Rethinking Composite Safety in Deep-Ocean Submersibles
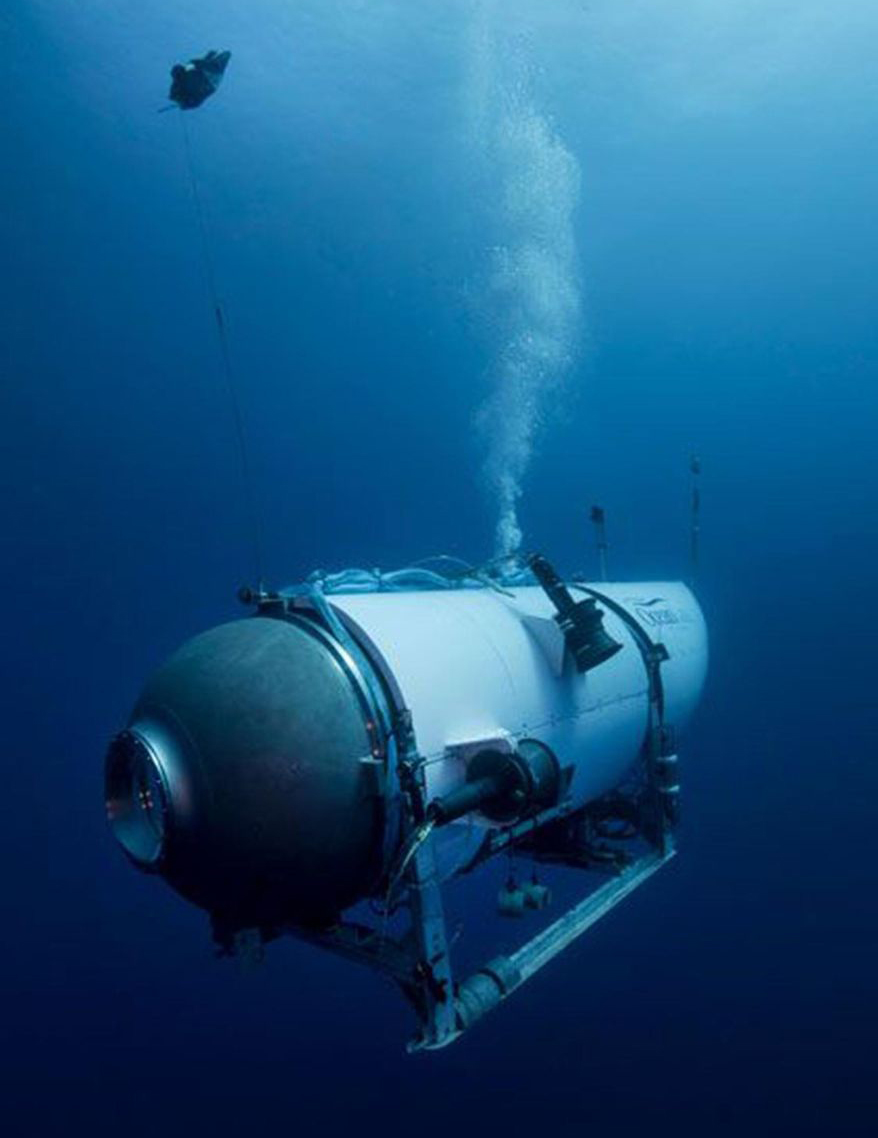
New findings from the OceanGate submersible incident reignite the discussion around composite safety standards for deep-sea transport applications.
On June 18, 2023, the implosion of OceanGate’s Titan submersible reignited debate over using carbon-fiber composites in deep-sea exploration vehicles. Although Titan had completed 24 successful dives, critics emphasize that extreme pressures—6,000 psi at 3,800 meters—can reveal material weaknesses in composites. Supporters maintain that carbon-fiber structures are safe with proper testing and inspection; yet, growing expert scrutiny challenges that belief. Recently released findings and a new Netflix documentary have revived concerns about the failure of composites in such demanding underwater applications.
You can also read: Basalt Fibers in Marine Composites: A Reliable Solution?
