Dumb Machines Can Be Smart
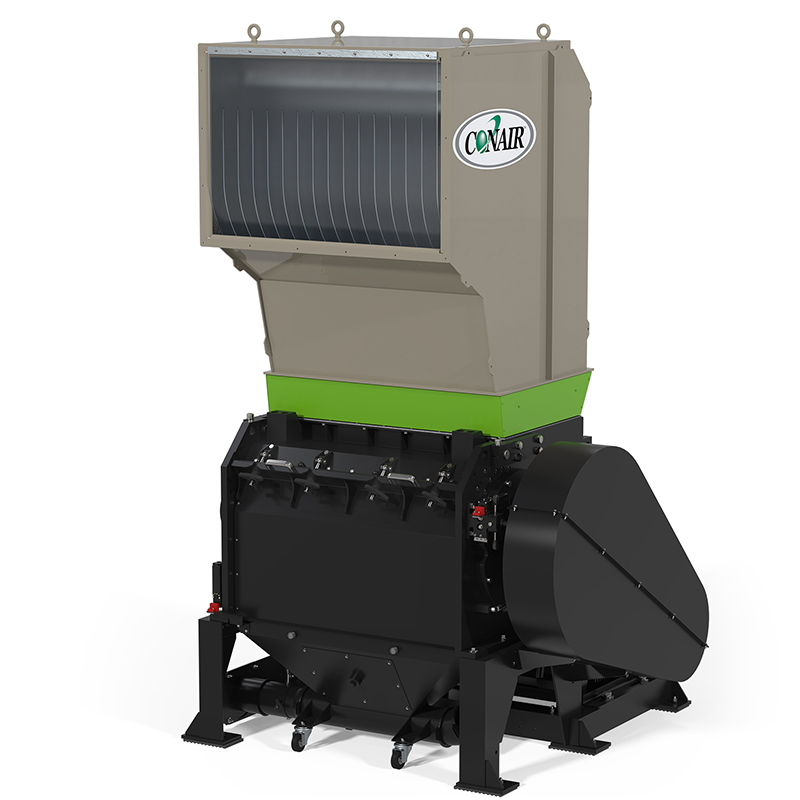
Granulators are low-tech outliers in the factory of the future, but advanced controls will make them more effective
Most granulators work separately from primary processing lines. It’s usual for granulators and shredders to be installed in a room or enclosed section of a plant away from production and operated by workers who periodically feed scrap into them for downsizing.
Exceptions exist, of course: many injection molders automatically feed low volumes of mold scrap to small beside-the-press granulators, while high-volume film and sheet extruders and thermoformers often position large granulators and shredders next to machines, even below them, to downsize massive amounts of scrap for reuse in a process or other needs.
Few processors, though, think about “smart” controls for granulators, much less Industry 4.0 connections to machines in a work cell. This may change.
Machine supplier Conair Group is evaluating the potential use of smart controls on granulators (and other auxiliary equipment), most likely the largest models, which Dave Miller, general manager of size reduction, says are already equipped with sophisticated control panels. However, Miller notes that Conair is only now analyzing what operations might benefit from smart controls and how to implement them most effectively.
For many granulators, Industry 4.0-type smart controls or even integration within work cells would probably be overkill considering that the only function of the machines is to downsize scrap. “For the most part a granulator hasn’t changed much over the years,” Miller says.
But for processors in high-manufacturing-data industries like automotive and medical, who compile detailed reports on the materials they use for production, the ability to monitor granulator or shredder operations in real time and schedule preventive maintenance without affecting primary machines could be worth an investment in advanced controls. The same is true for converters that downsize thousands of pounds per hour of film and sheet scrap. “The larger and more complicated the granulator [or shredder] is, the less the cost for advanced controls will mean,” Miller remarks.
To get an idea of what might be involved in developing smart controls for granulators and shredders, Plastics Engineering sought input from Conair about what controls might be needed and the benefits they would provide.
Sizing Up Need
Miller says that smart equipment controls and the future of Industry 4.0 technology are hot topics in the plastics industry. But realizing the vision of Industry 4.0—the seamless exchange and processing of data using intelligent machines that self-adapt and optimize processes autonomously—is very much in the future, not only for primary processing equipment, but for many pieces of auxiliary equipment, including size-reduction units.
How might processors determine if they need advanced controls on granulators and shredders?
“Whether a piece of equipment requires digital controls that monitor performance and trigger alarms for unusual conditions today, or that self-adapt equipment behavior in response to changing process conditions tomorrow, really depends on how critical the equipment is to operations,” he says.
In the case of granulators or shredders, the need for digital controls and for future Industry 4.0 capability probably comes down to whether granulation and shredding operations are in-line and integral to ongoing operations or can remain offline.
If operators simply toss scrap into bins and granulate it offline when they have time, there may not be value in a granulation system with sophisticated digital controls, sensors or alarms. “You need a granulator that turns on, runs and processes scrap when needed. Should the throughput of that granulator decline due to blade wear or the need for maintenance, you can live with the delay. The accumulation of ungranulated scrap isn’t slowing operations or costing you essential production materials,” Miller explains.
