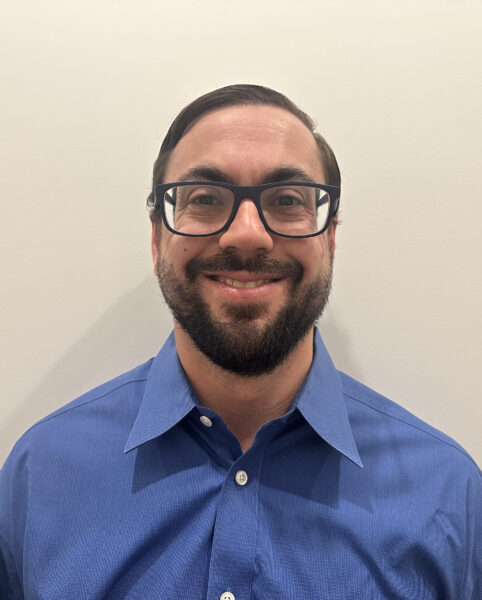
Phillip Goldberg
Phillip Goldberg, president of Columbia Recycling Corp. (CRC), is the fourth generation of his family to lead the 100-year-old waste recycling facility in Dalton, Ga. Under his leadership during the last 12 years, Columbia has expanded the volume of material it processes four-fold and established itself as a global leader in polyamide 6 and 66, homopolymer polypropylene and polyester fiber recycling.
Last fall Goldberg gave a presentation at the SPE TPO Automotive Engineered Polyolefins conference titled “The Recycling Commitment Dilemma: Today’s Plastics With Tomorrow’s Issues.” He discussed the challenges recyclers face separating and recycling plastics. Goldberg expanded on his comments in a recent interview.
The low percentage of plastics recycling in the U.S. gets bad press. Why is recycling so low?
First, there’s a patchwork of local, state and federal laws that constantly change. For example, Colorado has a law (HB1162) banning single-use plastic bags. Connecticut has a law (SB928) specifying a minimum recycled content policy. And Maine has a bill (LD1541 EPR) requiring packaging suppliers to pay into a stewardship program for products sold in that state.
On the business side, companies and trade groups promise greater recycled content in products. For example, Volvo pledges to use 25 percent recycled materials in its cars by 2025; Coca-Cola says all its plastic bottles will contain an average 50 percent recycled content by 2030; and the American Plastic Bag Alliance pledges that bags produced by members will contain at least 20 percent recycled content by 2025.
However, many of these promises were made before secure sources of reliable materials were found and regional recyclers were identified in order to ensure there’s a steady supply so companies can keep those commitments. The disorganized way we’re going about this at both the government and industry level is one of the biggest challenges we face and it’s a chief cause of disappointments.
Is it a matter of educating the public or are bigger issues involved?
First, you have to distinguish between post-consumer and post-industrial recycled (PCR, PIR) materials. While PCR gets the greatest attention and is considered the most valuable in the circular economy, PIR is often cleaner and a larger source in terms of accessibility and consistent supply.
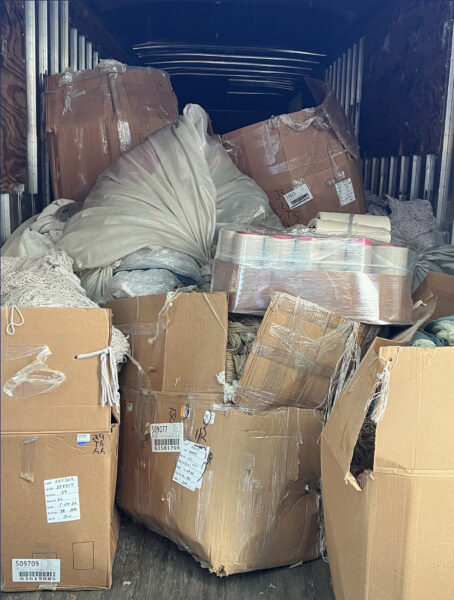
Recyclable or garbage? Recyclers often receive commingled materials that need identification before separation and recycling. Photos courtesy of Columbia Recycling Corp.
The problem is that companies aren’t well set up to sort their own waste. So, recyclers like Columbia end up with an entangled mess that needs hand sorting to ensure 100 percent purity, as automated sorting methods can only go so far in accuracy. It’s not that it can’t be done, but that it’s expensive and slow to recover material that way.
At times, this creates hard-to-explain costs, as many companies compare pricing of recycled to virgin. Complicating matters is that recycled products offer lower performance. Why would a company pay more for a lesser-quality product?