New Evidence Reveals Structural Defects
Recently, NTSB and Coast Guard officials revealed Titan’s carbon-fiber hull had voids, wrinkles, waviness, and adhesive-layer delamination. Because these flaws weaken structural performance, they could be precursors to failure under sustained deep-ocean compressive forces. Moreover, acoustic sensors had recorded a loud “bang” during a 2022 dive, later identified as hull delamination under stress. Although this warning was significant, OceanGate continued operating the vessel without full inspection or structural remediation.
See also the interview with OceanGate CEO Stockton Rush by CBS News on June 25:
Deeper Analysis Exposes Certification and Testing Gaps
In addition, experts highlighted Titan’s lack of third-party certification and limited use of non-destructive testing like ultrasound scanning. OceanGate relied on in-house monitoring systems, which may have failed to detect microcracks forming inside the composite layers. Therefore, without external inspection or regular scanning, undetected damage likely accumulated across repeated dives at high pressure. These micro-failures may have propagated within the hull structure, leading to a sudden and catastrophic collapse under stress.
Engineering Responds with Better Materials and Models
In response to this tragedy, researchers are improving composite design with gradient layups and matched thermal-expansion resins. Because inter-layer stress is a common failure point, such innovations aim to reduce deformation and delamination over time. At the same time, engineers are implementing real-time strain monitoring to detect early signs of material fatigue. This proactive data monitoring complements visual inspections and ensures safety during repetitive deep-sea missions. Furthermore, current research highlights thermoplastics like carbon-fiber reinforced PEEK as a stronger alternative to thermosets. Thermoplastics offer fracture toughness ten times greater, which improves resistance to cracks and sudden structural failures. Notably, laboratory testing has confirmed that thermoplastic composite tubes can endure more than 600 bar of pressure. These results indicate strong potential for thermoplastic composites in future human-rated submersible designs.
Learning from Titan: Toward Safer Best Practices
The Titan disaster provides a critical case study in marine composite safety, testing protocols, and material selection. Experts now emphasize the importance of robust inspection methods that combine real-time data, ultrasound scans, and acoustic feedback systems. At the same time, engineers continue to stress the value of third-party design certification to independently verify the structural integrity of submersibles. Additionally, there is growing attention on the need for fracture-resistant materials, particularly for deep-sea exploration vehicles carrying people. Oleksandr Kravchenko of Old Dominion University believes that composites can be safely used in submersibles if guided by sound engineering practices. He points out, however, that thermoset prepregs are relatively brittle and prone to delamination under extreme environmental loading. Since delamination can lead to catastrophic failure, thermoplastics may offer a safer alternative for high-pressure underwater environments.
Would Thermoplastics Have Prevented the Implosion?
Kravchenko notes that similar concerns have led NASA and others to explore continuous thermoplastic prepregs for aerospace applications. Thermoplastics such as polyetheretherketone offer significantly higher fracture resistance, providing greater toughness under load and reducing the likelihood of structural failure. Therefore, incorporating these materials into submersibles could greatly improve both safety margins and durability. So far, the marine sector has not widely adopted composites for human-occupied vehicles, in part due to concerns about long-term reliability. Kravchenko sees the Titan tragedy as a potential turning point—one that highlights the need for stronger, better-characterized composite systems. As a result, the disaster could help accelerate the development of marine-grade thermoplastics and improved certification frameworks for future deep-sea vehicles. He concludes that Titan’s loss should prompt engineers to reconsider both the capabilities and limitations of composite materials. Ultimately, future designs must address known weaknesses while meeting the structural and operational demands of deep-sea environments.
Conclusion: A Turning Point for Undersea Composites
Ultimately, the Titan tragedy underscores a key truth: carbon-fiber composites remain promising, yet misunderstood under deep-ocean compression. As a result, the industry is now poised to evolve through smarter materials, better design practices, and independent validation. We will likely see new composite layups, expanded use of thermoplastics, and routine non-destructive testing as industry standards. Only through such improvements can composites safely support future undersea missions—transforming loss into meaningful progress.