The types of processors who would benefit from smart controls on size-reduction equipment are users who need and value the data provided by more advanced PLC-based controls, and who may be looking forward to what Industry 4.0-capable controls might bring. Miller says these users are chiefly:
- High-volume film producers. If they’re running film lines at 3,000 to 4,000 pounds per hour, they’ll need in-line granulating processes because those lines generate a lot of edge and trim scrap and there’s no good place to put it. Some of these processors put granulators directly below the line to efficiently capture and granulate scrap and live-blend the material back into the process.
- Thermoformers. The companies that make containers from continuous sheet generate scrap in the form of “skeletons,” start-up scrap and off-spec product.
- Recyclers. Maintaining high throughput is everything in a recycling operation. Recyclers can’t afford unexpected downtime or having to take a key shredder offline for major repairs.
“These processors must rely on size-reduction equipment to be available and ready when needed,” Miller says. “Smart control features, monitors and alarms are important for tracking performance and keeping ahead of maintenance problems.”
For some time, makers of size-reduction equipment have been monitoring key factors of equipment performance, such as amperage, heat and vibration using PLC (programmable logic controller)-based systems, he notes. “These data—and a lot of practical experience—show that when any of these factors start moving beyond normal or baseline levels, something is likely going wrong.”
Advanced granulator controls will offer alerts or alarms when motors are drawing above-normal amperage, cutting chambers are getting hotter or internal vibrations are higher than usual. The problem could be that the hardness of the material being granulated has changed and is taxing the capacity of the granulator more than usual. Or the alarms could signal that the blades are getting dull or that lubrication and belt adjustments are needed.
For shredding equipment equipped with PLC controls, the most common things to monitor would be motor amperage for the shredder shaft and hydraulic pressure in the feed mechanism that pushes material into the shredder. When shredder blades are new, motor amperage is going to run in a baseline range, such as 30 to 40 amps, Miller advises.
“If you see an alarm that motor amps are rising suddenly, you can use digital controls—manually or automatically—to temporarily reduce the hydraulic pressure in the feed mechanism until the amps come down. Then, higher feed pressure can resume. However, if motor amps are consistently running in a higher-than-baseline range, say 40 to 50 amps, it’s a good indication that either new blades or other maintenance are required,” he says.
“Smart, PLC-based monitoring functions like these weren’t developed with Industry 4.0 in mind, but rather because processors with critical size-reduction challenges need to know how equipment is performing and detect potential problems as early as possible, so they can schedule troubleshooting and maintenance and avoid outages or throughput problems,” Miller adds.
Setting Capabilities
What will it take, then, to develop Industry 4.0-capable controls for size-reduction equipment? Miller says that discussions at Conair are underway about what future granulators and shredders will look like and how they will operate. There is, as a result, a great deal of focus on what capabilities controls should have and what they would be able to do.
Conair has SmartServices, a cloud-based Internet of Things or Industry 4.0 solution for machine monitoring and data collection. The controls that Conair developed or is developing for auxiliary equipment such as dryers, chillers and material-handling systems are compatible with the SmartServices platform and dashboard. Any advanced control that might be developed for granulators would be compatible with the platform as well.
Miller says that developing smart controls for granulators will happen in increments. The first phase would be specifying—or designing—a small PLC that records data from internal sensors that monitor select actions. These include movement, which indicates how well scrap is processed by the granulator. Miller says PLCs are available now for control, but they don’t analyze data and predict likely outcomes based on what’s happening in the machine. That would involve writing an algorithm that could forecast the need for sharper cutting surfaces, blade replacement and other critical issues.
Control actions could also include monitoring and regulating machine temperature during operation, amperage levels and vibrations, which indicate rotor speed and cutting efficiency.
The next phase, he says, would be collecting operational data for analysis and determining what the data predict could happen to granulator or shredder throughput if baseline values deviate from setpoints.
Miller makes clear that there’s a huge difference between where we are today—with individual computerized controls that monitor things like temperature, amperage and vibration on a piece of equipment and indicate when those are changing more than expected—and a whole class of equipment and controls with the capability to scan real-time sensor data, actively predict or identify a problem based on those changes, and go on to recommend that plant personnel take corrective action. “Most Conair shredders use PLCs, but we’re not at a point where we collect data with them,” he notes. “Most granulators do not come standard with PLCs. We’ve supplied them, but it’s a very customer-driven option—they have a much greater need for I/O reporting.”
The main difference between smart controls and what’s available today, is that it takes the collection and analysis of huge amounts of data over a long period of time, followed by the development and testing of computer algorithms, to make a control with predictive capabilities. “But that is where the future of Industry 4.0 lies,” he says.
Miller adds that such predictive capabilities will be very important for some categories of auxiliary equipment, but he’s not sure how broadly smart or Industry 4.0 controls will be adopted for granulators and shredders.
“The processors who need them will know it and be willing to invest. And those controls will be available. But there will always be a lot of processors who want grinders that they can buy, turn on and forget about,” he says. “For them, the added cost of the controls, alarms or predictive capabilities aren’t justified.
“When I think of the smart granulator control that would be perfect for them, I think of an inexpensive plug-in module that would simply indicate when blade changes or adjustments are needed. I think that would be a feature that virtually every processor would find valuable, regardless of the size or complexity of the machine. But alas, it doesn’t exist today.”