All waste recyclers must face these challenges and still make money, or they won’t remain in business.
What challenges does a recycler like Columbia face?
We face four tough issues at the same time. I’d describe them as relationships, handling, quality and labor. Given that the waste recycling industry has long operated on a price-per-pound basis, companies seeking recycled supply streams—especially plastics streams—don’t like to make long-term commitments as they prefer to shop the market for the lowest price.
The problem is that to ensure a company like mine can support a big program long term, I have to find a consistent source of material that my team can get to our facility and separate, meaning I have to make a contract to take back someone else’s waste material. Then I have to hire and train the people needed to ensure that material is properly separated, tested, upcycled and repackaged for a customer’s use. I can’t do that when companies only commit to short-term contracts.
It really comes down to customer treatment. If you’re a user who wants a consistent source of quality recycled material, you have to treat your recycler as though he were a valued member of your supply chain. This means making long-term contracts and paying a fair price for material, so the recycler remains profitable enough to supply your program. At CRC, we target long-term, mutually beneficial relationships, but they’re not always easy to develop.
Handling is another issue and a nightmare at times. We’re in the South so we source a lot of textiles. Every day we receive semitrucks full of spools of thread on cardboard tubes—often shrink-wrapped and in cardboard boxes. In this case, there are four different materials to separate and recapture. These materials may not be consistent in color, pattern or polymer type, and it’s not always possible or desirable to separate them just based on visual inspection. At other times we get a mix of loose materials scattered throughout the trailer.
Another problem is that companies we source materials from aren’t always disciplined about what they throw in the truck, and that can damage our equipment and create safety concerns for our people. I’ve seen everything from knives to wood to old furniture contaminating the load. If an item is found in a plant, we’ve probably found it mixed into materials we’re asked to recycle.
Since every manufacturer wants guaranteed quality for the price they pay, that means we need to run an in-house lab to identify and segregate materials. And then we need in-house expertise to upcycle waste materials back to the quality the customer demands. Not every customer has reasonable expectations about finished product quality or color. In fact, color can be a real issue. The reason most high-volume recycled products are gray or black is because we’re often left with source material in dozens of different colors.
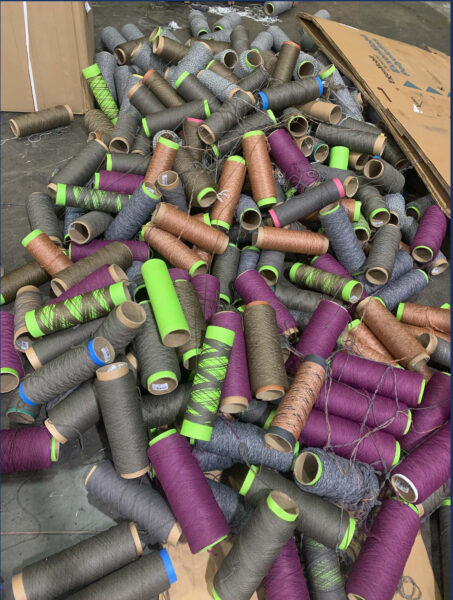
CRC often gets polymer thread on shrink-wrapped cardboard spools in boxes, which increases separation issues.
Finally, labor shortages are an ongoing issue. When customers are reluctant to sign long-term supply contracts with us, this issue can create challenging scenarios. Since the bulk of our employment tends to be unskilled jobs, people come and go, so it’s hard to ensure you have the right people to handle each batch of waste that comes in each week. It’s a fact that these are challenges all recyclers face and they make efficient, consistent and cost-effective recycling of plastics more challenging in a big country like ours.
How do we increase U.S. recycling as consumers and members of the plastics industry?
For starters, we need a multilayer, multifaceted approach and we need to be more understanding. It takes time to create systems to source, sort, recycle, upcycle and ship quality recycled product to customers, especially on a regional and national scale. And it’s harder to do with plastics than other materials given the sheer number of thermoplastics used in industry.
How do we protect the environment and ensure plastics remain available for companies wishing to use them?
The immense growth of plastics over the last 50 years and the lack of planning on how to recover and reuse them have led to significant amounts of plastics waste polluting the planet. The only way to address society’s concerns while lessening the plastics industry’s global waste footprint is to have open dialogue among all members of the circular economy. We have to honestly discuss the real problems different groups face and then develop practical and fair solutions that lead to significant increases in recycling to have the impact we want and need to achieve.